Understanding Large Chicken Incubators: A Guide
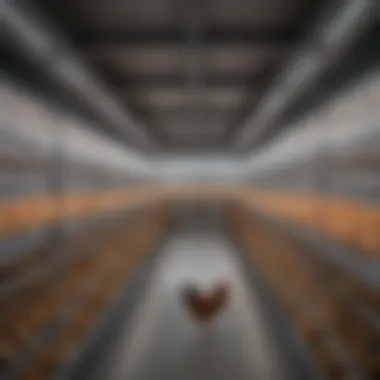
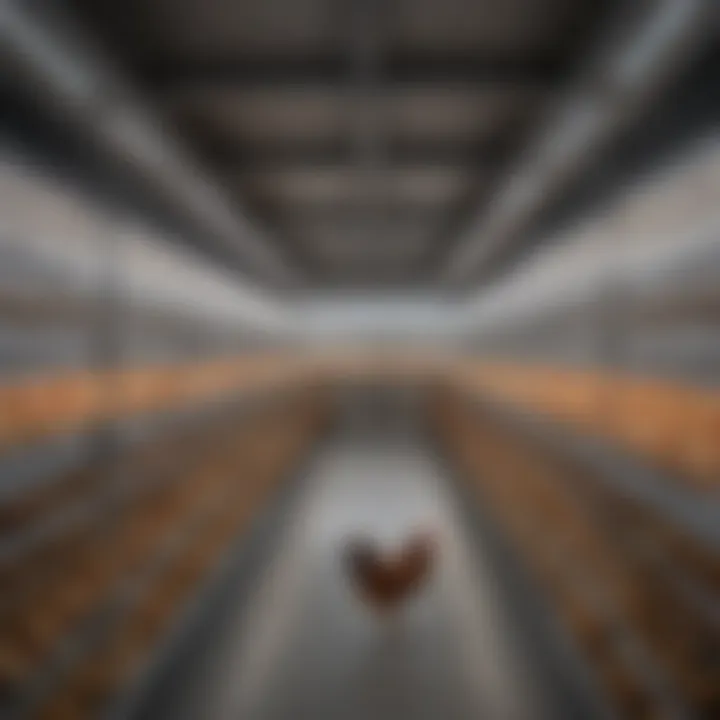
Intro
The pursuit of optimal poultry farming practices often leads to a crucial component: large chicken incubators. These sophisticated machines play an essential role in the incubation process, providing controlled environments for hatching eggs. Understanding their design and functionality is vital for agriculture enthusiasts and professionals alike. This article seeks to elucidate key concepts related to large chicken incubators, explore recent trends, and offer practical applications for effective operation.
Key Concepts and Terminology
Basic Definitions
When embarking on a journey in poultry farming, it is foremost to comprehend fundamental terminology. A chicken incubator is a device engineered to create an environment conducive to egg hatching. Efficient incubators regulate temperature, humidity, and ventilation, which are crucial for embryo development. The capacity of an incubator can vary significantly, but large incubators typically accommodate hundreds to thousands of eggs, catering to commercial farming needs.
Historical Context
The history of incubation dates back centuries, with primitive methods such as using straw and heat from rotting organic materials. Over time, the evolution of incubation has witnessed remarkable changes. The invention of mechanical incubators in the early 19th century marked a turning point, allowing for better monitoring of environmental conditions. Presently, large chicken incubators are equipped with advanced features like automatic turning mechanisms and digital controls, ensuring precision and efficiency.
Recent Innovations and Trends
Technological Advancements
The integration of technology in large chicken incubators cannot be overstated. Modern models often employ smart sensors and IoT capabilities, enabling real-time monitoring and control via mobile devices. This innovation streamlines the process, allowing farmers to manage hatching conditions remotely. Furthermore, some incubators are designed with energy-efficient systems that not only reduce costs but also lessen environmental impact.
Sustainable Practices
As the agriculture sector shifts towards sustainability, large chicken incubators have also adapted. Many manufacturers incorporate eco-friendly materials and energy sources in their designs. This trend aligns with broader agricultural shifts toward minimizing carbon footprints. Additionally, incorporating renewable energy sources such as solar panels in incubator setups can further enhance sustainability efforts.
