Understanding Welder Hourly Rates: Insights and Implications
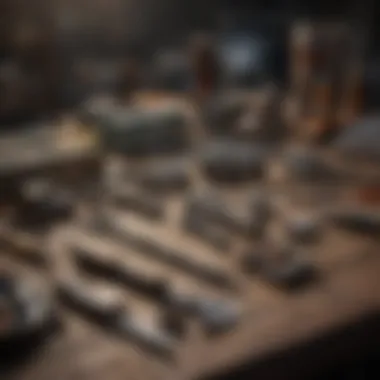
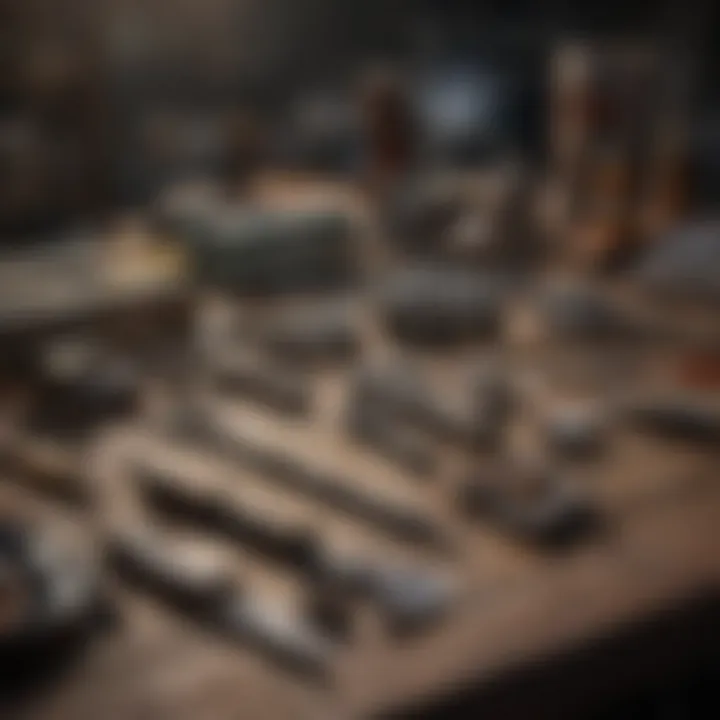
Intro
The welder profession plays a crucial role in various industries, significantly influencing the construction, manufacturing, and automotive sectors. Understanding the factors that determine welder hourly rates is essential for both welders and employers. This article provides a comprehensive examination of the elements affecting compensation, from geographical variations to market demand. In this exploration, we will discuss the relevance of skills and certifications, wage trends, and career prospects to equip readers with valuable insights.
Key Concepts and Terminology
Basic Definitions
In the welding industry, several key terms are essential to grasp. The welding process refers to the method of joining materials, typically metals, using heat or pressure. Hourly rates signify the compensation welders receive for their labor on an hourly basis. Factors influencing these rates include geographical location, skill level, and demand for specific types of welding.
Historical Context
Historically, welding evolved from manual techniques to more sophisticated methods. The introduction of electric welding in the early 20th century transformed the industry. As industries advanced, so did the complexity of welding techniques and, consequently, the compensation associated with them. Understanding this evolution provides context for today's pricing structures.
Factors Influencing Welder Hourly Rates
- Geographical Variations: Different regions have unique economic conditions influencing wages. Urban areas tend to offer higher rates than rural zones due to demand and cost of living. For example, welders in cities like San Francisco and New York may command much higher hourly rates compared to those in smaller towns.
- Skills and Certifications: Specific welding techniques require specialized training and certifications. Welders with certifications from recognized institutions, such as the American Welding Society (AWS), often enjoy higher hourly rates. Skills in advanced welding techniques, such as TIG or MIG welding, also come with premium compensation.
- Market Demand: Market demand fluctuates based on industry needs. For instance, an increase in construction projects or infrastructure development often leads to higher demand for skilled welders, subsequently raising their hourly rates.
"The welding industry, with its ever-evolving technology and techniques, determines hourly rates in a dynamic manner influenced by market needs."
Recent Innovations and Trends
Technological Advancements
With the rise of technology, effective welding practices have transformed. Automation and robotics are increasingly integrated into welding processes, allowing for greater efficiency and precision. Despite this, skilled human welders remain essential, particularly for complex tasks.
