Understanding MSDS Training: Safety and Compliance
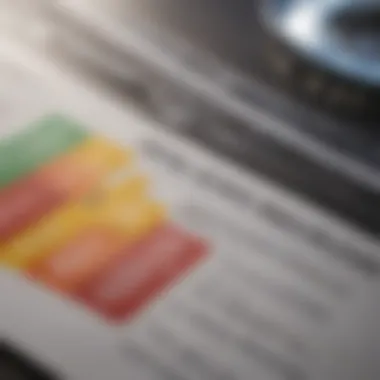
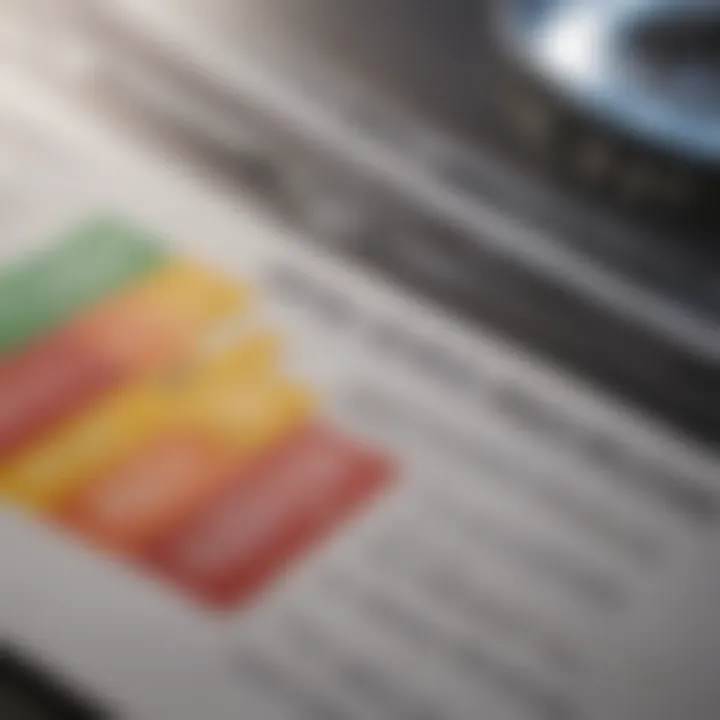
Intro
Material Safety Data Sheets (MSDS) are critical components in maintaining workplace safety and regulatory compliance, especially within environments handling hazardous materials. Understanding these sheets is paramount for employees as it equips them with the knowledge to respond effectively to potential risks. This article will explore the significance of MSDS training videos, examining their structure, effectiveness, and relevance in contemporary work settings.
Key Concepts and Terminology
Basic Definitions
An MSDS is a document that provides detailed information about hazardous substances. It includes data on chemical properties, health hazards, protective measures, and safety precautions. The MSDS serves as a guide to ensure the safety and health of individuals who may come into contact with hazardous materials.
Historical Context
The evolution of MSDS can be traced back to the emergence of chemical safety regulations in the late 20th century. Initially, these documents were mainly used in large industrial settings. However, as awareness about chemical hazards grew, regulatory frameworks, such as OSHA's Hazard Communication Standard, made the use of MSDS widespread across various sectors. This shift emphasized the need for continuous training regarding hazardous materials, paving the way for training videos.
Recent Innovations and Trends
Technological Advancements
With the rise of digital technology, MSDS training videos have transformed significantly. Today, they often utilize multimedia elements for enhanced engagement. These innovations include interactive modules, virtual reality simulations, and mobile accessibility, allowing employees to learn in diverse formats. Such advancements not only facilitate a better understanding but also promote compliance with updated safety regulations.
Sustainable Practices
An increasing focus on sustainability has led to the integration of eco-friendly materials in the MSDS process. Companies are now looking to produce training videos that emphasize the environmental impact of hazardous materials. This trend not only aligns with corporate responsibility but also reflects an overall commitment to safer and more sustainable workplace practices.
