Understanding Hydraulic Press Companies: An In-Depth Exploration
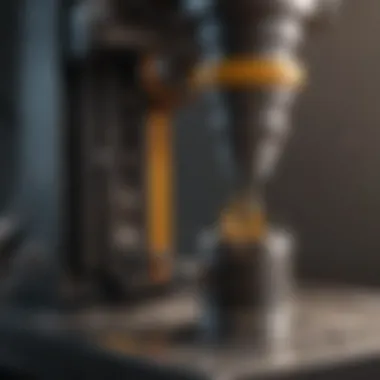
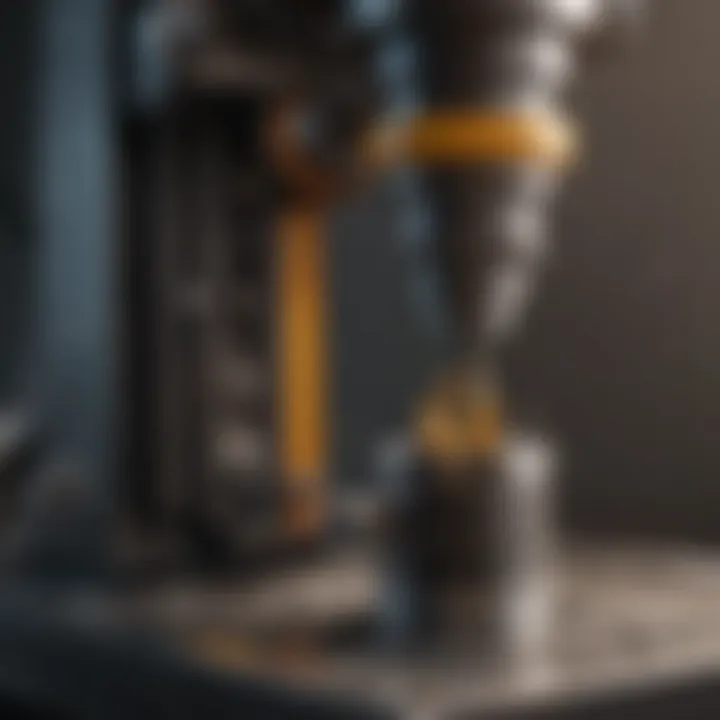
Intro
When exploring the hydraulic press industry, understanding its fundamental concepts is essential. Hydraulic presses are critical in various sectors, including manufacturing, automotive, and even agriculture. Their operational mechanisms and significance cannot be overstated. As we navigate through this detailed examination, we will look into core terminologies and historical context, recent innovations, practical applications, and techniques relevant to hydraulic press companies.
Hydraulic presses utilize fluids to generate significant force. The principles of hydraulics are based on Pascal's law, which states that a change in pressure applied to an incompressible fluid in a closed system is transmitted undiminished throughout the fluid. Recognizing these concepts lays the foundation for understanding the broader industry.
Key Concepts and Terminology
Basic Definitions
Hydraulic presses are machines that use hydraulic force to shape or manipulate materials. Common types of hydraulic presses include:
- C-frame hydraulic press: Known for its open design, suitable for various tasks.
- H-frame hydraulic press: More robust, allowing for heavier workloads.
- Bench hydraulic press: Compact and typically used for lighter applications.
Each type serves specific functions, all reliant on the same core hydraulic principles. The fluids used typically include oil or water, chosen for their ability to transmit force efficiently.
Historical Context
Hydraulic technology has a long-standing history. Its origins can be traced back to ancient civilizations utilizing water to power complex machinery. The evolution of hydraulic presses began in the 19th century, when notable figures like Joseph Bramah introduced advancements that enhanced industrial processes. As industries grew, so did the demand for efficient machinery, leading to the refinement and popularization of hydraulic pressing.
Recent Innovations and Trends
Technological Advancements
In recent years, hydraulic press technology has seen numerous innovations. Automation has become a significant trend, with the integration of robotics for optimized efficiency. Computer Numerical Control (CNC) systems also allow for precise operations, significantly reducing human error.
Beyond efficiency, manufacturers are focusing on smarter hydraulic systems that incorporate advanced sensors and data analytics. These advancements not only streamline operations but also enhance the overall quality of the produced components.