Sustainable Practices
Environmental concerns are influencing industries globally. Welding practitioners are adopting more sustainable practices, which can impact hourly rates. Welders who are familiar with eco-friendly techniques may find themselves in greater demand, thus securing better compensation.
Practical Applications and Techniques
Step-by-step Guides
Welder training often includes step-by-step guides for learning different techniques. Proficiency is built on understanding equipment, safety measures, and welding fundamentals.
Case Studies
Analysing specific cases can provide a clearer picture of compensation patterns in different fields. For instance, examining hourly rates of welders in aerospace versus those in construction can reveal significant differences that are influenced by skill requirements and market demand.
Through this examination of welding hourly rates, a deeper understanding of the professional landscape emerges. Welders are not just technicians; they are vital contributors to industry advancement and development. Recognizing their economic value is essential for sustainable growth in the profession.
Prelude to Welder Hourly Rates
Understanding welder hourly rates is crucial for both welders and employers. For welders, knowing how compensation is structured can lead to informed career decisions. For employers, being conscious of these rates allows for budgeting and strategic hiring. Various factors contribute to compensation in this field, influencing how much one earns.
A significant aspect includes the geographical location. Different regions may offer varying rates due to economic conditions. Furthermore, the complexity of the work and the skills required play a role. Skilled welders, especially those with certifications, often command higher wages.
Another important factor is the type of industry in which welders operate. Work in construction, manufacturing, or automotive sectors can yield different pay scales, necessitating an exploration of the nuances in each area.
Government policies and market demands also affect welder pay. In times of economic growth, the demand for welding may rise, leading to increased rates. Conversely, during economic downturns, such compensation may stagnate or decrease.
Welders should consider these elements when negotiating wages or selecting job opportunities. Employers benefit by remaining competitive while attracting skilled individuals. Identifying and understanding the details surrounding welder hourly rates can guide both parties towards fairer pay practices in the welding profession.
The Basics of Welder Compensation
Understanding welder compensation is essential for both employers and welders themselves. It not only affects job satisfaction but also influences the talent pool available for various industries. In this section, we will discuss two critical components: the hourly rate and the various welding positions. Both these factors play a direct role in determining overall compensation and offer insights into the welding profession's landscape.
Defining the Hourly Rate
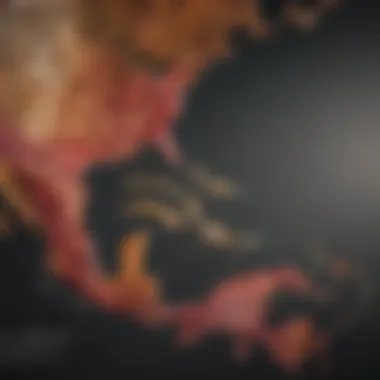
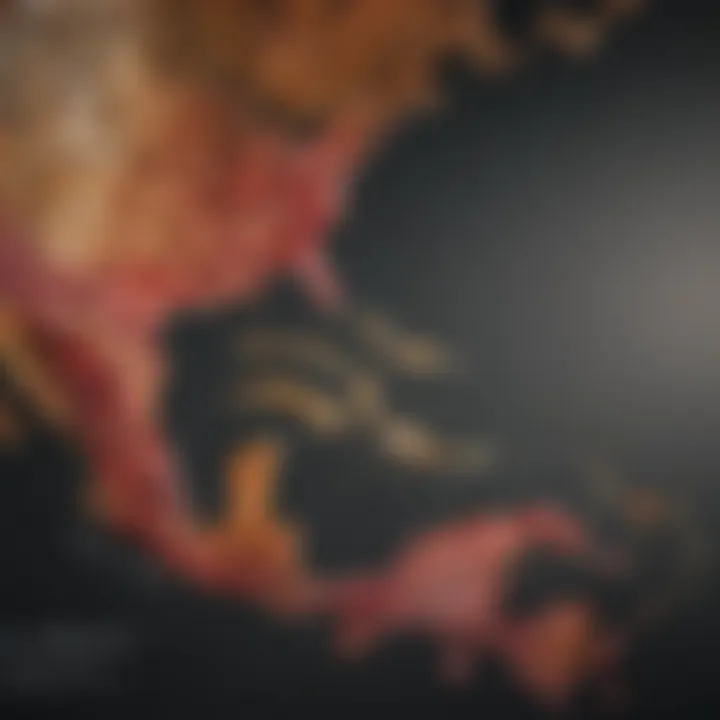
The hourly rate is a key aspect of welder compensation. It defines how much a welder earns for every hour of work performed. This rate can fluctuate significantly based on various factors such as geographical location, years of experience, and specialization.
