Essential Guide to Mini Excavator Repair Services
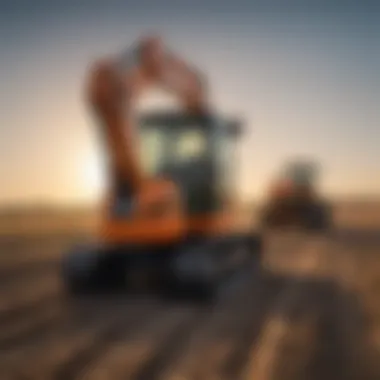
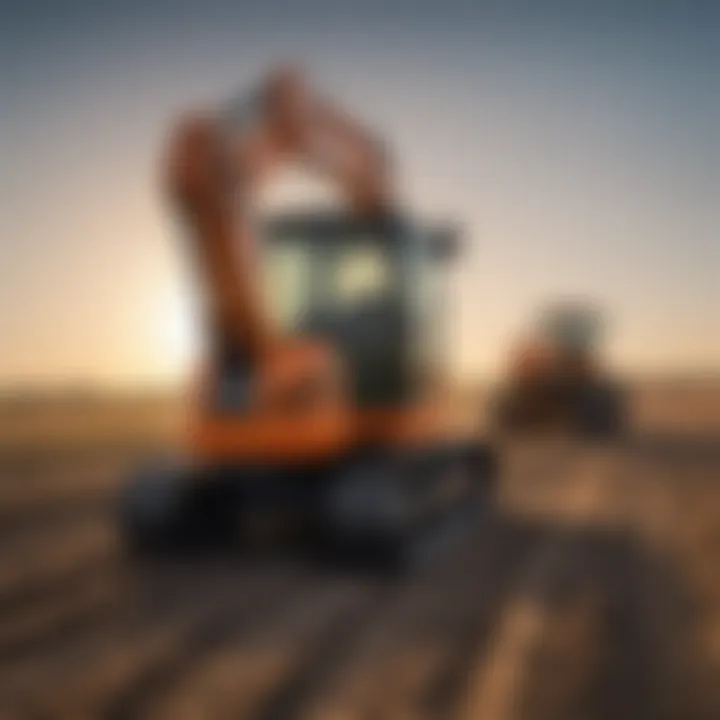
Intro
Mini excavators play a crucial role in modern agriculture. Their versatility allows farmers to perform a variety of tasks, from digging ditches to moving materials. However, like any machinery, mini excavators are prone to wear and tear. Understanding the repair services available for these machines is essential for maintaining their function and extending their lifespan.
Accessing the right mini excavator repair services can be challenging. Farmers must navigate through several factors when choosing a service provider. This guide aims to provide insight into the key concepts, recent innovations, and practical techniques associated with mini excavator repairs, specifically tailored for agricultural purposes. Through this examination, we intend to equip readers with knowledge critical for enhancing the performance of their machinery and ensuring efficient agricultural operations.
Understanding Mini Excavator Repair
The repair of mini excavators is crucial. These machines play a significant role in agriculture, enhancing productivity over traditional methods. Understanding the repair processes needed for these machines can lead to better maintenance and longer lifespans. With knowledge of repair specifics, operators can prevent small issues from escalating into costly problems. This proactive approach saves time and enhances operational efficiency.
The Role of Mini Excavators in Agriculture
Mini excavators are essential for many agricultural activities. They are used for tasks such as digging, grading, and lifting. Their compact size allows them to operate in tight spaces, which is common in farming environments. This versatility makes them valuable for tasks ranging from planting to irrigation.
In addition to flexibility, mini excavators are often more fuel-efficient than larger equipment. This efficiency can significantly lower operational costs. Farmers can use them for both heavy-duty tasks and delicate maneuvers, making them a favorite for diverse applications.
Common Repair Needs
Owning a mini excavator comes with its share of repair needs. Some common repair issues often include:
- Hydraulic leaks: These are prevalent and can lead to performance drops if not identified quickly.
- Electrical system failures: Issues with wiring and connections can disrupt machine operation.
- Wear and tear: Components such as tracks and buckets can wear out over time and require replacement or repairs.
Regular maintenance helps identify these issues early. By recognizing signs of wear or failures, operators can address them before they worsen, reducing downtime and repair costs.
Identifying Local Mini Excavator Repair Services
Locating reliable mini excavator repair services is essential for maintaining the operational efficiency of agricultural equipment. Understanding how to identify nearby repair options can help minimize downtime in the field. This section explores the importance of proximity and guides you in researching local services that cater specifically to mini excavators used in agriculture.