Sustainable Practices
Sustainability is another area gaining traction. Hydraulic press companies are adopting greener practices by using eco-friendly fluids and reducing energy consumption. Recycling waste materials has also become more common, promoting a circular economy within the industry. These measures are not merely trends but represent a genuine commitment to responsible practices in manufacturing.
Practical Applications and Techniques
Step-by-step Guides
Understanding how to utilize hydraulic presses effectively can boost productivity.
- Assess the Material: Evaluate the type and thickness to select the appropriate press type.
- Set the Die: Properly align the die to ensure efficient force application.
- Calibrate Pressures: Adjust the fluid pressure based on the material requirements.
- Initiate Pressing: Gradually apply force and monitor operations to avoid damage.
Case Studies
Several sectors rely heavily on hydraulic presses. In agriculture, hydraulic presses are used in the production of bales, allowing farmers to optimize storage and shipping. Automotive industries utilize presses for parts like frames and panels, ensuring high precision and strength.
"Hydraulic presses are integral to modern manufacturing, enabling tasks that are otherwise too difficult or labor-intensive."
By examining these aspects, readers can appreciate the complexities of hydraulic press technology and its applications.
Overall, hydraulic press companies play a significant role in various domains, further highlighting the importance of understanding their mechanisms and advancements.
Intro to Hydraulic Press Technology
In the realm of manufacturing and mechanical engineering, hydraulic press technology plays a crucial role. Understanding this technology can help stakeholders recognize how these machines enhance efficiency and precision in production processes. Hydraulic presses are widely used across various industries, from automotive to agriculture. Their significance extends beyond simple machinery; they incorporate advanced engineering principles that address intricate manufacturing needs.
Definition of Hydraulic Press
A hydraulic press is a machine that uses a hydraulic cylinder to generate compressive force. This force is applied to shape, form, or cut materials, which can include metals, plastics, and wood. The hydraulic system operates on Pascal's principle, which states that an enclosed fluid transmits pressure uniformly in all directions. This principle allows hydraulic presses to exert immense pressure with comparatively little input force. This efficiency makes them valuable in production scenarios where precision and power are essential.
History and Evolution
The history of hydraulic pressing dates back to ancient engineering concepts, where simple hydraulic systems were used in various constructions. However, the modern hydraulic press began to gain traction in the 18th century, thanks to further advancements in technology. The initial designs were rudimentary, often limited in force output and application. With time, hydrostatic systems evolved significantly. By the 19th and 20th centuries, the hydraulic press became a staple in manufacturing processes. Evolving from steam-based power to electricity-driven hydraulic systems, the technology continued to improve, increasing mechanical efficacy and automation in numerous industries. Today, hydraulic presses feature sophisticated control systems that enhance precision and safety, marking a significant transformation from their early counterparts.
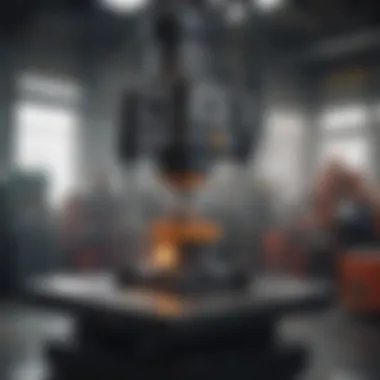
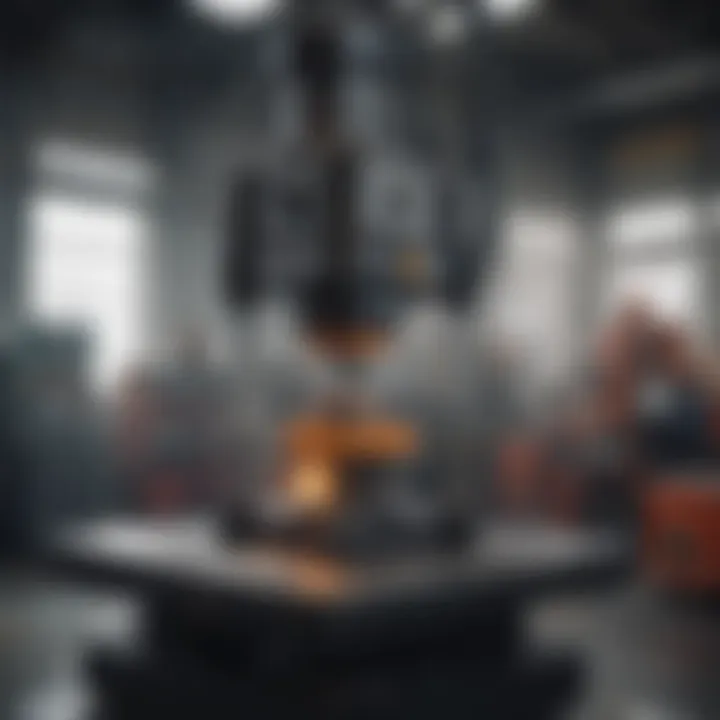
Understanding Hydraulic Press Companies
Understanding hydraulic press companies is crucial for anyone interested in the manufacturing and industrial landscape. These companies play a pivotal role in various sectors, from automotive to agriculture. Hydraulic presses are fundamental tools used for shaping, molding, and compressing materials through hydraulic force. By exploring the operational mechanisms of these companies, we gain insight into their significance in enhancing productivity and efficiency. Additionally, recognizing the benefits they bring—including improved manufacturing processes and adaptability to different materials—helps appreciate their contributions to modern industry.