For instance, in some urban areas like Chicago, the demand for skilled welders drives up hourly wages compared to more rural areas. Understanding this rate helps welders negotiate better salaries and helps employers budget accordingly.
Factors influencing the hourly rate:
- Geographical Location: Rates can vary from one state to another.
- Skill Level and Experience: More experienced welders generally command higher rates.
- Industry Specifics: Certain industries may offer better pay due to higher risks or demand.
It's also important to consider that hourly rates do not always directly correlate with overall earnings. Factors such as overtime pay and benefits may also play a significant role.
Different Types of Welding Positions
Welders occupy various positions, each with distinct responsibilities and skill requirements. The type of position can significantly impact compensation. Here are some of the primary types of welding positions:
- Structural Welder: Typically works on building frameworks, earning a competitive wage.
- Pipe Welder: Specializes in welding piping systems, often requiring specialized certifications.
- MIG/TIG Welder: Uses different techniques for metal inert gas or tungsten inert gas welding, with varying pay scales based on demand.
- Fabricator: Combines welding and fabrication skills, usually paid well for their versatility.
Each position has unique skill sets and is crucial in various industries, including construction, manufacturing, and automotive. Understanding these roles can help aspiring welders choose the right path.
"The type of welding position can affect both earnings and job satisfaction for welders. It is essential to align skills with the right opportunities."
Recognizing the significance of these basics helps both employers and welders make informed decisions regarding employment, projects, and salary negotiations.
Factors Influencing Welder Hourly Rates
Welding is a highly skilled trade, and understanding the factors that influence welder hourly rates is crucial for both workers and employers. Several elements come into play when determining how much welders earn per hour. These factors include geographical variations, skill level, experience, and industry demand. By examining these aspects, one gains a clearer picture of the economic landscape welders navigate. This article aims to provide insights into these factors and their implications for welding professionals and employers alike.
Geographical Variation
Urban vs. Rural Rates
The distinction between urban and rural areas is significant when discussing welder hourly rates. Urban regions generally offer higher wages compared to rural locations. This is often due to the concentration of industries and larger projects in cities, necessitating a higher skilled workforce. Employers in urban settings face fierce competition for qualified welders and thus are willing to pay more to attract talent. The demand is high, leading to increased earnings for welders willing to work there.
On the flip side, rural areas may have lower wages but often come with advantages like lower living costs. However, the number of available positions may also be fewer. This could be a consideration for welders evaluating their career locations.
Regional Economic Differences
Regional economic differences further illustrate the variance in welder hourly rates. Areas with booming economies, particularly those with construction booms or robust manufacturing sectors, tend to compensate welders more competitively. For example, states with substantial infrastructure projects often have higher wage standards for welding professionals.
Conversely, regions struggling economically may not offer as many opportunities and therefore provide lower pay rates. This economic backdrop shapes the local job market, affecting wages significantly. Welders need to be aware of these regional disparities when seeking employment, as they could influence overall earning potential.
Skill Level and Experience
Entry-Level vs. Experienced Welders
The distinction between entry-level and experienced welders is essential in determining hourly rates. Entry-level welders typically begin with lower wages as they are just starting their careers and require training and experience. They might be subject to lower pay until they can demonstrate proficiency in their skills.
Experienced welders, on the other hand, command higher rates due to their vast knowledge and expertise. They often have a fine-tuned set of skills, allowing them to handle complex projects efficiently. This experience translates into higher compensation as employers recognize the value of their competencies.
Specialized Skills and Certifications
Specialized skills and certifications in welding can significantly influence hourly rates. Welders with certifications such as those from the American Welding Society often enjoy higher pay. Specializations like TIG welding or underwater welding are particularly lucrative and can lead to increased opportunities in niche industries.
Certifications validate a welder's skills and can often result in better pay and job security. For employers, hiring certified welders means assurance of quality work, which in turn influences their compensation strategies. It is important for welders to consider obtaining relevant certifications to enhance their earning potential.