Importance of Proximity
When seeking repair services for mini excavators, proximity to your location has several advantages. First, it reduces transportation costs and time. If a mini excavator requires immediate attention, a nearby repair service can provide faster response times and minimize delays in resuming projects. Additionally, local repair shops may have a more keen understanding of the specific challenges faced in agricultural settings in your area. This can translate to more tailored service and parts usage appropriate for local conditions.
Local services often have established relationships with parts suppliers, leading to quicker access to essential components. Furthermore, proximity promotes a relationship with the service provider, facilitating better communication and ongoing support.
Researching Local Options
Once you recognize the importance of location, the next step involves researching available options. Start by using online search engines and directories to compile a list of local repair services. Keywords such as "mini excavator repair near me" or "mini excavator service in [your region]" can yield fruitful results. Websites like Google Maps can assist in visualizing distances and reading reviews from other customers.
Another reliable source for finding local services includes forums or groups on platforms such as Reddit or Facebook. In these spaces, you can ask for recommendations from fellow agricultural workers or enthusiasts who have first-hand experience with service providers. Engage in discussions to gather insights regarding service quality and typical repair times.
After obtaining a list of potential service providers, assess their websites and social media pages. Look for any specific information they provide about their offerings, specialties, and expertise with mini excavators. Ensuring that they have the right experience in working with your specific brand and model is critical to achieving effective repairs.
To summarize, identifying repair services in close proximity can enhance your operations significantly by reducing response times and ensuring that your mini excavator receives appropriate care tailored to local needs.
Evaluating Repair Services
When selecting a mini excavator repair service, careful evaluation is essential. This process not only aids in finding a qualified provider but also affects the overall operating efficiency of your equipment. A well-chosen service can prolong the life of your mini excavator and ensure it operates at optimal performance. Understanding what to assess and how to consider various factors in your decision can make a significant difference.
Assessing Experience and Qualifications
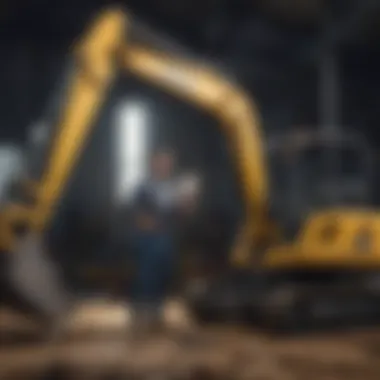
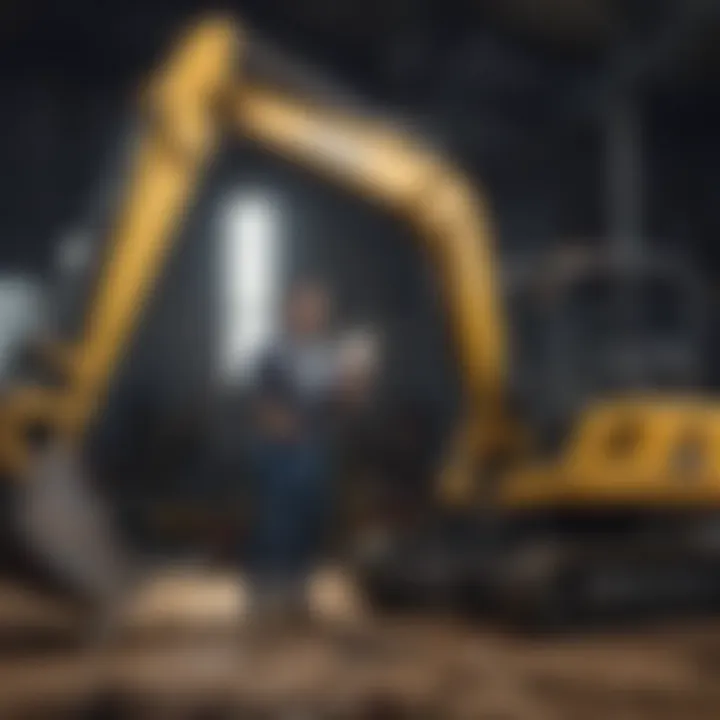
Experience and qualifications of repair technicians are critical factors in evaluating repair services. A service provider with a long history in the industry likely has encountered diverse issues, developing a solid problem-solving methodology. Consider looking for technicians who have specific training in mini excavator repairs. Certifications from recognized organizations can also provide reassurance of their knowledge and skills.