Key Players in the Industry
The hydraulic press industry features several key players, each contributing significantly to technological advancements and market dynamics. Notable companies include:
- Schuler Group: A leader in stamping technology, their hydraulic presses are used extensively in the automotive sector.
- Komatsu Industries: Known for their robust machinery, they offer a range of hydraulic press solutions for various applications.
- Hyundai Wia: This company focuses on innovative hydraulic technology to deliver high-performance presses.
- Aida Engineering: Recognized for their precision-engineered machines, they cater to diverse industries.
These players influence industry trends through research and development efforts, striving to create more efficient and effective hydraulic solutions. Their contributions not only shape current practices but also pave the way for future innovations.
Operational Framework
The operational framework of hydraulic press companies encompasses several critical components that ensure smooth functioning. Key elements include:
- Research and Development: Continuous investment in R&D is essential for innovation and maintaining competitive advantage. Companies often collaborate with engineers and technical experts to design more effective presses.
- Manufacturing and Production: The manufacturing process involves sourcing high-quality raw materials, such as steel and hydraulic components. These materials undergo strict quality control to ensure reliability.
- Sales and Marketing: Understanding target markets helps companies position their products effectively. Sales strategies often focus on highlighting the efficiency and effectiveness of hydraulic presses.
- After-Sales Support: Providing maintenance and repair services is critical. Companies need to support clients post-purchase to ensure optimal performance of hydraulic systems,
In summary, the operational framework supports both production and customer satisfaction, ensuring long-term success for hydraulic press companies. Their adaptability to market demands and commitment to quality are vital for thriving in this competitive landscape.
Manufacturing Process of Hydraulic Presses
The manufacturing process of hydraulic presses is a critical component in their overall functionality and reliability. Understanding this process is essential for those interested in the engineering behind these machines, especially for agricultural farmers who may utilize them for various tasks. The quality and efficiency of hydraulic presses directly impact productivity and cost-effectiveness in operations. Moreover, a well-designed manufacturing process enhances the lifespan of the presses and ensures better performance under different conditions.
Design and Engineering
Design and engineering are the backbone of the hydraulic press manufacturing process. Every hydraulic press must be designed with specific applications in mind. The design phase involves detailed drafting and calculations to ensure that the machine can withstand high pressures while performing optimally. Engineers consider various factors during this stage, including:
- Load requirements: Each application may demand different load capacities. The design must accommodate these varying needs without compromising safety.
- Ergonomics: The user interface and operational commands should be intuitive and accessible, especially in industries like agriculture, where operators might not have advanced training.
- Safety features: It is essential to integrate safety measures to minimize hazards associated with high-pressure operations.
Material Selection
Material selection is a profound aspect in the manufacturing process of hydraulic presses. The materials used greatly influence the durability, performance, and safety of the machine. Key considerations include:
- Strength and toughness: Steel is commonly used for the frame and components due to its strength. Material must endure the operational stress without deforming or breaking.
- Corrosion resistance: Especially important in agricultural settings where exposure to various elements is frequent. Materials that resist rust and corrosion can prolong the lifespan of the press.
- Weight: The weight of the components affects mobility. In farming, lighter machines can be advantageous for ease of transport.