Practical Applications and Techniques
Step-by-step Guides
Optimizing the use of large chicken incubators involves following precise steps:
- Preparation: Ensure the incubator is clean and well-sterilized before use. Maintain all equipment in optimal working condition.
- Setting Conditions: Adjust the temperature and humidity settings according to the specific breed and egg type. Most chicken eggs require a temperature of 99.5Β°F (37.5Β°C) and humidity of 50% during incubation.
- Egg Placement: Position eggs properly in the incubator, ensuring they are not overcrowded. Rolling or turning them regularly helps maintain health.
- Monitoring: Regularly check temperature and humidity levels. Adjust as necessary, utilizing automated systems where applicable.
- Hatching Phase: In the last few days of incubation, increase humidity to around 65% to assist hatching.
Case Studies
A notable example of effective use of large chicken incubators is seen in commercial poultry farms in the United States. By deploying automated systems and data analytics, these farms significantly increased their hatching rates while decreasing losses. Such practices underscore the potential benefits of advanced incubation techniques.
"Utilizing large chicken incubators effectively can dramatically enhance productivity and ensure healthy poultry growth."
Understanding and mastering the functionality and intricacies of large chicken incubators is paramount for todayβs poultry farmers. These insights provide a pathway toward maximizing incubation success and fostering sustainable agriculture practices.
Preamble to Large Chicken Incubators
Large chicken incubators play a critical role in modern poultry farming. They allow farmers and enthusiasts to efficiently hatch eggs on a significant scale, ensuring higher productivity in their operations. Understanding these machines is essential for optimizing the incubation process, which directly affects the health and viability of chicks.
With advancements in technology, large incubators have become more sophisticated. They provide precise control over essential factors such as temperature, humidity, and ventilation. These capabilities ensure that eggs develop properly, improving hatch rates significantly compared to manual methods.
Definition and Purpose
A large chicken incubator is defined as a device that creates and maintains the ideal conditions for egg incubation. This involves regulating temperature, humidity, and airflow. The primary purpose of these incubators is to mimic the natural environment that chicken eggs need to hatch successfully.
In commercial poultry farming, the use of large incubators is crucial for several reasons. They save time and labor compared to traditional methods. Moreover, they allow farmers to hatch numerous eggs simultaneously, making farming operations more efficient. Large incubators can handle hundreds or even thousands of eggs at a time, depending on the model.
Historical Context of Incubation
The concept of incubation is not new; it has historical roots that date back centuries. Historically, incubation was conducted using broody hens, which would sit on eggs to provide warmth. This natural method, while effective, limited the number of eggs that could be hatched at one time.
The shift from natural to artificial incubation began in the late 19th century with the invention of the first mechanical incubators. These early machines were simple boxes with heat sources, but they marked a significant leap forward. Over the years, technological advancements have led to the development of complex systems that can provide consistent conditions needed for successful hatching.
As a result, the efficiency of poultry farming has improved dramatically. Farmers can now manage larger operations with precise controls, allowing for better outcomes in terms of hatch rates and overall production.
"Understanding the evolution of incubation methods helps appreciate current technologies and the impact they have on poultry farming."
Overall, the development of large chicken incubators has changed the landscape of poultry farming. Their significance cannot be overstated; they are at the heart of modern agriculture, helping ensure food security and the sustainability of farming practices.
Types of Large Chicken Incubators
Understanding the types of large chicken incubators is essential for anyone involved in poultry farming. Each type of incubator has its own features, advantages, and challenges. Recognizing these differences helps in choosing the right incubator based on specific needs.
Forced Air Incubators
Forced air incubators employ a fan system to circulate heated air uniformly throughout the incubator. This feature ensures a more consistent temperature, which can lead to higher hatch rates. The forced air system minimizes temperature gradients within the incubator, allowing eggs to develop more evenly.
Benefits of Forced Air Incubators:
- Uniform Temperature: The air circulation helps maintain a stable environment.
- Higher Hatch Rates: Consistent conditions support better embryo development.
- Flexibility in Use: Suitable for various egg sizes and types, including chicken, duck, and quail eggs.