Practical Applications and Techniques
Step-by-step Guides
To effectively implement MSDS training videos, businesses can follow these steps:
- Identify key hazards relevant to the specific workplace.
- Select or create comprehensive MSDS training videos that cover these hazards.
- Schedule regular training sessions to engage employees.
- Assess employee understanding through quizzes or discussions.
- Update training materials regularly to incorporate new regulations or findings.
Case Studies
Numerous organizations have successfully utilized MSDS training videos. For instance, a large agricultural firm implemented a series of videos focusing on pesticide safety, leading to a 30% reduction in reported incidents. Another case involves a manufacturing company that revamped its training program, resulting in heightened safety compliance and overall employee satisfaction.
"Education and continuous training are only effective when presented in a manner that is engaging and accessible to all employees."
MSDS training videos offer vital insights and education. They not only assist in regulatory compliance but also cultivate a safety-conscious culture, essential for any organization.
Prelims to MSDS Training Videos
The selection of materials and methods to train employees about Material Safety Data Sheets (MSDS) is critical for workplace safety. MSDS training videos serve as a vital resource, providing a visual and auditory method to convey essential information. These videos simplify complex concepts, making it easier for employees to understand how to handle hazardous materials while adhering to safety regulations. In an age of digital information, using videos is not only a modern approach but also ensures effective learning in a shorter timeframe.
Definition of MSDS
Material Safety Data Sheets, often abbreviated as MSDS, are documents that summarize crucial information relating to the properties of hazardous materials. This includes the chemical composition, potential hazards, safe handling practices, and emergency response steps in case of accidents. An MSDS is required for each hazardous chemical present in an organization. These documents ensure that workers receive necessary information that can help them minimize risks associated with their jobs. Without access to accurate MSDS, employees can face significant exposure to harmful substances, leading to severe health problems or accidents.
Importance of MSDS Training
The importance of MSDS training cannot be overstated. First, adequate training ensures compliance with various regulatory requirements. Organizations must keep their employees informed about hazardous materials, which is not only a best practice but often a legal obligation under regulations set by the Occupational Safety and Health Administration (OSHA).
Moreover, effective MSDS training promotes a culture of safety within the organization. Employees knowledgeable about MSDS are better equipped to recognize hazards and take appropriate precautions. This proactive approach can lead to fewer workplace accidents and injuries. Consequently, investing in MSDS training videos does not merely fulfill compliance obligations; it fundamentally enhances employee awareness and safety consciousness.
Additionally, MSDS training videos can cater to diverse learning styles. Visual learners absorb information quickly through engaging content, while auditory learners benefit from narrated explanations. This versatility increases the likelihood that employees will retain critical safety information needed for their jobs. As a result, organizations can create safer work environments by ensuring that all employees understand the importance of adhering to safety guidelines related to hazardous materials.
Legal Framework Surrounding MSDS
The legal framework surrounding Material Safety Data Sheets (MSDS) is essential for ensuring workplace safety and regulatory compliance. Understanding this framework is crucial for organizations that handle hazardous materials, as it defines the responsibilities for documenting and communicating safety information. It helps to mitigate risks associated with hazardous substances and reinforces the need for proper training in recognizing and responding to these hazards.
Organizations must adhere to various regulations and standards regarding the formulation and use of MSDS. Compliance with these regulations not only fulfills legal obligations but also fosters a culture of safety among employees. The two primary components of this framework are OSHA regulations and Global Harmonization Standards, which establish guidelines for the creation and management of MSDS. Understanding these components will aid in ensuring that employees are adequately trained and informed about potential risks in the workplace.
