Track Undercarriage: Insights for Equipment Maintenance
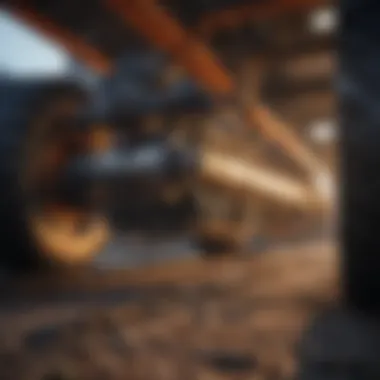
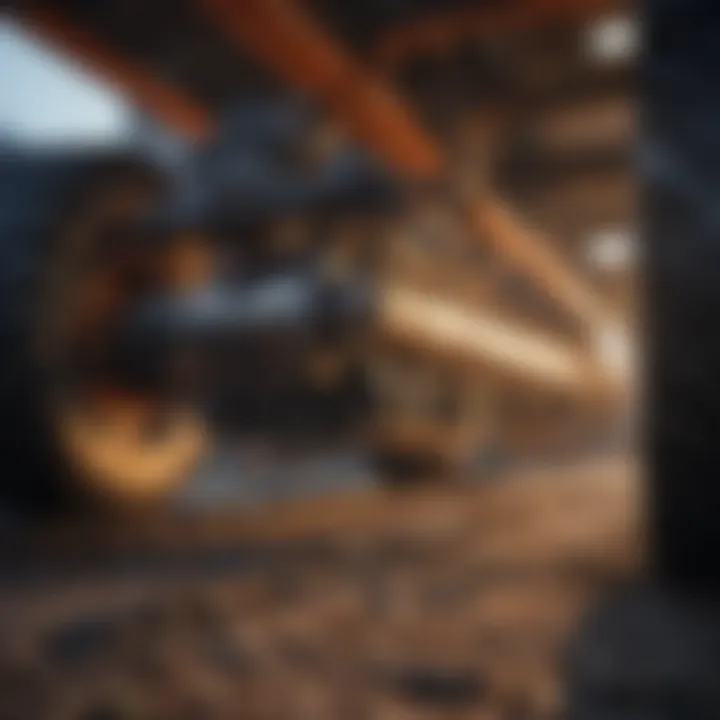
Intro
The undercarriage of agricultural equipment plays a vital role in its overall performance and durability. Understanding the fundamental aspects of track undercarriage systems is essential for anyone involved in maintaining agricultural machinery. This section will lay the groundwork for comprehending the design, function, and significance of undercarriage systems, setting the stage for deeper exploration throughout the article.
Key Concepts and Terminology
Basic Definitions
Track undercarriage refers to the assembly that supports the equipment's weight and facilitates movement over various terrains. Key components include tracks, rollers, and frames. Each of these parts has distinct roles that contribute to the effective functioning of the undercarriage system.
- Tracks: These are the broad bands that make contact with the ground. They disperse the equipment's weight and reduce soil compaction.
- Rollers: These components assist the movement of the tracks, allowing for smooth operation over uneven surfaces.
- Frames: The structure that holds everything together, ensuring stability and durability.
Historical Context
The evolution of track undercarriages can be traced back to early agricultural machinery. As the demand for efficient farming increased, different designs were introduced to enhance the adaptability and strength of machinery. Initially, metal tracks were heavy and cumbersome, but technology has since evolved significantly.
From the introduction of rubber tracks to modern hydraulic systems, innovation has consistently aimed at improving performance while reducing maintenance needs. This historical perspective helps appreciate the advancements in technology and design that have shaped today's agricultural practices.
Recent Innovations and Trends
Technological Advancements
In recent years, technology in track undercarriage systems has progressed notably. Some key innovations include:
- Composite Materials: Modern tracks often use lightweight but durable materials that enhance performance and reduce wear.
- Smart Sensors: These technologies are now integrated to monitor wear and tear in real-time, allowing for predictive maintenance.
- Automated Adjustments: Newer systems can automatically adjust tension based on soil conditions, which optimizes the machine's operation.
Sustainable Practices
Sustainability is an increasing focus in agriculture. The design and manufacturing processes of track undercarriages are shifting toward more eco-friendly practices. This includes:
- Recyclable Materials: Utilizing materials that can be recycled after their service life.