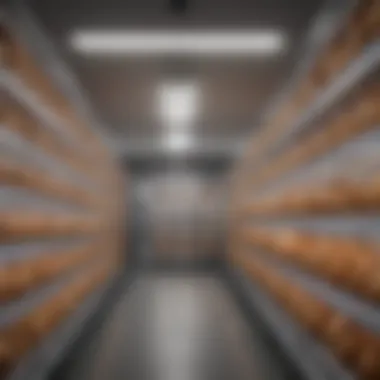
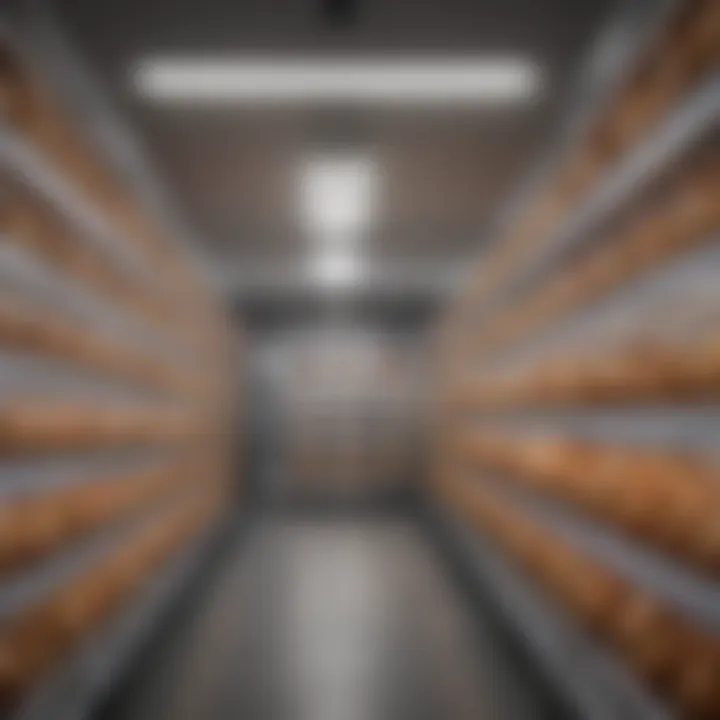
However, they do have some considerations. The initial cost may be higher compared to still air incubators. Additionally, it is important to ensure the fan is functioning properly to avoid any detrimental effects on incubation.
Still Air Incubators
Still air incubators rely on natural convection for air movement without the use of fans. Heat rises, creating a flow of warm air. This type is simpler in design and often less expensive than forced air options.
Advantages of Still Air Incubators:
- Cost-Effective: Lower initial investment compared to forced air models.
- Simplicity: Fewer moving parts means less maintenance is necessary.
On the downside, there are challenges. Still air incubators often have temperature fluctuations, especially if the surrounding environment changes. Hatch rates may also be lower due to uneven heating.
Automated Egg Turners
Automated egg turners are devices that rotate eggs at regular intervals to mimic the natural process done by hens. Proper turning is crucial as it prevents the embryos from sticking to the shell and promotes even development.
Key Features of Automated Egg Turners:
- Consistency: Ensures eggs are turned regularly without manual effort.
- Enhanced Hatch Rates: Improved conditions can lead to better overall hatch success.
- Convenience: Frees up time for farmers, allowing them to focus on other tasks in poultry management.
Although automated turners are beneficial, they require electrical power to function. This is an important consideration if planning to use them in areas with unstable electricity supply.
In summary, the choice of incubator type impacts the entire incubation process. By understanding the different types available, farmers can make informed decisions that align with their operational goals.
Key Components of a Large Chicken Incubator
Understanding the key components of a large chicken incubator is essential for anyone involved in poultry farming. Each component plays a crucial role in creating the optimal environment for successful egg incubation. Failing to maintain any of these elements can lead to high failure rates in hatching. Thus, recognizing their importance allows farmers to achieve higher productivity and better outcomes.
Heating Mechanisms
Heating mechanisms are pivotal in a chicken incubator. They ensure that the eggs receive the necessary warmth for developing embryos. The most common heating sources are electric heaters and gas-fired systems. Each has its advantages and considerations.
Electric heaters provide consistent and controllable heat, which is easier to manage. On the other hand, gas systems can be more economical in areas with high electricity costs.