OSHA Regulations
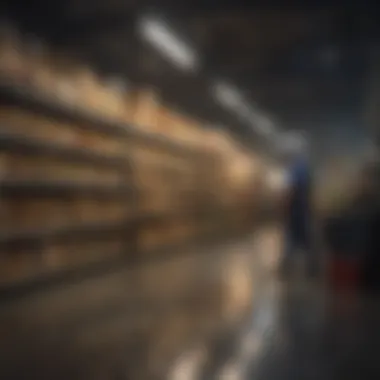
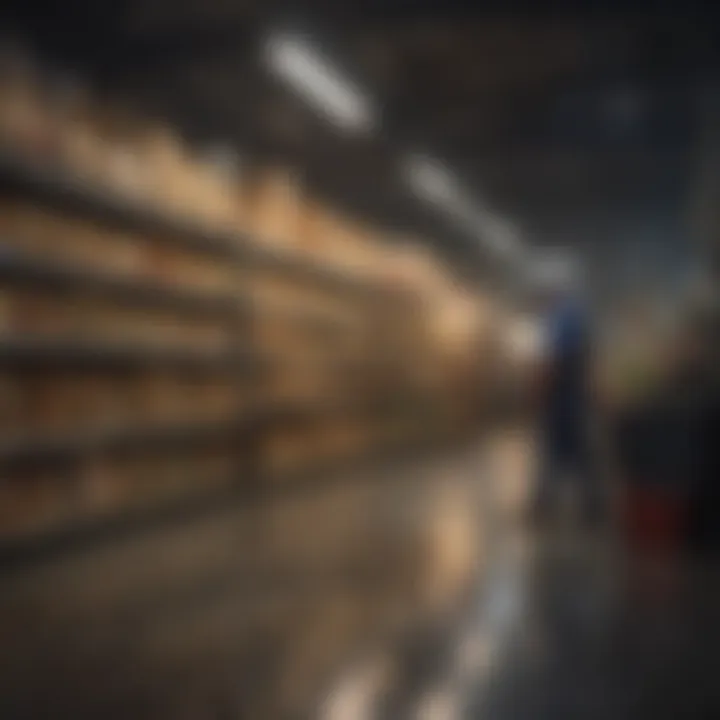
The Occupational Safety and Health Administration (OSHA) plays a vital role in regulating workplace safety through the Hazard Communication Standard (HCS). According to OSHA, every employer must ensure that hazardous chemicals are properly labeled, and that employees have access to MSDS. The goal is to communicate the hazards associated with chemical substances effectively. Employers are responsible for providing clear and understandable information about chemicals, including their risks and safe handling procedures.
Key requirements of OSHA regulations include:
- Labeling: Chemicals must have labels that provide essential information about their hazards.
- MSDS Accessibility: Employees must have easy access to MSDS for all hazardous materials they may encounter.
- Training Requirements: Employers are required to train employees on how to interpret MSDS and understand the hazards of substances they work with.
Failure to comply with OSHA regulations can lead to severe consequences, including fines and penalties. Thus, organizations must prioritize MSDS training to meet these regulations and ensure a safe working environment.
Global Harmonization Standards
In conjunction with OSHA regulations, Global Harmonization Standards offer a framework for creating consistent safety data sheets worldwide. The Globally Harmonized System of Classification and Labelling of Chemicals (GHS) aims to unify the varying safety standards and regulations across different countries. This system enhances the understanding of the hazards associated with chemicals globally, which is crucial for organizations involved in international trade.
Implementing GHS means that MSDS will adopt standardized formats for classification and labeling of chemicals. The benefits of these standards include:
- Consistency: A standardized approach ensures that information on chemical hazards is easily understood across different regions.
- Improved Communication: The unified system allows for better communication of risks associated with hazardous substances.
- Enhanced Regulatory Compliance: Organizations that adhere to GHS improve their compliance with local and international regulations.
By integrating Global Harmonization Standards into their MSDS training, organizations contribute to a safer workplace while ensuring compliance with global safety regulations. Understanding both OSHA regulations and these global standards is fundamental for organizations in fostering an environment where safety is prioritized and compliance with the law is maintained.
Components of an Effective MSDS Training Video
An effective MSDS training video must encompass several critical components to ensure it meets its educational purposes and compliance requirements. These elements determine how well the video communicates essential safety information, engages the viewer, and facilitates knowledge retention. Understanding these components can significantly enhance the overall effectiveness of MSDS training, particularly in complex environments like agriculture where safety is paramount.