- Energy Efficiency: Designs that reduce fuel consumption while maintaining high functionality.
- Soil Conservation Techniques: Tailoring designs to minimize soil disturbance and promote healthier land.
Practical Applications and Techniques
Step-by-step Guides
For effective maintenance of track undercarriages, follow these recommended practices:
- Regular Inspections: Check for signs of wear or damage at regular intervals.
- Cleaning: Remove debris and dirt to prevent corrosion and build-up that can hinder performance.
- Lubrication: Ensure all moving parts are adequately lubricated to reduce friction and wear.
- Replace Worn Parts: Address any damaged components promptly to avoid more significant issues.
Case Studies
One notable case is the implementation of smart sensors in John Deere's latest line of machinery. These sensors have resulted in a significant reduction in maintenance costs and downtime. By monitoring the undercarriage's performance, farmers can plan repairs more effectively, leading to a more efficient use of resources.
"Understanding the role of track undercarriages is key to optimizing agricultural machinery performance and expanding the life span of equipment."
Through this exploration, it is clear that grasping the complexities of track undercarriage systems is not just beneficial, but essential for achieving optimal machinery performance and ensuring a sustainable agricultural future.
Overview of Track Undercarriages
Track undercarriages are fundamental to the performance of agricultural machinery. Their design and maintenance have a direct impact on both the efficiency and longevity of high-value equipment. Understanding track undercarriages is essential for farmers and machinery operators who seek to maximize productivity while minimizing operational costs.
Definition and Functionality
A track undercarriage refers to the system of components that supports and drives agricultural equipment using continuous tracks rather than wheels. This system enhances traction and stability, especially in softer soil conditions, making it suitable for various agricultural tasks. The functionality of track undercarriages allows machinery to exert lower ground pressure, reducing soil compaction during operations. This is crucial for preserving soil health, especially in crop production.
Components of Track Undercarriages
The track undercarriage system comprises several critical components. Each plays a significant role in ensuring that the equipment operates smoothly and efficiently. The main components include:
Track links
Track links are the basic building blocks of the track system. They connect to form a continuous loop that drives the machinery. Their durability is a key characteristic, as they need to withstand substantial operating stress. Most agricultural equipment benefits from the robust nature of metal track links, which can handle rough terrain and heavy loads. However, using track links made from heavier materials can increase wear on other components, so balance is necessary.
Rollers
Rollers aid the movement of the machinery by supporting the weight and facilitating smooth track travel. They reduce friction between the track and the undercarriage, which is vital for performance. A notable feature of many rollers is their ability to self-lubricate, which can extend their lifespan. On the downside, if not regularly maintained, roller bearings can accumulate dirt, leading to premature wear and operational failures.
Idlers
Idlers support the upper structure of the track system, maintaining tension on the track to prevent it from slipping off during operation. The design of idlers allows for efficient tracking and reduces the potential for track misalignment. Their capability to absorb impacts is a major advantage, although improper adjustment can result in excessive wear and poor performance.
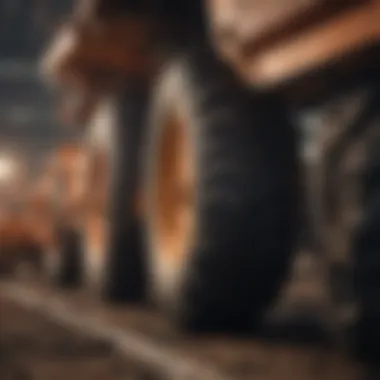
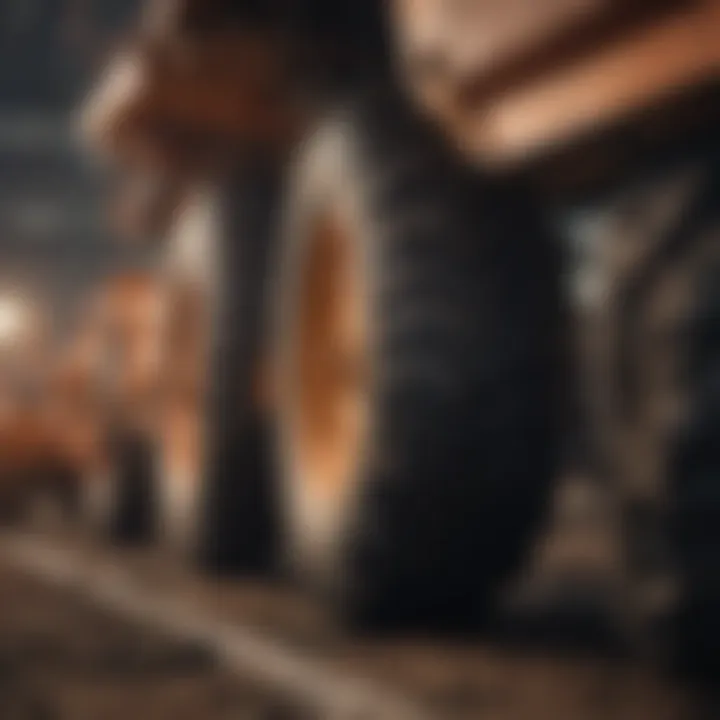
Suspension components
Suspension components provide a cushion between the machine and the ground, enhancing the comfort of the operation. This is particularly important in agricultural work, where uneven terrain is common. A well-designed suspension can prevent excessive vibrations, which can lead to equipment fatigue over time. However, complex suspension systems may require more maintenance, which could increase operational costs.