Regardless of the type, it's crucial to ensure the heating system distributes warmth evenly. Hot spots can be detrimental, causing uneven development of embryos. Regular checks of the heating elements must be performed. A malfunction can easily derail the incubation process.
Humidity Control Systems
Humidity control is another decisive factor in egg hatching. The right humidity level ensures that embryos do not lose too much moisture. Too low humidity can cause the eggs to dry out, while too high humidity may lead to bacterial issues or suffocation of the embryos.
Most large chicken incubators include built-in humidity control systems such as water pans, misters, or fully automatic humidity systems that rely on sensors. The ideal humidity is generally around 40% during the first 18 days and then raised to 60% or higher during the final stages of incubation.
Farmers must monitor humidity closely, adjusting as needed based on the incubatorβs specifications and environmental conditions.
Ventilation Systems
Ventilation systems are essential to maintaining air quality and oxygen levels within the incubator. Developing embryos require oxygen and produce carbon dioxide. A deficiency in air circulation can lead to poor hatch rates.
Most large chicken incubators come equipped with fans that facilitate airflow. Proper ventilation helps prevent the buildup of harmful gases. It also supports even temperature distribution inside the incubator.
Regular maintenance of these systems is crucial. Dust and debris can obstruct airflow, which directly impacts the health of the incubating eggs. Keeping the vents clean is a simple yet effective measure to ensure success.
Temperature Regulation
Temperature regulation is likely the most critical factor in the incubation process. The optimal temperature for chicken eggs is around 99.5Β°F (37.5Β°C). Slight variations can affect embryo development significantly.
A stable temperature control mechanism is necessary to prevent fluctuations caused by external influences. Many large chicken incubators are equipped with sophisticated thermostats that provide ongoing temperature readings and adjustments.
It is advisable to place additional thermometers or temperature sensors inside the incubator. This strategy helps cross-verify the readings and ensures accurate monitoring. Regular calibration of these devices can prevent temperature-related issues.
By understanding these key components, poultry farmers can optimize their incubation processes, leading to increased hatching success and healthier chicks.
Operational Considerations
In the realm of large chicken incubation, operational considerations are critical to maximizing efficiency and hatch rates. Each phase of operation requires attention to detail, as small miscalculations can lead to significant consequences. Understanding how to properly manage the factors within an incubator can ultimately determine the success of the entire process.
Setting Up the Incubator
Setting up a large chicken incubator properly is foundational to achieving optimal results. This stage involves several steps that require careful planning. Initially, locate the incubator in a space with stable temperature and low contamination risk. Make sure that the area is free from drafts, which could disrupt the internal temperature. The placement should allow easy access for monitoring and adjustment.
Next, ensure the incubator is clean and sanitized before the first use. Following this, configure the incubatorβs settings according to the specific needs of the hatching eggs. This includes adjusting temperature and humidity levels based on the type of eggs being incubated. Different breeds may have unique requirements, thus, it's important to research beforehand to align settings precisely. Remember to wait for the incubator to achieve stabilization before introducing the eggs.
Egg Selection and Preparation
Egg selection is a pivotal step that directly impacts hatch outcomes. The quality of eggs chosen for incubation can determine viability rates. Look for eggs that are free from cracks, have clean shells, and are of uniform size and shape. Freshness also plays a role; eggs should ideally not be more than a week old at the time of incubation.
Preparation of the eggs themselves is equally important. Clean any dirt from the eggs using a damp cloth. Avoid using strong chemicals or soaps, as these can harm the eggs' protective coating. Additionally, consider marking the eggs with a pencil, indicating the laying date and other important details. This practice can help monitor the incubation timeline effectively and ensure proper tracking.
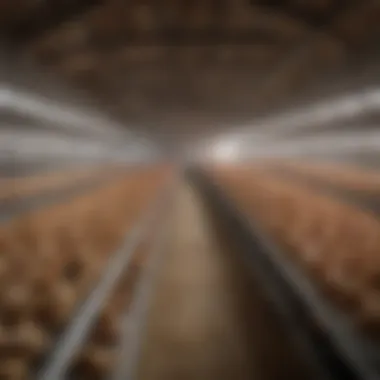

Monitoring and Adjustments
Monitoring and adjustments throughout the incubation process are vital for success. Regular checks on temperature and humidity levels should be conducted multiple times each day. Any deviations from the established parameters could jeopardize the eggsβ viability. If fluctuations occur, adjustments must be made promptly to avoid long-term effects.