Industry Demand and Supply Dynamics
Impact of Economic Cycles
Economic cycles play a crucial role in determining welder hourly rates. During economic booms, industries such as construction and manufacturing see increased demand for welders, often driving wages up. Conversely, during economic downturns, demand may drop, resulting in wage stagnation or reductions. This cyclical nature of the economy influences both hiring practices and the financial sustainability of welding jobs.
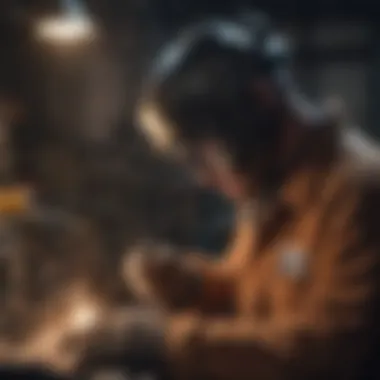
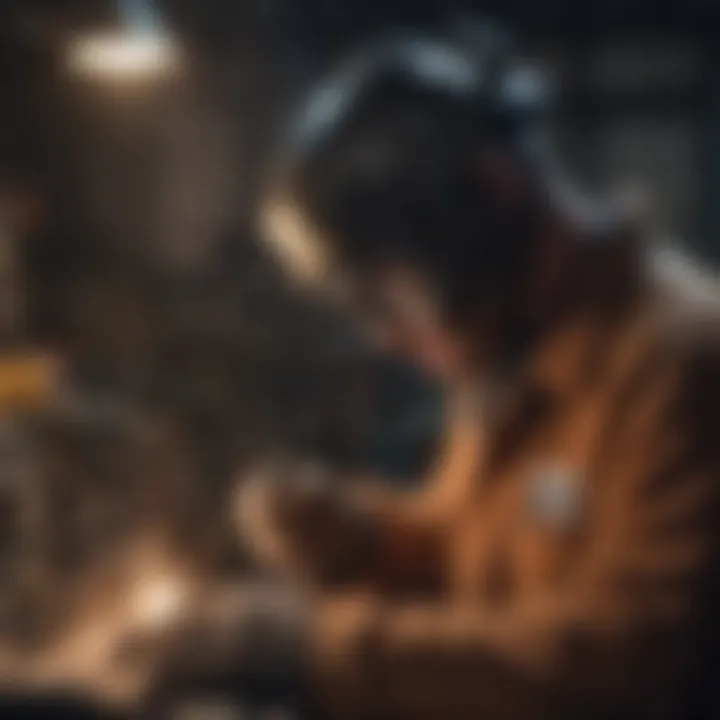
Employers must stay informed about these economic trends. Understanding when to hire or when to offer wage increases can help companies maintain a competitive edge in attracting skilled welders.
Trends in Construction and Manufacturing
Current trends in construction and manufacturing can also dictate welder hourly rates. For instance, if architectural firms are designing large scale projects, or if manufacturing sectors are investing in new technologies, the demand for welders naturally increases. Understanding these trends can help welders situate themselves in growing areas of the market, thereby enhancing their earning capacity.
Understanding the economic landscape and how trends affect welding jobs is crucial for welders and employers alike. Identifying opportunities based on economic indicators can be beneficial.
Welding Certifications and Their Impact
Welding certifications play an essential role in determining welder hourly rates. With a competitive job market, these certifications distinguish a welder's qualifications and expertise. Recognized certifications like those from the American Welding Society (AWS) or the National Center for Construction Education and Research (NCCER) signify that a welder has met industry standards. This acknowledgment can bring higher pay and better job opportunities. In essence, certifications serve as proof of a welder's skills, compelling employers to consider these factors seriously when setting compensation rates.
Overview of Welding Certifications
Welding certifications vary widely, encompassing different processes and techniques. At its core, a certification validates a welderβs skills in specific types of welding, such as MIG, TIG, or Stick welding. Each certification process typically involves both a theoretical examination and a practical welding test. Furthermore, these certifications are often time-limited, requiring welders to recertify periodically to maintain their credentials.
Some prominent organizations offering certification include:
- American Welding Society (AWS): Offers a variety of certifications for different welding processes and industries.
- National Center for Construction Education and Research (NCCER): Focuses on career development in construction.