Understanding these components and their roles allow equipment operators to make informed decisions regarding maintenance and repairs. This understanding is crucial for optimizing the life cycle and efficacy of agricultural machinery.
Importance of Track Undercarriage Systems
The effectiveness of agricultural equipment is closely linked to the performance of its track undercarriage system. Understanding the importance of this system can greatly impact overall operational efficiency. Track undercarriage systems absorb weight and provide stability, enabling machinery to navigate various terrains. Their role is not only functional but also critical in determining how effectively equipment can perform its intended tasks.
Impact on Equipment Performance
Equipment performance hinges greatly on the integrity of the undercarriage. A well-functioning track undercarriage enhances traction, enabling machinery to operate smoothly, even in challenging conditions. This smooth operation translates into several benefits:
- Increased Efficiency: A robust undercarriage maintains optimal contact with the ground, ensuring that the machine utilizes its power effectively. This leads to less energy consumption and improved productivity.
- Enhanced Durability: Regular maintenance of the track undercarriage reduces wear and tear on the entire machine. This results in lower repair costs and extends the service life of the equipment.
- Predictable Maintenance Needs: With a dependable undercarriage, maintenance schedules become easier to predict. This predictability minimizes downtime and allows operators to plan for repairs and services more efficiently.
When the undercarriage is compromised, the entire system suffers. Loss of traction or increased vibration can lead to premature breakdowns, affecting the productivity and reliability of agricultural operations.
Role in Soil Preservation
Track undercarriage systems also play a significant role in soil preservation. The footprint left by heavy machinery can compact soils, leading to a host of agricultural issues. Here are several reasons why careful management of track undercarriages is vital for soil health:
- Minimizing Soil Impact: Designed to distribute weight evenly, track undercarriages reduce soil compaction, preserving the structure of the soil and promoting healthier crop growth.
- Promoting Water Retention: Less compaction helps maintain pore spaces within the soil, leading to better water infiltration and retention. This is crucial in both drought conditions and heavy rainfall scenarios.
- Enhancing Soil Aeration: A well-maintained undercarriage prevents excessive pressure on the soil surface, allowing for improved aeration. Healthy soil aeration supports microbial activity, essential for plant growth and nutrient cycling.
"Investing in track undercarriage systems is not just about machinery efficiency; itβs a commitment to sustainable agriculture."
Types of Undercarriage Systems
Understanding the types of undercarriage systems is essential for maximizing the potential of agricultural equipment. Different systems offer unique benefits and considerations that impact performance, durability, and operational efficiency. The correct choice can lead to better traction, reduced soil compaction, and enhanced equipment longevity. Let's explore the two primary types of undercarriage systems: rubber tracks and steel tracks.
Rubber Tracks
Rubber tracks are a popular choice in agricultural machinery due to their flexibility and versatile performance. They provide several advantages that appeal to operators working in diverse farming conditions.
Advantages
Rubber tracks offer superior traction on soft and uneven ground. This characteristic is crucial for ensuring operations in muddy or loose soil where conventional tires may struggle. Furthermore, rubber tracks distribute the machine's weight across a broader surface area, minimizing soil compaction. This is especially important in preserving soil structure and health, as high compaction can hinder water infiltration and root growth.