Content Coverage
The content coverage of an MSDS training video must be comprehensive. It should encapsulate key topics such as the structure of Material Safety Data Sheets, identification of hazards, handling procedures for dangerous materials, and emergency response strategies. Each relevant section of the MSDS should be clearly explained to provide a thorough understanding. Including real-life examples that are relevant to the agricultural setting enhances relatability.
Furthermore, the information presented should align with regulatory standards, ensuring that employees understand their obligations under laws such as OSHA. Incorporating case studies or testimonials can also illustrate the consequences of not adhering to MSDS guidelines, making the training more impactful.
Visual and Audio Elements
Visual and audio elements play a crucial role in how effectively information is conveyed. An engaging video should utilize high-quality visuals, including clear graphics, animations, and text overlays. These features can help to break down information into digestible parts. Color coding can be applied to hazardous materials, aiding in quick recognition of risks associated with each substance.
Audio is equally important. The narration should be clear, professional, and appropriately paced to match the visual components. Background music, if used, must not interfere with the clarity of the information; rather, it should enhance engagement without being distracting. Subtitles can also benefit non-native English speakers or those with hearing difficulties, increasing accessibility.
Duration and Pacing
The duration and pacing of the video are vital considerations for maintaining viewer focus and ensuring information retention. A training video should ideally last no longer than 20 to 30 minutes. This timeframe is generally accepted for adult learning, keeping fatigue at bay and maximizing attention.
Pacing should allow enough time for viewers to absorb information. Quick, concise segments can keep momentum high, but be cautious not to rush through critical content. Segmenting the training into modules allows for pauses where employees can engage in discussions, ask questions, or review key points. By striking a balance in duration and pacing, an MSDS training video can create a more effective educational experience.
In summary, the componentsโcontent coverage, visual and audio elements, and duration and pacingโare integral to creating effective MSDS training videos. Organizations should prioritize these factors for optimal learning outcomes.
Delivery Methods for MSDS Training Videos
Selecting the right delivery method for MSDS training videos is crucial for effective learning and compliance. The chosen method affects not just the engagement level of trainees but also the retention of important safety information. Organizations must consider various aspects such as accessibility, convenience, and the nature of their workforce when deciding on the delivery platforms for their training materials.
Online Platforms
Online platforms offer significant benefits for delivering MSDS training videos. They provide flexibility, allowing employees to access training materials at their convenience. This is particularly beneficial for organizations with diverse schedules and locations.
Some key advantages include:
- Accessibility: Employees can watch training videos anytime and anywhere without needing to be physically present at a training room. This is especially useful for remote teams or shift workers.
- Cost-Effectiveness: Online training eliminates the need for printed materials and potentially high travel costs for in-person training sessions.
- Scalability: Organizations can easily update content and rescale training sessions to accommodate new employees or updated regulations.
- Interactive Features: Many platforms enable interactive elements like quizzes or discussion boards, enhancing understanding and engagement.
However, there can be challenges with online training, such as technological issues or varying levels of digital literacy among employees. It is essential to ensure that all staff are comfortable with the technology used for training.
On-Site Training
On-site training involves conducting training sessions at the workplace. This approach can be beneficial for fostering a direct and personal learning environment. Employees can engage face-to-face with trainers, ask questions in real time, and participate in hands-on activities that reinforce learning.
Some reasons why on-site training may be preferred include:
- Direct Interaction: Trainees can immediately clarify doubts and seek expertise from the trainer, creating a direct line of communication.
- Customization: Training can be tailored to specific workplace environments, making it more relevant to employeesโ daily tasks.
- Monitoring Progress: Supervisors can observe employee engagement and assess immediate comprehension through discussions and practical applications.
Potential drawbacks of on-site training include logistical considerations, such as scheduling, space availability, and equipment needs. It might also entail higher costs if external trainers are involved.