Quality Control Measures
Quality control measures are invaluable in the manufacturing process of hydraulic presses. The significant risks linked to hydraulic machinery necessitate thorough inspections and tests.
A systematic approach includes:
- Material inspection: Before manufacturing begins, the quality of incoming materials is verified to ensure they meet specified standards.
- Dimensional checks: As parts are fabricated, precise measurements are taken to guarantee they fit together correctly during assembly.
- Functional testing: Once assembled, the hydraulic press undergoes rigorous testing to check for leaks, pressure endurance, and operational functionality.
In summary, the manufacturing process encompasses rigorous design, thoughtful material selection, and ongoing quality control. These elements work together to produce hydraulic presses that meet the demanding needs of industries, including agriculture.
"Well-manufactured hydraulic presses provide unmatched reliability and efficiency, crucial for maximizing productivity in farming operations."
Understanding these components can help farmers make informed choices when selecting and using hydraulic presses for their applications.
Applications of Hydraulic Presses
The significance of hydraulic presses in various sectors cannot be overstated. These machines are pivotal in transforming raw materials into finished products. Their ability to apply high levels of pressure with remarkable precision allows industries to maximize efficiency and minimize waste. Understanding the applications of hydraulic presses is crucial for stakeholders in the manufacturing ecosystem, including manufacturers, engineers, and operational managers.
- Flexibility: Hydraulic presses are adaptable for diverse applications. They serve functions in forming, bending, punching, and stamping materials across multiple sectors.
- Cost-Effectiveness: These machines enable large-scale production while reducing operational costs. The minimal labor required compared to traditional methods is a notable advantage.
- Precision Work: Hydraulic presses can achieve tight tolerances. This precision is essential where accuracy is vital, such as in the automotive sector.
"Hydraulic presses represent a crucial technological advancement, allowing industries to optimize processes and enhance production capabilities."
Industrial Manufacturing
In industrial manufacturing, hydraulic presses play an indispensable role. They are commonly used for metal forming, where intricate shapes need to be achieved. Processes like forging or die-casting depend heavily on hydraulic presses. Manufacturers can leverage these machines to produce complex components with tight compliance to specifications.
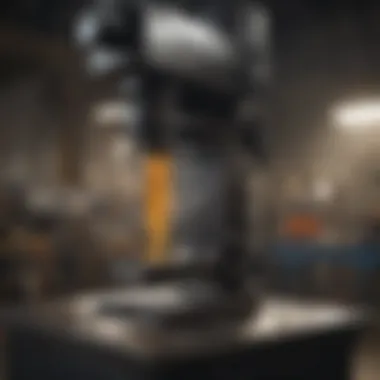
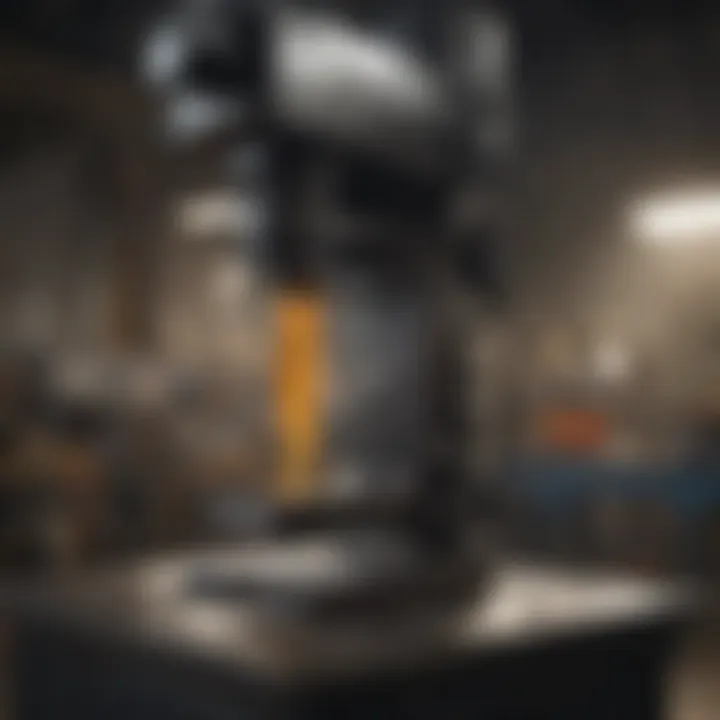
- Auto Parts Production: In the manufacturing of auto components, hydraulic presses ensure structural integrity and reliability.