Furthermore, keep an eye on ventilation. Adequate air exchange is crucial, especially during the later stages of incubation when embryos are more active. Look out for signs of developmental issues which may appear in the early days, such as abnormal egg movement or condensation inside the incubator.
"The monitoring phase is where the difference between casual hobby incubation and professional breeding can be clearly seen."β An experienced poultry farmer
In summary, operational considerations are integral to the incubation process. Proper setup, careful egg selection, and constant monitoring equip poultry enthusiasts and professionals with the means to enhance hatch rates. While the intricacies of these operations may seem daunting, they are essential for achieving reliable and productive outcomes.
Benefits of Large Chicken Incubators
The role of large chicken incubators in modern poultry farming cannot be overstated. As the demand for poultry products increases, so does the need for efficient incubation systems. The benefits offered by these systems are crucial in addressing several challenges faced by farmers. Below are key advantages that highlight their significance in optimizing hatchery operations.
Increased Hatch Rates
One of the primary advantages of large chicken incubators is the increase in hatch rates. These incubators are designed to create an optimal environment for embryonic development. Unlike smaller models, they offer better control over temperature, humidity, and airflow.
The sophisticated heating mechanisms and humidity control systems enable consistent conditions that are essential for hatching. Studies show that maintained conditions can improve hatchability by up to 90% or more, tremendously impacting the productivity of poultry farms. This reliability helps farmers maximize their output, ensuring that more of the eggs hatch successfully.
Key Factors Contributing to Increased Hatch Rates:
- Consistent Temperature Control
- Automated Humidity Regulation
- Regular Monitoring of Environmental Conditions
Efficient Space Utilization
Large chicken incubators also promote efficient space utilization. These models can house a greater number of eggs compared to traditional methods. With the right design, they provide more capacity while minimizing the footprint required in a hatchery.
Furthermore, many large incubators come with vertical stacking options, optimizing available floor space. This feature helps in maximizing production without needing to increase the physical area of the farm.
Benefits of Optimal Space Usage:
- Higher Egg Production Capacity
- Reduced Operational Costs
- Better Organization and Management
Labor Savings
Incorporating large chicken incubators into the farming process can lead to significant labor savings. These systems typically feature automated controls that reduce the amount of hands-on work required. With mechanisms for automatic egg turning and environmental adjustments, farmers can tend to their hatchery with less frequent manual intervention.
This efficiency allows labor to be allocated elsewhere or reduced, leading to a more streamlined operation. Consequently, farmers can focus on other vital aspects of their business, such as feeding, health monitoring, or expansion.
Labor Savings include:
- Reduced Need for Manual Monitoring
- Streamlined Operational Processes
- Ability to Attend to Other Farm Duties
"By integrating large chicken incubators, farmers can not only improve hatch rates but also utilize their space and labor more effectively."
In summary, the advantages of large chicken incubators are numerous. From increasing hatch rates to optimizing space and reducing labor demands, these systems provide essential benefits to modern poultry production. Their importance in the agricultural sector cannot be underestimated, as they enable farmers to meet growing demands in a sustainable and productive manner.
Challenges Faced with Large Chicken Incubators
In the realm of poultry farming, large chicken incubators play a crucial role. Despite their benefits, they also present numerous challenges that demand attention. Understanding these challenges helps farmers navigate potential pitfalls, ensuring optimal outcomes from the incubation process. Addressing these issues is essential not only for productivity but also for the welfare of the hatchlings. Without looking into the challenges, particularly technical malfunctions, temperature fluctuations, and humidity control issues, the effectiveness of an incubator can be severely compromised.
Technical Malfunctions
Technical malfunctions are one of the primary concerns when operating large chicken incubators. These machines are complex, with various components that must work in harmony. If any malfunction occurs, it can lead to catastrophic results, including the loss of eggs and reduced hatching success. Common malfunctions include failures in the heating elements, fan motors, or control boards. Even small issues, such as a blocked ventilation system, can escalate quickly.