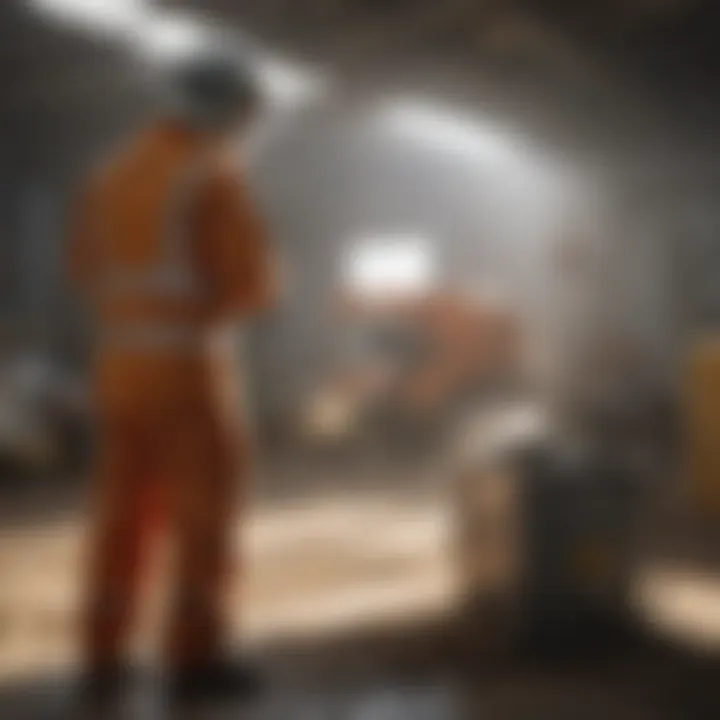
"Effective MSDS training is not just about compliance; it is about creating a culture of safety that permeates every level of the organization."
Measuring the Effectiveness of Training
Measuring the effectiveness of MSDS training is crucial to ensure that employees understand safety protocols and compliance requirements. It provides an objective way to assess whether the training meets its intended goals. An effective evaluation can highlight areas that need improvement, ensuring that the training evolves in response to the changing needs of the workplace.
Feedback mechanisms and assessments play a significant role in this process. They not only gather data but also promote a continuous learning environment, which is essential for fostering a culture of safety.
Feedback Mechanisms
Feedback is a vital element in understanding the impact of training. It allows for a two-way communication process, enabling trainers to gauge employee understanding and retention. There are several methods to collect feedback:
- Surveys and Questionnaires: Post-training surveys can measure employee satisfaction and perceived value of the training content. These tools can reveal whether participants found the training informative and engaging.
- Focus Groups: Engaging small groups of employees in discussions can provide deeper insights into the training's effectiveness. Participants can share their experiences, highlight gaps, and suggest improvements.
- Follow-Up Interviews: Direct conversations can yield qualitative data about the training. Employees may express their understanding of MSDS content and how they apply it to their daily tasks.
Effective feedback mechanisms lead to actionable insights, enabling organizations to refine their training approach over time. Organizations can adapt their strategies based on real-world insights, resulting in continuously improving training programs.
Assessments and Evaluations
Assessments and evaluations are structured methods to measure knowledge acquisition and skill application. They are essential for establishing whether training objectives were met. There are various evaluation strategies:
- Quizzes and Tests: These can assess knowledge retention immediately after training. Regular quizzes can be integrated into ongoing training to ensure that employees regularly engage with the material.
- Practical Assessments: Demonstrating knowledge through hands-on evaluations provides a real-world measure of an employee's capability. For instance, employees might be asked to interpret an MSDS document and apply it in a simulated scenario.
- Performance Metrics: Monitoring employee performance post-training can show if safety procedures are being followed. For example, a decrease in incidents or near-misses can indicate effective training.
- Longitudinal Studies: Conducting evaluations over time can illustrate the training's long-term effectiveness. Tracking compliance rates and safety incidents can show the lasting impact of MSDS training.
Implementing varied assessment methods offers a comprehensive view of training effectiveness, benefiting both the organization and its employees.