- Material Formation: From shaping metal sheets to crafting intricate designs in polymers, their capacity to easily mold materials under pressure is crucial.
Automotive Industry
The automotive industry relies heavily on the efficiency of hydraulic presses. These machines are involved at every stage of vehicle production, from assembling parts to forming body shapes. The challenges of modern automotive manufacturing demand high precision and reliability, both addressed with hydraulic technology.
- Bending and Stamping: Hydraulic presses are used to bend and stamp massive sheets of metal, transforming them into bodywork and structural components.
- Component Assembly: They also assist in assembling smaller parts, ensuring that every piece fits perfectly, ultimately improving vehicle safety.
Recycling Processes
In recycling, hydraulic presses serve a critical function. They compress materials, which reduces volume and facilitates transportation cost savings. The recycling industry values their efficiency in handling diverse materials such as metals, plastics, and paper.
- Compaction: Hydraulic presses compact waste materials into bales, making it easier for processing facilities to manage and recycle them.
- Energy Recovery: The increasing emphasis on sustainability drives the use of hydraulic technology to improve energy recovery initiatives.
Understanding these applications enables stakeholders to appreciate the critical role hydraulic presses play in modern processes across various industries. Their capacity to facilitate production, enhance efficiency, and support sustainable practices makes them a central piece of machinery in industrial operations.
Technological Advancements in Hydraulic Presses
Technological advancements play a pivotal role in enhancing the efficiency and capabilities of hydraulic presses. This topic is critical as it highlights how innovation can lead to improved performance, reliability, and safety within the hydraulic press industry. As agricultural demands grow, staying up-to-date with technology becomes essential for manufacturers and users alike. Significant elements include automation, control systems, and energy-efficient designs.
Automation and Control Systems
Automation in hydraulic presses refers to the integration of technology to optimize operation processes. This includes computerized systems that manage the press's functions. Such systems can monitor performance, adjust settings, and provide feedback in real-time. Automation offers several benefits:
- Increased Precision: Automated control systems enhance the accuracy of pressure application, leading to better product quality.
- Reduced Labor Costs: Fewer manual interventions are needed, lowering workforce expenses.
- Enhanced Safety: Automating processes minimizes human exposure to potential hazards in high-stress environments.
The sophistication of these systems enables remote monitoring. Operators can access data and control settings from different locations, which is pivotal for operation managers overseeing multiple units. Due to this, companies can adapt to rapid changes in production demands, thereby optimizing efficiency.
Energy Efficiency Improvements
Energy efficiency is becoming a cornerstone of modern hydraulic press designs. With rising energy costs and environmental concerns, manufacturers concentrate on creating systems that require less power to operate. Several advancements contribute to this goal:
- Variable Speed Drives: These allow presses to operate at different speeds and power levels, reducing energy use during non-peak times.
- Energy Recovery Systems: Some modern presses can harness the energy generated during pressing operations, which can be redirected for further use.
- Improved Hydraulic Fluids: The use of synthetic oils can decrease friction, leading to lower energy consumption.
Energy-efficient designs not only reduce operational costs but also contribute to sustainability in manufacturing practices.
By aligning with these advancements, hydraulic press companies not only enhance their market competitiveness but also demonstrate responsibility towards environmental stewardship. The future of hydraulic presses is about blending technology with practical applications that benefit both users and the planet.
Safety Standards and Regulations
Safety standards and regulations within the hydraulic press industry are critical not only for operational integrity but also for the protection of workers and the surrounding environment. Hydraulic presses, by their nature, exhibit high levels of force, which can lead to severe accidents if proper measures are not adhered to. The presence of extensive regulations ensures a safe working environment and helps mitigate risks, making it an indispensable aspect of hydraulic press companies’ operations.
Importance of Compliance
Compliance with safety standards is paramount for hydraulic press manufacturers and operators. Adhering to regulations helps to safeguard employees from potential injuries caused by equipment malfunctions or misuse. This compliance is often guided by local, national, and international standards set by agencies such as the Occupational Safety and Health Administration (OSHA) in the United States or the International Organization for Standardization (ISO).
The benefits of strict compliance include:
- Reduction of accidents: Regular maintenance and adherence to standards significantly decrease the potential for accidents.
- Improved workplace morale: Employees are more confident working in an environment where safety regulations are prioritized.