Another key aspect of rubber tracks is their quieter operation compared to steel tracks. The softer materials absorb much of the noise that can be generated during machinery operation, leading to a calmer working environment.
The maintenance of rubber tracks can also be more straightforward. While they still require care, issues like punctures may be easier and less costly to repair than those associated with steel tracks. Rubber's resistance to wear and tear further extends its usability, making it a beneficial option for many agricultural operators.
Disadvantages
Despite their advantages, rubber tracks come with certain downsides. One major consideration is their cost. Rubber tracks are often more expensive upfront than their steel counterparts. This can be a significant factor for budget-conscious farmers.
Additionally, rubber tracks may not be as effective in extremely rocky or abrasive environments. They can suffer from wear and tear when exposed to sharp objects or rugged terrain. This limits their applicability in certain agricultural sectors where conditions might be less forgiving.
Steel Tracks
Steel tracks stand out for their strength and durability, making them suitable for specific applications where toughness is prioritized. Understanding their advantages can help in deciding when they are the right fit.
Advantages
One of the primary advantages of steel tracks is their incredible durability. They are built to withstand harsh conditions, including rocky terrains and heavy loads. This robustness can reduce downtime and repair costs in the long run, as they are less likely to sustain damage from challenging surfaces.
Steel tracks can also provide better traction on harder surfaces, making them ideal for certain types of farming or construction applications. Their ability to grip onto rugged terrain enhances stability and support, especially for heavy machinery.
Disadvantages
However, steel tracks do possess certain disadvantages. One noteworthy aspect is their weight. Steel tracks are heavier than rubber tracks, which can impact the overall weight distribution of the equipment. This increased weight can lead to soil compaction, counteracting efforts to maintain soil health.
Moreover, steel tracks create more noise during operation. This can be a concern for those working in quieter environments or focusing on environmentally friendly farming practices.
Factors Affecting Undercarriage Performance
The performance of track undercarriages is influenced by several critical factors. Understanding these elements helps in optimizing equipment operation and prolonging the service life of agricultural machinery. Each factor, from soil type to weight distribution, plays a role in overall performance. Addressing these aspects can enhance traction and stability while reducing wear and tear.
Soil Type and Conditions
Soil type is a primary determinant of undercarriage performance. Different soil conditions, like clay or sandy soils, offer varying degrees of resistance against movement.
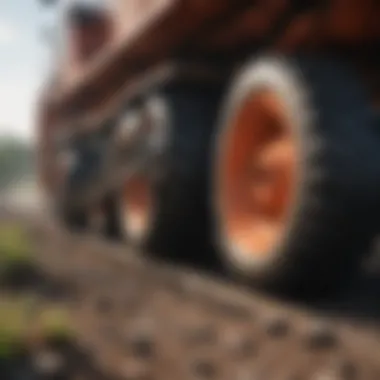
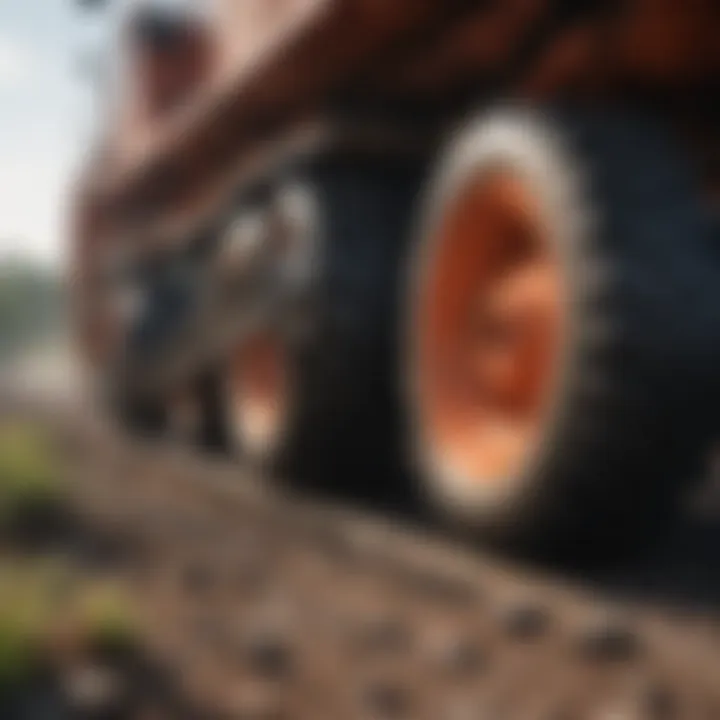
- Clay soils: They tend to hold water and can become sticky. This may cause increased rolling resistance as tracks struggle to maintain grip.