Challenges in Implementing MSDS Training
Implementing MSDS training presents various challenges. Recognizing these difficulties is essential for developing effective training programs. Ultimately, understanding these challenges can help organizations build a robust safety culture. Addressing employee resistance and technical issues is often central to the training's success.
Employee Resistance
Employee resistance is a significant barrier to effective MSDS training. Workers may feel overwhelmed by additional training requirements or perceive them as unnecessary. This mindset can stem from a lack of understanding regarding the relevance of safety data sheets to their daily tasks. Engaging employees through relevant scenarios can enhance their perception of training importance.
When employees grasp how hazardous materials affect their work and well-being, compliance improves. Active involvement in the training process boosts buy-in and reduces resistance.
To combat this resistance, organizations can:
- Offer clear explanations about the significance of MSDS training.
- Incorporate real-life examples to illustrate safety implications.
- Encourage feedback and adapt training based on employee suggestions.
- Develop a supportive atmosphere focused on learning and safety.
Training programs that consider and mitigate employee apprehensions foster a more compliant and safety-oriented workplace.
Technical Issues
Technical issues present another challenge when implementing MSDS training programs. Issues such as inadequate equipment, software failures, or internet connectivity problems can disrupt the training process. Such interruptions can lead to frustration for trainers and participants alike.
Organizations must ensure proper infrastructure to minimize these setbacks. This involves:
- Regularly updating training equipment and software.
- Conducting pre-training tests on technology to identify potential problems.
- Offering technical support during the training sessions.
- Training facilitators to manage any potential technical difficulties in real-time.
To conclude, addressing both employee resistance and technical issues are critical elements for successful MSDS training implementation. Overcoming these challenges not only improves training effectiveness but also enhances workplace safety compliance.
"Effective training reduces workplace accidents and ensures regulatory compliance."
By actively working to mitigate these difficulties, organizations can better educate their workforce and foster a proactive approach to safety.
The Role of Technology in MSDS Training
Technology significantly enhances the effectiveness of MSDS training. Proper utilization of technological tools allows organizations to create more engaging and informative training experiences for employees. By implementing effective selection of platforms and production methods, companies can ensure that safety knowledge is not just delivered but retained.
Advancements in Video Production
The field of video production has evolved considerably. Professional-grade video technology is now more accessible than ever, enabling companies to produce high-quality MSDS training videos. Improved resolution, sound quality, and editing software facilitate clearer conveyance of complex information. For instance, the use of animations can simplify difficult concepts in safety data sheets, making them more understandable. Moreover, interactive elementsโsuch as quizzes embedded within videosโfurther reinforce learning outcomes and encourage active participation.
- Enhanced Visual Quality: Modern cameras and editing software allow for higher-quality visuals and clear audio, which is crucial in effectively communicating important safety information.
- User Engagement: Incorporating interactive elements engages employees, making learning less monotonous.
- Cost-Effectiveness: Technological advancements further lower production costs in the long run, enabling frequent updates and revisions to reflect regulatory changes or new safety practices.