Regular maintenance is paramount. Observing the incubator's performance and conducting routine checks can prevent many malfunctions. Keeping a log of maintenance activities is advisable. This allows farmers to track when parts may require replacement or servicing. Also, understanding the manufacturerβs guidelines about troubleshooting can aid in identifying issues early. Minimized downtime can be achieved through proactive maintenance practices. Therefore, addressing technical malfunctions is not just important; it's crucial for sustaining optimal incubation conditions.
Temperature Fluctuations
Temperature regulation is key to successful incubation. Large chicken incubators must maintain a steady temperature between 99 to 102 degrees Fahrenheit. Any fluctuation can adversely affect embryo development and lead to poor hatching rates. If the incubator experiences a temperature spike or drop, the eggs may develop abnormally, causing malformations or even death.
Monitoring systems should be in place to detect any deviations from the set temperature. Many modern incubators come equipped with alarms or notifications systems for this purpose. Adjustments may be necessary if the temperature consistently falls outside the normal range. Farmers should regularly check and calibrate the thermostat to ensure accuracy. Additionally, insulating the incubator can mitigate temperature changes caused by external factors. Proper insulation helps maintain a steady environment and enhances overall performance.
Humidity Control Issues
Humidity plays a critical role in the incubation process. For optimal hatching conditions, humidity levels should typically be maintained between 45-55% during the incubation period and increased to around 65% during the hatching phase. Insufficient humidity can lead to dehydration of the embryos, while excessive humidity can cause respiratory issues and mold growth.
Large chicken incubators can sometimes struggle to maintain the proper humidity levels due to malfunctioning water reservoirs or evaporation issues. Like temperature control, a monitoring system is recommended to track humidity levels continuously. Farmers can also utilize hygrometers to measure moisture accurately. Furthermore, ensuring that the incubator is appropriately ventilated can prevent humidity build-up.
Maintenance Best Practices
Maintaining large chicken incubators is essential for ensuring optimal functionality and successful hatch rates. Proper maintenance practices not only extend the life of the equipment but also enhance the overall efficiency of the incubation process. In this section, we will explore specific elements of maintenance, its benefits, and considerations that should be made by agricultural farmers and enthusiasts alike.
Regular Cleaning and Sanitization
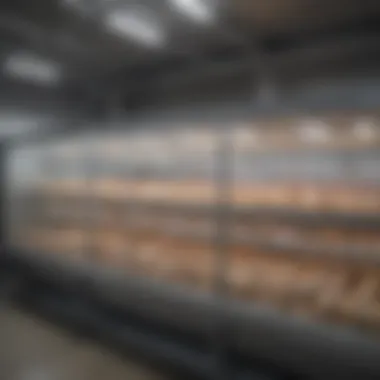
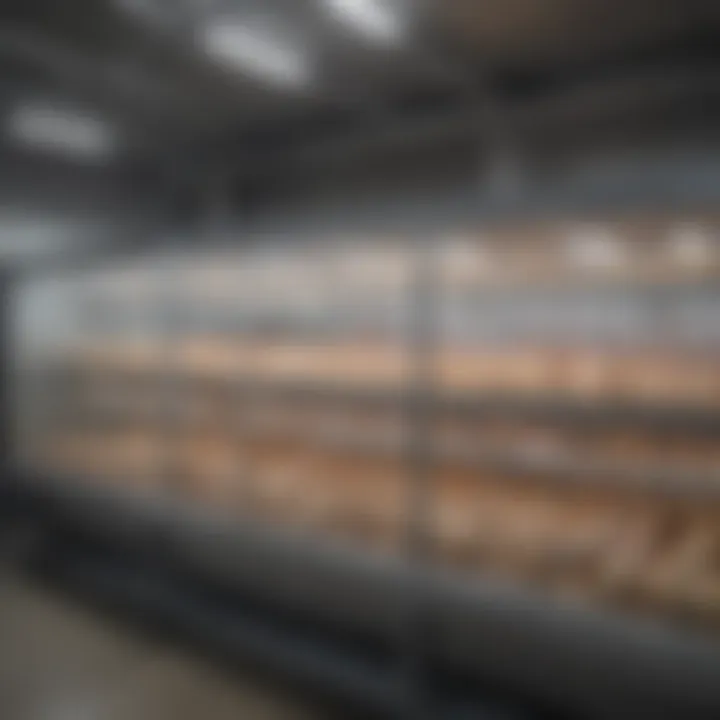
Regular cleaning and sanitization of large chicken incubators are crucial for preventing the buildup of harmful bacteria and pathogens that can affect the health of the eggs and chicks. Neglecting this step can lead to disease transmission, which ultimately compromises hatching success. Here are some important points:
- Frequency: Cleaning should be done before each incubation cycle. This ensures a fresh start each time.