- Sandy soils: While they provide less resistance, sandy conditions can lead to rapid track wear due to the abrasive nature of the particles.
Additionally, moisture levels play a critical role. Wet soils can result in greater slippage, affecting the traction of the equipment. Implementing strategies such as choosing the right track systems for specific soil types can significantly improve efficiency in agricultural tasks.
Operating Weight and Load Distribution
The operating weight and load distribution of agricultural machinery are vital to effective track undercarriage performance. Each machine has a specified load capacity, and exceeding this limit can lead to several issues, including:
- Increased Wear: Excess weight puts additional stress on all components, leading to premature failure.
- Uneven Tracking: If the load is not evenly distributed across the tracks, it can create uneven wear and impact tractor stability.
Proper load management and regularly monitoring weight can help ensure that the undercarriage operates within its optimal range. This can lead to lower maintenance costs and longer intervals between repairs.
Terrain and Inclines
The terrain on which agricultural equipment operates also significantly impacts undercarriage performance. Challenging landscapes, such as hills and slopes, require more power and stability.
- Inclines can lead to: Increased strain on the undercarriage, especially if the equipment is working against gravity. This can result in slip, loss of traction, and potential track derailing.
- Flat terrain: While generally easier for equipment, varying surface conditions must still be considered, such as rocks and ruts.
Adjusting driving techniques and ensuring the machinery is equipped to handle specific terrain conditions is crucial for efficient operation. Equipment tuning might be necessary for optimal performance across diverse terrains.
Keeping these factors in mind while maintaining and operating undercarriages is essential for maximizing efficiency and minimizing maintenance expenses.
Maintenance of Track Undercarriages
Maintaining track undercarriages is essential for ensuring the longevity and efficiency of agricultural equipment. Regular maintenance can significantly reduce downtime and repair costs. A well-maintained undercarriage enhances performance and minimizes soil disruption, which is crucial for environmental conservation. The emphasis on maintenance relates both to operational effectiveness and overall equipment health. Key maintenance practices include inspections, lubrication, and proper adjustments, all of which contribute to the longevity of these systems.
Regular Inspection Protocols
Visual inspections
Visual inspections are a primary component of routine maintenance for track undercarriages. This method involves a simple yet effective process of checking for visible signs of wear, damage, or misalignment. The primary characteristic of visual inspections is their immediacy; they allow operators to quickly assess the condition of track systems without specialized tools. This approach is beneficial due to its accessibilityβit requires minimal training and can often be performed in-field.
One unique feature of visual inspections is their ability to identify issues early on, preventing potential failures before they escalate. The advantages include quick identification of surface-level problems, such as cracks or misalignments. However, its limitations include the inability to detect hidden problems that may require more sophisticated measurement techniques.
Wear measurements
Wear measurements are an essential aspect of assessing the condition of track undercarriages. They involve quantifying material loss on components such as track links and rollers. The key characteristic of wear measurements is that they provide a more precise and quantitative analysis than visual inspections alone. This detailed assessment can inform maintenance decisions more accurately, indicating when components need repair or replacement.
The unique feature of wear measurements is their reliance on specific tools and gauges, ensuring that measurements are objective and repeatable. The advantage here is that they allow for the monitoring of wear patterns over time, enabling proactive maintenance strategies. However, implementing wear measurements requires more investment in tools and training, which might be a drawback for some operators.
Lubrication Practices
Lubrication is a critical maintenance function that directly impacts the longevity and efficiency of track undercarriages. Proper lubrication minimizes friction between moving parts, reducing wear and preventing system failures. The application of the correct type and amount of lubricant must be tailored to the environmental conditions and specifications of the equipment.
Lubrication practices should be scheduled based on the operational intensity and conditions. Regularly lubricated components ensure smooth operation and enhance the overall performance of the equipment. However, negligence in these practices can lead to excessive wear, overheating, and eventually structural failure of critical components.