Integration with Learning Management Systems
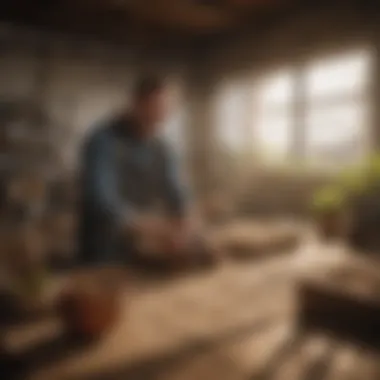
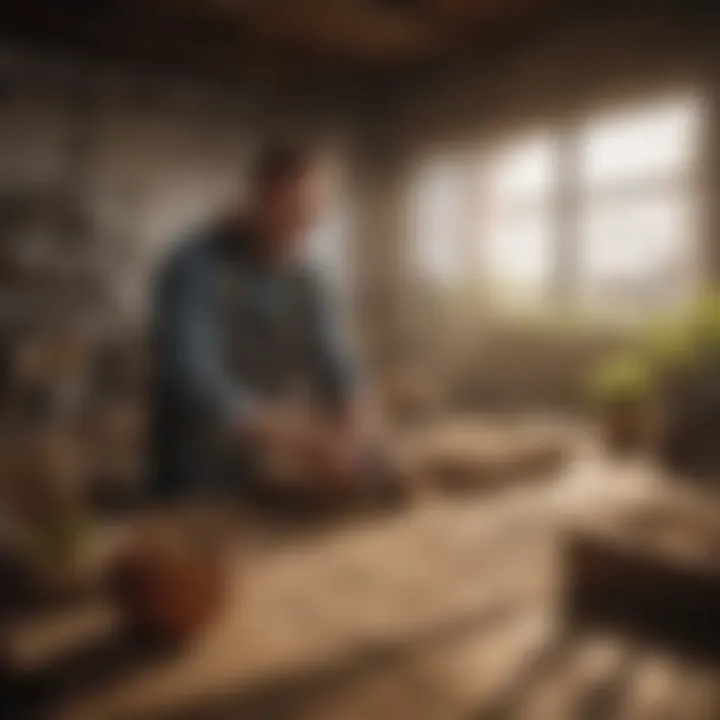
The integration of MSDS training videos with Learning Management Systems (LMS) is vital for tracking progress and effectiveness. LMS platforms allow organizations to manage training schedules, assess employee understanding, and streamline the delivery of content. This integration facilitates:
- Centralized Access: Employees can access all training content in one location, making it easier to complete required training modules.
- Performance Tracking: Organizations can monitor employee completion rates, assessment scores, and overall engagement with the content. This allows for timely interventions if knowledge gaps surface.
- Customizable Training Pathways: LMS can tailor the training experience based on individual employee needs and prior knowledge, optimizing the learning experience.
The combination of advanced video production and robust LMS integration not only improves compliance with safety training but also nurtures a culture of safety within workplaces.
"The integration of modern technology in MSDS training embodies a commitment to employee safety and operational excellence."
As workplaces become increasingly digitized, it remains essential for organizations to leverage technology effectively. Doing so will ensure the continued relevance and efficacy of MSDS training.
Case Studies of Successful MSDS Training
Case studies play an essential role in understanding the practical application of MSDS training videos. They provide concrete examples of how specific industries have effectively implemented training methods. This section highlights significant instances where organizations have reaped the benefits of robust MSDS training. These case studies not only illustrate best practices but also serve as a guide for others aiming to enhance their safety protocols and compliance measures.
Industry-Specific Examples
In agriculture, the handling of hazardous materials is commonplace, making effective MSDS training vital. For instance, a large agribusiness in the Midwest adopted an MSDS training video focused on pesticide safety. The video was tailored to the specific chemicals that employees would encounter. By incorporating real scenarios and testimonials from personnel, the training resonated more with the viewers. After implementing this program, the company reported a 40 percent reduction in incidents related to pesticide exposure.
In another sector, a manufacturing plant revamped its MSDS training strategy by introducing engaging multimedia elements. The training included a mix of videos, interactive quizzes, and on-the-spot demonstrations of safety practices. This approach led to an impressive improvement in employee retention rates of key safety protocols. Employees were able to demonstrate their knowledge in practical settings, reinforcing the learning process.
Data-Driven Outcomes
The outcomes of these case studies can often be quantified, providing a clear picture of the impact of MSDS training videos. Statistics from the agribusiness example indicated a sharp decline in unsafe behaviors post-training. More significantly, compliance audits reflected an improved understanding of safety data sheets among the staff. These audits showed a 25 percent increase in proper MSDS usage during evaluations.
Moreover, the manufacturing plant's improved retention rates translated into fewer workplace accidents. A follow-up analysis documented a decrease in reported incidents by 30 percent within six months of adopting the new training strategy. Such data illustrates that effective MSDS training can substantially enhance workplace safety and regulatory compliance.