- Procedure: Remove all trays and other components for cleaning. Use a non-toxic disinfectant suitable for poultry equipment. Rinse thoroughly to avoid any chemical residue.
- Drying: Allow components to dry completely before reassembling. Moisture can attract mold and bacteria, hindering effectiveness.
Cleaning and sanitizing not only protect the health of the flock but also allow for an accurate assessment of the incubator's condition.
Routine Part Checks
Conducting routine part checks is another practice that cannot be overlooked. Regular inspections of all mechanical and electronic components of large chicken incubators help to identify potential issues before they escalate. This practice involves checking:
- Heating Elements: Ensure that heating elements are functioning properly. Overheating or insufficient heating can result in poor hatchability.
- Humidity Control: Confirm that the humidity levels are being maintained without fail. Calibration should be done frequently to guarantee accuracy.
- Ventilation: Inspect the ventilation system to ensure that air circulation is adequate. Insufficient ventilation can lead to gas buildup, which is harmful to developing embryos.
By routinely checking these components, farmers can anticipate failures and implement corrective measures, leading to smoother operations.
Calibration of Sensors
Calibration of sensors is fundamental in maintaining large incubators, as accurate readings are essential for effective management of temperature and humidity. Ensuring that sensors are calibrated properly allows for better control over the incubation environment.
- Regular Calibration: Sensors should be calibrated at least once every month. This is especially important after major cleaning or part replacements, as shifts may affect their performance.
- Use of Standards: Employ reliable calibration standards to check the accuracy of temperature and humidity sensors. If discrepancies are identified, adjustments must be made immediately.
- Documentation: Keep detailed records of calibration checks. This will assist in identifying patterns and help manage equipment more effectively.
Proper calibration can significantly reduce the risk of hatching failures, ultimately leading to more successful outcomes.
Maintaining large chicken incubators through these best practices not only enhances egg incubation success but also promotes the longevity of the machinery involved. With diligent care, farmers can achieve better efficiency in their poultry operations.
Comparative Analysis: Large vs. Small Incubators
The choice between large and small chicken incubators can significantly impact the efficiency and productivity of poultry farming. Understanding the nuances of both types is essential for making informed decisions tailored to specific operational needs. This section will delve into two main aspects: cost-effectiveness and operational efficiency. By comparing these elements, farmers can determine which incubator best suits their requirements.
Cost-Effectiveness
Cost is a major factor in selecting an incubator. Large incubators often represent a higher upfront investment compared to their smaller counterparts. However, the method of calculating cost-effectiveness must take into account not only the initial purchase price but also long-term operational costs and benefits.
- Initial Investment: Large incubators tend to be pricier due to their advanced technologies and larger capacity.
- Economies of Scale: A larger capacity allows for the incubation of more eggs at once, reducing the cost per egg. For operations aiming for high hatch rates, this can lead to significant savings over time.
- Operational Costs: Factors such as energy consumption, maintenance, and repair must be evaluated. Larger incubators may have higher energy costs, but they are often designed for efficiency.
In summary, while large incubators require a larger initial outlay, they can offer better cost-effectiveness in the long run with careful planning.
Operational Efficiency
Operational efficiency focuses on how effectively an incubator can perform its function of hatching eggs. This factor includes aspects like ease of use, reliability, and the ability to maintain ideal conditions.
- Capacity Management: Large incubators can manage higher quantities of eggs simultaneously. This scalability is advantageous for farmers with larger flocks.
- Automation Features: Many large models come equipped with automatic temperature and humidity controls. This automation can reduce manual monitoring and involvement, allowing for more time-efficient management.
- Maintenance Needs: Smaller incubators may be less complex and easier to maintain, but they frequently require more frequent monitoring. Conversely, the robust design of larger incubators may require less regular intervention.