Track Tensioning Techniques
Track tensioning is another vital maintenance aspect. Proper tension ensures optimal contact between the track and the surface being worked on. This practice affects traction and stability of the agricultural machine, directly influencing productivity. The tension should be checked regularly and adjusted according to the manufacturer's specifications.
Incorrect tension can lead to various issues like uneven wear on the tracks and rollers or loss of traction. Therefore, mastering the correct tensioning techniques can prolong the life of the undercarriage and enhance operational efficiency. Operators should familiarize themselves with specific adjustment protocols as outlined in equipment manuals.
Common Repairs and Adjustments
Finally, being ready to perform common repairs and adjustments is crucial for maintaining track undercarriages. Operators should be trained in identifying when a component is no longer functioning optimally and needs repair. This includes tasks like replacing worn track links, adjusting misaligned rollers, and repairing damaged idlers.
Being proactive in these repairs prevents more significant problems and costly downtime. Keeping a checklist of common repairs helps streamline routine maintenance sessions, ensuring that undercarriage systems remain in peak condition. Regular training and reference to equipment manuals will enhance the effectiveness of these maintenance practices.
Technological Advancements in Track Undercarriage Systems
Technological advancements have significantly transformed track undercarriage systems in agricultural machinery. This transformation is essential as it addresses the increasing demands for efficiency and reliability in agricultural operations. Improved technology not only enhances performance but also impacts maintenance practices and operational costs.
Smart Monitoring Systems
Smart monitoring systems represent a notable leap in track undercarriage maintenance. These systems employ sensors and data analytics to provide real-time feedback on the condition of the undercarriage. For instance, monitoring systems can track wear rates and alert users about components that require attention.
- Benefits of Smart Monitoring Systems:
- Predictive Maintenance: By monitoring trends, these systems help predict failures before they occur, reducing unexpected downtime.
- Operational Efficiency: Operators benefit from the capacity to optimize performance parameters based on real-time data.
- Cost Reduction: Timely alerts for maintenance can save costs associated with repairs and extend the lifespan of equipment.
Material Innovations
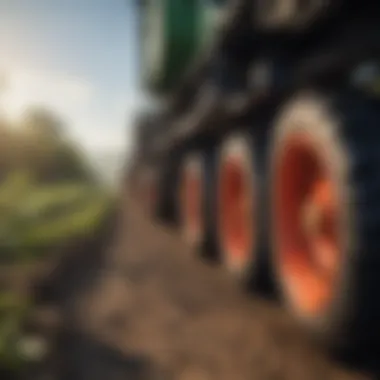
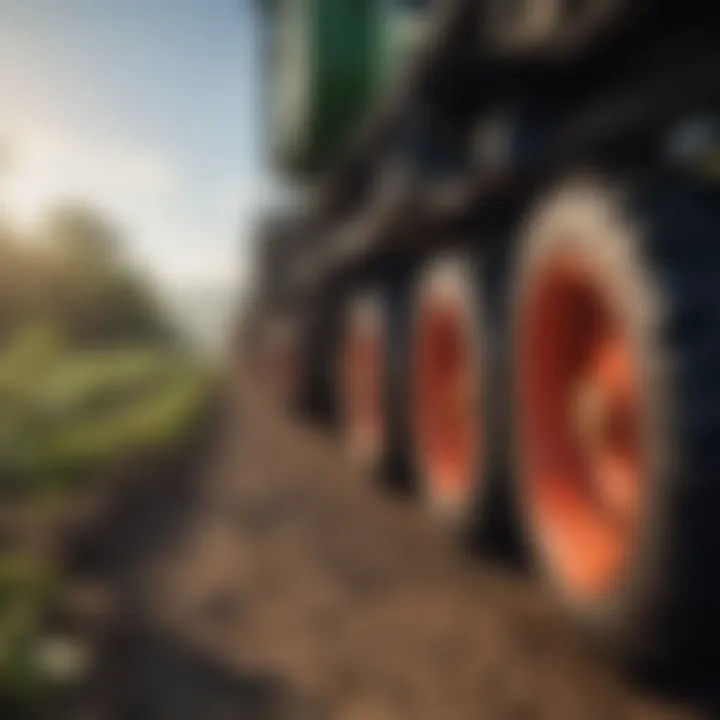
Material innovations are also critical in enhancing the durability and performance of track undercarriages. Advancements in materials used in construction allow for stronger, lighter, and more resilient components. For example, the use of advanced synthetic compounds for rubber tracks increases their resistance to wear, while high-grade steel alloys improve the strength of steel tracks.