- Canadian Welding Bureau (CWB): Offers certifications for welders in Canada.
Certifications not only validate a welderβs skills but also signify a commitment to professionalism and safety in the trade. This can enhance a welder's reputation in the industry, potentially leading to increased earning potential.
Value of Certification in Salary Negotiation
Holding a valid welding certification can be a significant asset during salary negotiations. Employers often see certified welders as more reliable and skilled, which can justify higher pay. For instance, a welder certified by AWS may command a higher hourly rate compared to non-certified peers. This premium reflects the investment made in acquiring the certification.
Several reasons highlight the value of certifications in wage negotiations:
- Increased Trust: Employers view certified welders as trustworthy professionals.
- Wider Job Opportunities: Many employers specifically seek certified workers, expanding job options.
- Negotiation Leverage: Due to higher perceived value, certified welders can negotiate better pay than those without certificates.
Indeed, having the right certifications can fundamentally alter the earning power of a welder. As the industry evolves and technology advances, the importance of obtaining and maintaining certifications will continue to rise, impacting hourly rates across various sectors.
Comparing Hourly Rates Across Industries
Understanding the differences in welder hourly rates across various industries is essential for both workers and employers. Knowing where welders can earn the most can guide career decisions and inform hiring strategies. Furthermore, it allows professionals to assess their skills and negotiate effectively. Each industry presents unique demands, which influence pay scales. By comparing rates, one can recognize trends, associate them with the industryβs needs, and leverage insights for better compensation.
Manufacturing Sector Rates
The manufacturing sector is a critical area for welders. It encompasses a wide range of operations, including metal fabrication and assembly. The hourly rates for welders in manufacturing can vary significantly based on several factors. These include the complexity of the work and the materials involved. Typically, welders with specialized skills, like those able to work with stainless steel or aluminum, command higher wages due to their expertise.
Additionally, the scale of the manufacturing operation plays a role. Large factories may offer higher pay rates due to increased demand for skilled labor. According to recent data, the average hourly rate for welders in this sector can range from $18 to $35, depending on experience and skill level.
Construction Sector Rates
Welders in the construction sector face a different set of challenges and pay rates. This field often requires physical strength, endurance, and the ability to work in various conditions, whether outdoors or on scaffolding. On average, welding jobs within construction can bring hourly wages between $20 and $30. However, emergency work or urgent projects may offer premiums for welders willing to take on high-pressure tasks.
Moreover, job security can be variable in construction. Projects can be short-term, affecting consistent pay. Welders who specialize in structural welding, including pipeline and heavy steel, typically see higher pay due to the technical nature of their work.
Automotive Industry Rates
The automotive industry is another significant arena for welders. This sector demands precision and adherence to strict safety standards. As a result, automotive welders often receive wages averaging $25 to $40 per hour. Those working in high-tech environments, such as automated welding processes, may be compensated at the higher end of this scale due to their technical skills and familiarity with advanced machinery.
Various roles exist within this industry, from assembly line positions to specialized welding for custom parts. Each offers varying pay rates depending on the required skill level and the companyβs market position. As automobiles become more complex and environmentally friendly, skilled welders will continuously be in demand, translating into ongoing wage growth and job opportunity.
"Welding is essential in many industries, each providing different pay scales and job challenges. Understanding these differences can lead to better career choices and workforce planning."
Benefits and Drawbacks of Welding Jobs
Understanding the benefits and drawbacks of welding jobs is essential for both potential welders and employers in the industry. It provides insights into what to expect in this field and the trade-offs that come with various job opportunities. This section focuses on significant elements that influence the perception and reality of welding as a career choice.