Ultimately, the choice between a large or small incubator hinges on specific goals and resources. Analyzing cost-effectiveness along with operational efficiency presents a clearer picture for poultry operations seeking to optimize their incubation processes.
Future Trends in Incubation Technology
The future of incubation technology is shaping the way poultry farming operates. As the need for efficiency, productivity, and sustainability grows, new innovations come to the forefront. Understanding these future trends can help farmers and enthusiasts make informed decisions and stay competitive in the evolving agricultural landscape. The rise of technology not only enhances the incubation process but also addresses challenges such as environmental concerns and labor shortages.
Smart Incubators
Smart incubators are becoming prominent in the poultry industry. These devices use advanced technology to monitor and control the incubation environment. With features like IoT connectivity and automated adjustments, smart incubators ensure optimal conditions for egg hatching. They provide data on temperature, humidity, and air quality, allowing users to track performance remotely.
The benefits of smart incubators include:
- Real-Time Monitoring: Farmers can receive alerts about significant changes in the incubation parameters. This enables quick responses to any issues.
- Data Analytics: By collecting data over time, users can analyze trends and make adjustments to enhance hatch rates.
- Energy Efficiency: Many smart incubators are designed to consume less energy, making them cost-effective over time.
This shift towards smart technology reflects a broader trend of adopting digital solutions in agriculture. It empowers farmers to optimize their operations and improve outcomes.
Sustainable Practices
Sustainability is another vital aspect of future incubation trends. The growing emphasis on eco-friendly practices drives poultry businesses to reduce their carbon footprints. Innovations focus on using renewable energy sources, minimizing waste, and improving resource management. Large chicken incubators are increasingly designed with sustainability in mind.
Key sustainable practices include:
- Energy Use Reduction: Employing solar panels or energy-efficient heating systems can significantly cut energy demands.
- Water Conservation: Implementing systems that recycle and manage water usage protects one of agriculture's most precious resources.
- Waste Management: Utilizing organic waste generated during the incubation process for composting or as animal feed supports a closed-loop system.
Sustainable practices not only appeal to consumer preferences but also ensure long-term viability for poultry operations.
Understanding and adopting these future trends will allow agriculture farmers and enthusiasts to stay relevant. By integrating technology and sustainability, poultry farming can evolve to meet the demands of modern society, benefiting both producers and consumers alike.
Epilogue
In reviewing the role of large chicken incubators, it becomes evident that they serve a vital function in modern poultry farming. Their capacity, design, and technology enable farmers to optimize hatch rates and efficiently manage egg incubation processes. This article has highlighted the various types of incubators available, focusing on forced air and still air models, which each hold unique strengths. The operational considerations, such as setting up the incubator and egg selection, are crucial to ensure successful hatching.
Recap of Key Points
- Types of Incubators: Forced air incubators and still air incubators offer different advantages. Understanding their operation helps in choosing the right equipment for specific needs.
- Key Components: Essential elements like heating mechanisms, humidity control systems, and temperature regulation are fundamental to achieving optimal incubation conditions.
- Operational Considerations: Effective setup and monitoring of the incubator significantly influence hatch outcomes.
- Benefits: Using large chicken incubators leads to increased hatch rates, better space utilization, and labor efficiencies.
- Challenges: Being aware of potential technical malfunctions and environmental fluctuations is critical for successful incubation.
- Maintenance Practices: Routine cleaning and calibration keep incubators functioning well and enhance reliability.
- Future Trends: Advancements in technology such as smart incubators and sustainable practices are shaping the future of incubation.
The Importance of Proper Incubation
Proper incubation is crucial for various reasons. It directly affects the survival and health of chicks. Accurate control of temperature and humidity, along with consistent monitoring, ensures that embryos develop in ideal conditions. Furthermore, understanding the needs of different breeds and adjusting incubation parameters accordingly can significantly improve hatch rates.
In summary, the insights provided here are essential for anyone involved in poultry farming. Large chicken incubators are not just tools; they are integral for agricultural prosperity and sustainability. Continuing education on best practices in incubation can provide farmers with the knowledge needed to adapt to evolving agricultural technologies and methodologies.