- Considerations in Material Innovations:
- Weight vs. Strength: New materials can provide better strength without adding excess weight, which is beneficial for fuel efficiency.
- Resistance to Environmental Factors: Some materials are designed to withstand harsh environmental conditions, reducing maintenance needs and increasing reliability.
"Advancements in technology enable the agricultural sector to meet its evolving challenges with increased precision and efficiency."
Keeping abreast of these technological advancements is important for farmers and agricultural enthusiasts. Understanding how smart monitoring and material innovations impact undercarriage performance allows for more informed decisions concerning equipment maintenance and overall agricultural productivity.
Economic Implications of Track Maintenance
Understanding the economic implications of track maintenance is pivotal for agricultural operators. The costs associated with maintaining track undercarriage systems can directly influence the overall profitability of farming operations. Hence, conducting a thorough cost-benefit analysis becomes essential. This section will explore how maintenance practices can lead to significant savings while ensuring operational efficiency.
Cost-Benefit Analysis of Maintenance vs. Replacement
When equipment components incur wear and tear, decision-makers are often faced with the dilemma of whether to maintain or replace them. The initial impulse might lean towards replacement because it seems simpler. However, here are key considerations:
- Maintenance Costs: Regular maintenance is generally less expensive than purchasing new undercarriage parts. Operators should assess the routine expenses associated with servicing versus the potential costs of downtime caused by failure.
- Longevity of Parts: Well-maintained components can provide extended service life. Conversely, a hasty replacement might not always guarantee superior quality or functionality.
- Productivity Impacts: Downtime due to failure can disrupt operations, affecting yield and revenue. Regular maintenance reduces the risk of sudden breakdowns, ensuring that machinery performs optimally when needed.
- Replacement Costs: New equipment can initially appear more attractive. Nonetheless, the financial strain comes not only from the purchase price but also from the depreciation associated with new parts, which can swiftly impact the bottom line.
- Market Resale Value: Maintaining your equipment can also help preserve its resale value. Well-maintained machinery tends to fetch a better price in the market, which can offset the initial maintenance costs over time.
In summary, while it may be tempting to replace equipment at the first sign of trouble, a comprehensive analysis often reveals that routine maintenance is far more economically viable. Operators should stay vigilant and proactive with their track undercarriage systems.
"Investing in maintenance rather than replacement can yield higher returns in the long run, drastically improving operational efficiency and profitability."
By considering the economic implications of track maintenance, agricultural operators can make more informed decisions, maximizing returns and sustaining their farming endeavors.
Environmental Considerations in Track Operations
Understanding environmental considerations in track operations is vital for sustainable agricultural practices. With the growing emphasis on eco-friendly farming, the impact of heavy machinery on soil health cannot be overlooked. Proper management of track undercarriages plays a pivotal role in creating an environmentally responsible approach to agriculture. As farmers and operators become more aware of their role in environmental stewardship, the need for efficient track systems is paramount.
Minimizing soil compaction is a key focus within environmental considerations. Soil compaction occurs when soil particles are compressed, leading to reduced pore space and restricting air and water movement. High soil density can negatively affect root growth and reduce crop yields. Given that track undercarriages exert significant weight on the soil, the design and maintenance of these systems must prioritize minimizing their impact.
Minimizing Soil Compaction
There are several strategies that operators can implement to minimize soil compaction caused by track undercarriage systems. These include:
- Using Larger Surface Area Tracks: Wider tracks distribute weight over a larger area, reducing pressure on any specific point of soil. This design significantly lessens the risk of compaction compared to narrower tracks.
- Operating During Optimal Conditions: Conducting fieldwork when the soil is dry or during drier seasons can prevent further compaction. Premature tasks during wet conditions can lead to severe damage to the soil structure.
- Regular Maintenance: Keeping the undercarriage well-maintained ensures that it operates effectively, minimizing unnecessary weight distribution that could lead to compaction issues.
"The use of wider tracks and proper maintenance are critical in reducing soil health impacts."