Future Trends in MSDS Training Video Production
The landscape of MSDS training video production is consistently evolving. Staying informed about emerging trends is crucial for organizations aiming to enhance safety and compliance in the workplace. This section explores significant developments in technology and regulation that shape the future of MSDS training videos.
Emerging Technologies
Recent advancements in technology are redefining the way MSDS training videos are produced and delivered. Virtual reality (VR) and augmented reality (AR) offer immersive experiences that engage learners more effectively than traditional methods. These technologies allow employees to experience simulated hazardous situations, making the training more tangible and memorable.
Additionally, artificial intelligence (AI) can personalize learning experiences by adapting the content to the individual's knowledge level and learning pace. The use of interactive elements, such as quizzes and simulations, can keep the viewers involved and improve retention rates. Organizations should also consider mobile-friendly formats that allow employees to access training on-the-go, thereby increasing flexibility.
The introduction of cloud-based solutions facilitates easier sharing and access of training materials across different locations. This ensures consistency in training irrespective of geographical barriers.
"Embracing these technologies not only enhances engagement but also maximizes the training effectiveness."
Shifts in Regulatory Standards
The regulatory landscape surrounding MSDS training is also experiencing changes. As industries advance, so do the standards regarding safety training and hazard communication. New regulatory requirements may mandate more frequent and updated training sessions, making it essential for companies to keep their MSDS training videos current and compliant.
Increased global harmonization of regulations, such as the GHS (Globally Harmonized System), necessitates organizations to adapt their training materials to meet diverse international standards. This means MSDS training videos must not only inform about local regulations but also educate employees on global compliance aspects.
Furthermore, specific industries, such as agriculture, are subject to unique safety requirements. MSDS videos will need to incorporate these unique regulatory demands to ensure that training meets the required standards effectively.
Keeping abreast of these changes allows organizations to proactively adapt their training programs, reducing risks and ensuring a safer workplace.
The End and Recommendations
The conclusion section of this article serves as a pivotal point. It encapsulates the key insights gained throughout the discussion of MSDS training videos and highlights their crucial role in promoting safety and compliance in various workplaces. MSDS training is not just about fulfilling regulatory obligations; it is about instituting a safety culture that prioritizes the well-being of employees, especially in high-risk industries like agriculture.
Implementing effective MSDS training can aid organizations in minimizing accidents and incidents related to hazardous materials. Moreover, it fosters an informed workforce who understands the potential risks associated with the substances they handle. By adhering to the best practices in training video production and delivery, organizations can ensure that their employees remain compliant with evolving regulations and are equipped with essential knowledge to make sound decisions in emergency situations.
Best Practices Summary
Organizations should consider the following best practices for creating and implementing MSDS training videos:
- Content Quality: Ensure that the videos are comprehensive and cover all necessary aspects of safety data sheets, including proper handling instructions and emergency procedures.
- Engaging Format: Use a mix of visual aids, real-life scenarios, and expert insights to engage employees effectively.
- Regular Updates: Keep the content fresh and aligned with current regulations and newly adopted technologies in safety protocols. Regular reviews and updates will maintain the relevance of the training.
- Interactive Components: Incorporate quizzes or prompts that encourage active participation from the viewers. This can increase retention of information and make the learning experience more effective.
Call to Action for Organizations
Organizations must take immediate action to incorporate MSDS training videos into their safety protocols. This includes:
- Assessing Current Training: Review existing training materials to identify gaps regarding MSDS information.
- Investing in Quality Production: Allocate resources towards high-quality video production to ensure the content meets educational standards and engages employees.
- Tailoring Training to Needs: Consider the specific contexts and challenges of different departments or roles within the organization. Customized videos can enhance relatability and effectiveness.
- Evaluating Training Impact: After implementation, use feedback and assessment results to evaluate the effectiveness of the training. Adjust content and delivery based on this data to improve future sessions.
โThe strength of the team is each individual member. The strength of each member is the team.โ โ Phil Jackson
This perspective should resonate in organizations as they prioritize safety through thorough and effective training.