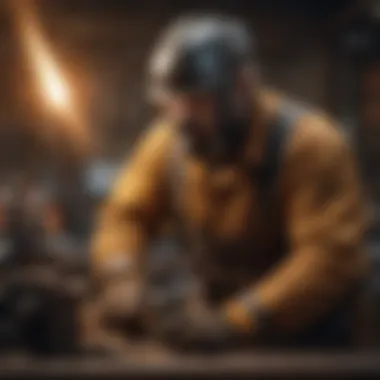
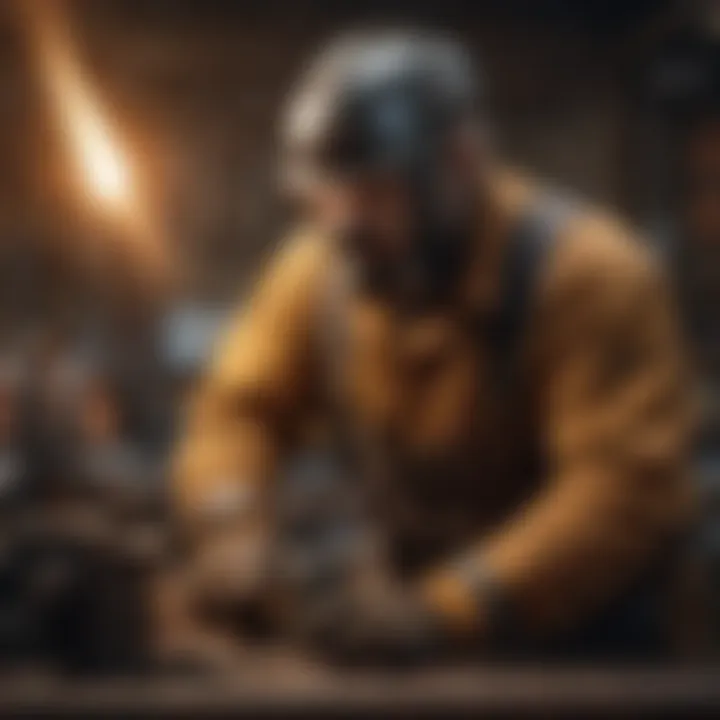
Job Security and Stability
Job security is often seen as a significant advantage of working in the welding industry. The demand for skilled welders remains fairly consistent, particularly in sectors like construction and manufacturing. Many projects necessitate welding for structural integrity, which creates ongoing opportunities for employment. Furthermore, as infrastructure ages and requires maintenance, the necessity for welders continues to grow. This translates into a career path that offers a solid sense of stability.
However, economic fluctuations can impact job security in the welding field. During economic downturns, projects may be put on hold, leading to layoffs or reduced hours for welders. This relies heavily on the overall health of the sectors employing welders. In regions where the demand for construction is high, job stability may be sustained. In contrast, rural areas often see more variability.
"While welding provides many opportunities, understanding local economic conditions is crucial to assess job security realistically."
Physical Demands and Risks
Welding is a physically demanding job. Welders must often work in awkward positions or at elevated heights. This can lead to physical strain over time. Moreover, the work environment can include exposure to fumes, heat, and other hazardous materials. Understanding these physical demands is crucial for anyone considering a career in welding.
Additionally, safety considerations play a vital role. Welders must wear protective gear and follow strict safety protocols to mitigate risks. Injuries can occur if safety measures are not followed properly. Thus, prospective welders should evaluate their ability to handle these physical and risk-related demands before entering the profession. Individuals with good physical fitness and a strong awareness of safety practices may adapt more easily to the demands of this job.
In summary, the welding occupation has its distinct benefits, notably job security in a growing field; however, it also demands a strong physical base and adherence to safety regulations. Assessing these factors thoroughly can aid individuals in making informed career choices.
Employer Considerations for Welder Compensation
In order to create a competitive and effective workforce, employers must account for various factors when determining welder compensation. Proper compensation is crucial, not just for satisfying their workforce, but also for ensuring long-term operational efficiency. This section will analyze the specific elements that influence compensation, such as cost-benefit analysis, the competitive landscape, and strategies for attracting and retaining skilled welders.
Cost-Benefit Analysis of Hiring Welders
When hiring welders, employers are compelled to conduct a thorough cost-benefit analysis. This ensures that the benefits of hiring skilled labor outweigh the costs associated with their employment. Factors to consider in this analysis include:
- Wages and Benefits: Attractive wage packages and benefits are necessary to draw in talented welders. Employers must ensure that their compensation packages are competitive within their local market.
- Productivity Levels: Skilled welders can significantly boost productivity in a work environment. Their expertise can lead to fewer mistakes and reduced rework.
- Training and Onboarding Costs: Employers must factor in the costs incurred during training new hires. If a welder needs to undergo extensive training, this may impact the overall profitability of their employment.