- Legal protection: Compliance can also protect companies from legal repercussions in case of accidents.
Understanding and implementing these safety regulations contributes to the overall efficiency of operations, making it an essential focus in hydraulic press companies.
Assessment and Certification
Assessment and certification processes are critical components that ensure compliance with safety standards. These processes typically involve third-party audits, inspections, and evaluations of manufacturing practices and equipment.
- Third-party audits: Independent organizations often conduct audits to verify that companies meet safety regulations. This unbiased evaluation is crucial for instilling trust in consumers and stakeholders.
- Certification: Many hydraulic press manufacturers pursue certifications such as ISO 9001, which signify adherence to quality management principles. These certifications not only enhance credibility but also reflect a commitment to safety.
- Continuous improvement: Assessment processes highlight areas for improvement, prompting companies to refine their practices continuously.
"Safety isn't expensive, it's priceless."
This quote encapsulates the essence of investing in safety standards within hydraulic press operations.
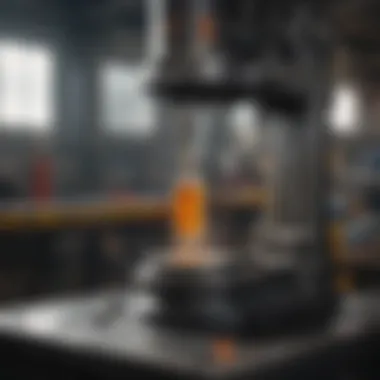
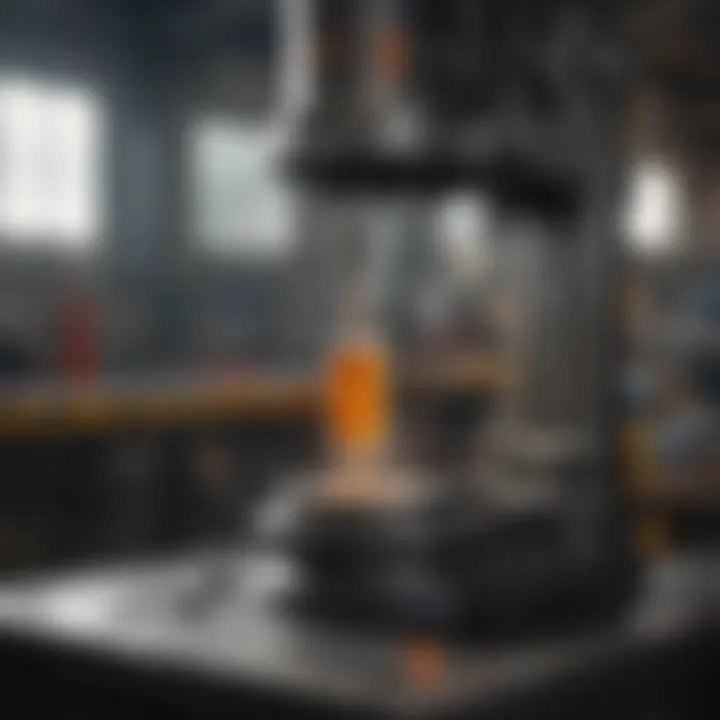
Market Trends and Future Outlook
The hydraulic press industry is dynamic, reflecting the broader trends in manufacturing and technology. Examining market trends and future outlook helps understand where hydraulic press companies are headed. Their significance spans innovations and changing demands. It guides stakeholders in making informed decisions about investments and strategies.
Emerging Markets
Emerging markets are crucial for the expansion of hydraulic press companies. Countries like India, Brazil, and Mexico have increased demand for industrial automation. These markets are experiencing strong growth due to rising industrial activities. The automotive and aerospace sectors are leading contributors.
Key factors driving growth in these markets include:
- Increased industrial activities: As industries evolve, demand for hydraulic presses grows.
- Government initiatives: Many governments support modernization of manufacturing.
- Foreign investments: International players are increasingly entering these markets, accelerating growth.
Companies are adapting their product offerings to cater to local needs, enhancing accessibility and affordability. The hydraulic press market in these regions is projected to expand significantly, providing myriad opportunities.
Forecast of Industry Growth
The forecast for hydraulic press companies is promising. Industry analysts predict steady growth over the next five to ten years. Factors influencing this growth include:
- Technological advancements: Innovations in hydraulic press design improve efficiency and effectiveness.