- Adjusting Tension Appropriately: Ensuring the right tension on tracks can also aid in minimizing ground pressure. Too much tension may lead to increased soil compaction.
- Employing Crop Rotation and Cover Crops: Implementing these methods can enhance soil structure and promote its ability to resist compaction, thereby working in tandem with improved undercarriage designs.
Incorporating these approaches enhances not only the efficiency of agricultural operations but also sustains the underlying ecosystem. By adopting practices that consider environmental factors, farmers can protect soil health while maximizing equipment performance. This balance can lead to long-term productivity and sustainability in farming.
Case Studies and Practical Applications
Case studies and practical applications provide valuable insights into the real-world implications of track undercarriages. They showcase how theoretical concepts translate into operational realities for farmers and operators. By analyzing these cases, it becomes easier to identify best practices and common pitfalls. Moreover, such studies highlight the significance of ongoing maintenance and attention to detail in the field.
In the agricultural context, the effectiveness of a track undercarriage can vary significantly based on specific conditions and practices. These case studies emphasize the need for adaptable strategies tailored to individual circumstances. By examining different situations and outcomes, agricultural professionals can make informed decisions that enhance performance and longevity of their machines.
Real-World Examples of Track Undercarriage Failures
Observing past failures can offer numerous lessons. For example, a well-documented case involved a large agricultural operation that faced repeated track failures due to improper tensioning. Agitated by the uneven load distribution, the tracks wore out prematurely. The operator initially underestimated the impact of track tension on stability and traction. As a consequence, this miscalculation led to higher maintenance costs and reduced operational efficiency.
Additionally, another case highlights soil compaction issues arising from inadequate maintenance. An operator using a steel track system in a wet field experienced significant compaction. This caused damage to the soil structure, leading to decreased crop yield. The key takeaway from these failures stresses the importance of regular maintenance practices. It reinforces the message that neglecting basic protocols can result in significant operational setbacks.
Best Practices from Successful Operators
Learning from successful operators can illuminate effective strategies and innovative practices. One such operator implemented rigorous inspection schedules that included daily visual checks and weekly wear measurements. This proactive approach ensured that minor issues were identified before they escalated into significant problems.
Furthermore, successful operators employ systematic lubrication practices, ensuring all moving parts are adequately serviced. For instance, regular applications of high-quality lubricant reduced wear on rollers and idlers, thereby extending their lifespan.
In addition to maintenance, these operators emphasize the importance of training and knowledge-sharing among their staff. Regular workshops covering techniques for track tensioning and inspections foster a culture of vigilance. This education is vital for sustaining machine performance over time.
To summarize, integrating case studies and practical applications into agricultural practices provides lessons in efficiency. Understanding failures helps operators refine their strategies, while studying best practices motivates continual improvement. By embracing these insights, professionals in the field can optimize performance and extend the service life of track undercarriages.
Closure
The conclusion serves as a pivotal component of this article by emphasizing the significance of track undercarriages in agricultural equipment maintenance. Understanding the insights shared throughout the text crystallizes the inherent value of proper maintenance practices, technological adaptations, and the necessity for regular inspections.
In particular, it is critical to recognize the multifaceted benefits derived from effective track undercarriage management. The implications extend beyond mere equipment lifespan, significantly impacting operational efficiency, fuel consumption, and overall productivity on the field. Proper insight into the components, performance factors, and innovative advancements promises not only to enhance functionality but to safeguard investments.
The examination of case studies and real-world applications showcased the tangible results of thorough maintenance regimes. By following best practices, operators can mitigate the risks of breakdowns and soil degradation, ultimately preserving both equipment and the environment. It is also necessary to consider economic implications; the calculated investment in maintenance is often considerably lesser compared to the costs incurred from equipment failure.
Summarizing Key Points
- Essence of Track Undercarriage: The foundation of performance for agricultural machinery.
- Regular Maintenance: Critical for longevity and functionality; emphasizes the need for inspections.
- Technological Advancements: Innovative tools and materials enhance operational capabilities.
- Economic Benefits: A well-maintained undercarriage reduces costs associated with repairs and replacements.
- Environmental Responsibility: Proper management helps prevent soil compaction and preserves land quality.
Ultimately, recognizing the nuances of track undercarriage systems allows for improved decision-making, efficiency, and sustainability in agricultural practices.