When evaluating welder compensation, employers should not only consider direct costs but also the return on investment resulting from skilled labor in the long run. The objective is to establish a balanced approach that promotes a motivated workforce while maintaining overall cost guidelines.
Attracting and Retaining Skilled Welders
To ensure operational success, attracting and retaining skilled welders is paramount. The industry is evolving, and welders with advanced skills and certifications have become increasingly valuable. Employers should consider the following strategies:
- Competitive Pay: Offering hourly rates that reflect the skills and certifications of welders aids in attracting top talent. Employers should regularly assess and adjust wages to match or surpass those of competitors.
- Career Development Opportunities: Providing welders with avenues for professional growth can enhance retention. This may include ongoing training, opportunities for skill advancement, and tuition reimbursement for further education.
- Work Environment: A safe, positive, and engaging work environment is a pivotal factor. Employers who invest in safety programs and workplace culture will find it easier to retain skilled workers.
- Flexible Schedules: Offering flexible working conditions or the possibility of remote work can attract welders who value work-life balance.
Future Trends in Welding Compensation
Welding compensation is entering a fresh phase marked by transformative trends. Technologies are shifting the framework of welding, which implies a need for welders to adapt. Understanding these future trends is essential for both welders and employers. The dynamic landscape illustrates how compensation rates can fluctuate based on emerging methodologies and sustainability practices. This trend will have implications not just for salaries but for the overall perception of welding as a profession.
Adapting to Technology and Automation
Technology is shaping welding in unprecedented ways. Automation is becoming a significant part of the process. This change brings several considerations for the workforce. First, the demand for high-tech skills is evident. Welders must now embrace continuous learning to keep pace with advancements such as robotic welding systems. Employers look for individuals who understand both traditional techniques and modern automated processes.
The integration of technology may influence hourly wages. While automation could reduce the number of welders needed, it may also increase the pay for those who possess unique technical skills. A welder today must therefore be versatile. Being skilled in troubleshooting and operating sophisticated machines can enhance job security. Moreover, companies implementing these technologies tend to offer better compensation packages. This creates a positive feedback loop: as the technology advances, it likely raises the value of skilled welders.
Sustainability and Green Welding Practices
Sustainability emerges as another essential trend in welding. As industries acknowledge the importance of eco-friendly practices, welding too must adapt. Sustainable welding practices are not merely ethical decisions; they influence the bottom line. Companies that prioritize green initiatives often attract clientele looking to reduce their environmental footprint.
The incorporation of sustainable methods can also lead to new job opportunities. Welders trained in green techniques may find their skills in high demand. Such practices can include using renewable energy sources and promoting energy-efficient processes. Hourly rates for welders skilled in these areas could be higher. They provide value beyond mere task completion; they contribute to a company's sustainability goals.
"Adapting to the demands of sustainability will not only enhance the labor market but also redefine the perception of welding as a future-ready profession."
In summary, the future of welding compensation hinges on technological adaptation and sustainability. Those entering the trade must not only develop their craft but also anticipate shifts in the landscape. Continuous education and an awareness of ecological impacts will play a critical role in shaping the economic viability of welding careers.
Ending
The conclusion of this article serves as a critical reflection on all the elements discussed regarding welder hourly rates. It synthesizes the information and highlights the significance of understanding compensation in the welding profession. Navigating through the complexities of wage structures is essential for both welder and employers.
For welders, grasping how different factors impact their hourly rates can lead to better decision-making regarding career paths. Knowledge of skills, certifications, and market demand directly shapes their earning potential. Recognizing market trends and geographical variations can help them negotiate better wages and secure more stable employment.
For employers, understanding these factors is equally vital. Making informed compensation decisions is crucial for attracting skilled welders in a competitive labor market. Moreover, ensuring fair pay helps in retaining talent, minimizing turnover, and enhancing job satisfaction among workers.
Overall, the discussion about welder hourly rates is not merely about numbers. It encapsulates financial implications, career growth, and the broader economic landscape of the welding industry.
"In the world of welding, knowledge is as powerful as the weld itself. Understanding the dynamics of compensation can lead to better prospects for everyone involved."
Grasping the insights of this article not only empowers welders but also offers employers a framework for structuring competitive compensation. As we move towards a future shaped by technology and market evolution, continuous learning about these factors will benefit all stakeholders. Thus, staying informed is key to thriving in the welding profession.