- Sustainable practices: Growing importance of sustainability drives investment in energy-efficient and eco-friendly hydraulic presses.
- Integration of automation: Many companies are adopting automated solutions to enhance productivity and reduce human error.
Additionally, key industry players are investing heavily in research and development. This focus on innovation ensures they remain competitive in the global landscape.
Overall, understanding market trends allows hydraulic press companies to strategize more effectively. They can tap into emerging opportunities that influence future growth and development.
Challenges Faced by Hydraulic Press Companies
Understanding the challenges hydraulic press companies encounter is essential for grasping the dynamics of this industry. As global demand for hydraulic presses increases, these companies face a myriad of obstacles that can impact their operations and profitability. Addressing these challenges requires strategic insight and innovative approaches.
Competition and Market Saturation
The hydraulic press market is characterized by intense competition. Many firms vie for market share, creating a saturated environment. Larger companies often leverage economies of scale, allowing them to offer lower prices, which can be detrimental for smaller enterprises.
Key factors contributing to competition in this market include:
- Product Differentiation: Companies need to emphasize unique features of their presses, such as energy efficiency or advanced automation.
- Service Offerings: Providing comprehensive customer support can give companies an edge. Maintenance contracts or training programs can foster loyalty among buyers.
- Innovation: Keeping up with industry trends requires continual investment in research and development. Companies must innovate to remain relevant in a saturated landscape.
Firms that do not adapt to these competitive pressures may struggle to maintain their market position. Therefore, recognizing the importance of distinct value propositions is paramount for survival.
Technological Adaptations
Adapting to technological advancements poses both a challenge and an opportunity for hydraulic press companies. The emergence of smart technology, particularly in automation and remote monitoring, is reshaping the expectations of manufacturers. Those who cannot keep pace with these technological shifts may find themselves out of touch with market demands.
Some critical technological adaptations include:
- Integration of Automation: Advanced robotic systems streamline production processes, improving efficiency.
- Energy Efficiency: Implementing energy-saving technologies reduces operational costs and meets regulatory standards.
- Data-Driven Decisions: Collecting and analyzing data from press operations can enhance productivity and minimize downtime.
Continuous adaptation to technology is not simply advantageous but required. Companies that embrace these changes will find opportunities for growth and market differentiation.
"In an industry where innovation is the norm, falling behind in technology can mean the end for many companies."
Overall, understanding the challenges faced by hydraulic press companies aids stakeholders in navigating a complex environment. By focusing on competition and leveraging technological advancements, these companies can secure their future in the hydraulic press market.
Epilogue
The conclusion serves as a pivotal reflection on the various aspects discussed in this article regarding hydraulic press companies. Understanding these elements is essential for stakeholders in the hydraulic press sector, which includes manufacturers, customers, and industry analysts. The hydraulic press industry is not only crucial for manufacturing but also plays a significant role in various other applications, such as recycling, automotive production, and more.
Summary of Key Insights
In reviewing the key insights throughout this article, we uncover several significant points:
- Industry Relevance: Hydraulic presses are integral in many industries, enhancing productivity and efficiency. Their applications span from industrial manufacturing to recycling processes, demonstrating their versatility.
- Technological Advancements: The focus on automation and energy efficiency marks a transformative shift in how hydraulic presses are designed and utilized. Companies adopting these technologies can significantly improve their operational efficiency and reduce costs.
- Safety and Compliance: Adhering to safety standards is non-negotiable. Compliance not only ensures worker safety but also enhances the company's reputation in the industry. Regular assessments and certifications validate a company's commitment to quality and safety.
Overall, these insights present a comprehensive picture of how hydraulic press companies operate and evolve in response to market demands.
Final Thoughts on Hydraulic Press Companies
As we conclude our exploration, it is evident that hydraulic press companies are vital to modern manufacturing and other sectors. Their ability to adapt to changing technological landscapes and market needs will dictate their future. Businesses must remain aware of market trends and challenges such as competition and technological adaptations.
In summary, a thorough understanding of hydraulic press companies equips readers, especially agricultural farmers and enthusiasts, with the knowledge to appreciate the significance of these machines. The hydraulic press industry fosters innovation, efficiency, and safety, reinforcing its importance in various fields. By embracing advancements and adhering strictly to safety standards, hydraulic press companies can secure their position as leaders in the industry.