Furthermore, inquire about the technician's familiarity with different brands like Kubota or Caterpillar. Each brand may have unique operational characteristics and problems requiring specialized knowledge in repair methods. This expertise can accelerate diagnosis and repair, ultimately minimizing downtime.
Checking Reviews and References
Before finalizing a repair service, checking reviews and references is a valuable step. Online platforms such as Google and Yelp can offer insights from previous customers. Reviews usually highlight both positive and negative experiences, giving a balanced view of service quality. Pay special attention to feedback on turnaround times and customer service as these aspects significantly affect your satisfaction.
Additionally, ask the repair service for references. Speaking directly with past clients can yield personal accounts regarding the quality of work, reliability, and whether the service met expectations. References will provide an up-close view of what you might expect.
Warranty and Service Guarantees
Insurance on a repair service can be a safeguard against future problems. When evaluating services, inquire about warranties or service guarantees. A provider that offers a warranty on repairs demonstrates confidence in their workmanship and provides peace of mind for you as the client. Such warranties can also indicate that the service commits to stand behind their work, mitigating the risk of incurring further costs due to repeated issues.
"A proper warranty not only guarantees the quality of the repair but also shows the company's commitment to customer satisfaction."
Having a firm understanding of the options and terms of these warranties aids in making a reliable choice. Overall, evaluating these aspects of repair services significantly influences your equipment's longevity and performance.
Common Mini Excavator Issues
Mini excavators are versatile machines, widely used in agriculture for various tasks. However, like all machinery, they are not immune to issues. Understanding common mini excavator problems is crucial for maintaining efficiency and longevity in agricultural operations. Identifying these problems early can save time and cost. Knowing the types of challenges faced can guide preventive measures and facilitate effective repairs.
Hydraulic Problems
Hydraulic systems are at the core of mini excavators. They allow for smooth operation of the arm, bucket, and tracks. However, various issues can arise in this system. Common hydraulic problems include leaks, overheating, and sluggish movements. Leaks often result from worn-out seals or damaged hoses. They can cause a significant loss of hydraulic fluid, leading to reduced performance.
Overheating occurs due to blocked filters or low fluid levels, which can lead to severe damage if not addressed. Identifying problems promptly can help avoid costly repairs. Regular checks of hydraulic fluid levels and condition are essential practices.
Electrical Failures
Electrical issues also pose significant challenges for mini excavators. These can range from faulty wiring to malfunctioning sensors. Problems often manifest in starting failures or erratic behavior of controls. Corroded connections may hinder electrical flow, causing unreliable operation. Such failures can disrupt work schedules, leading to downtime.
A proactive approach includes inspecting wiring and electrical components frequently. Ensuring protective coverings are intact helps prevent moisture intrusion. Regular maintenance on the battery is essential, too, as it powers most electrical aspects of the mini excavator.
Mechanical Malfunctions
Mechanical malfunctions encompass a variety of physical faults within the mini excavator. Common issues include engine troubles, track issues, and problems with the bucket. Engine problems can arise from poor fuel quality or inadequate lubrication. Such issues can drastically affect overall performance and efficiency.
Track problems, such as misalignment or wear, can compromise stability and mobility. Regularly inspecting tracks can help in spotting potential concerns early. Bucket issues, whether bent or malfunctioning, can obstruct the effectiveness of digging and lifting tasks.
"Timely identification and resolution of mechanical issues is fundamental for sustaining equipment longevity."
Preventive Maintenance Practices
Preventive maintenance is crucial for the longevity and performance of mini excavators, especially in agricultural settings. In a field where machinery reliability can directly impact productivity, adhering to a preventive maintenance schedule can prevent costly breakdowns and enhance the equipment's operational efficiency. By addressing potential issues before they escalate, operators can maintain optimal performance and greatly reduce downtime during critical operations.
Regular Inspections
Conducting regular inspections of mini excavators is essential in identifying issues that may lead to more significant repairs if neglected. These inspections should include visual checks of the hydraulic systems, electrical components, and mechanical parts. Pay attention to the following aspects:
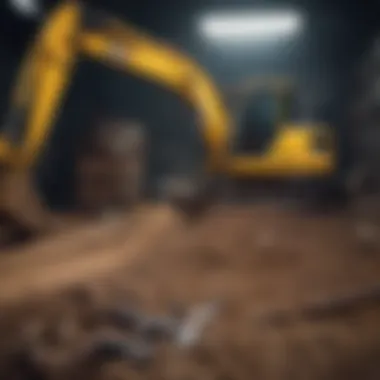
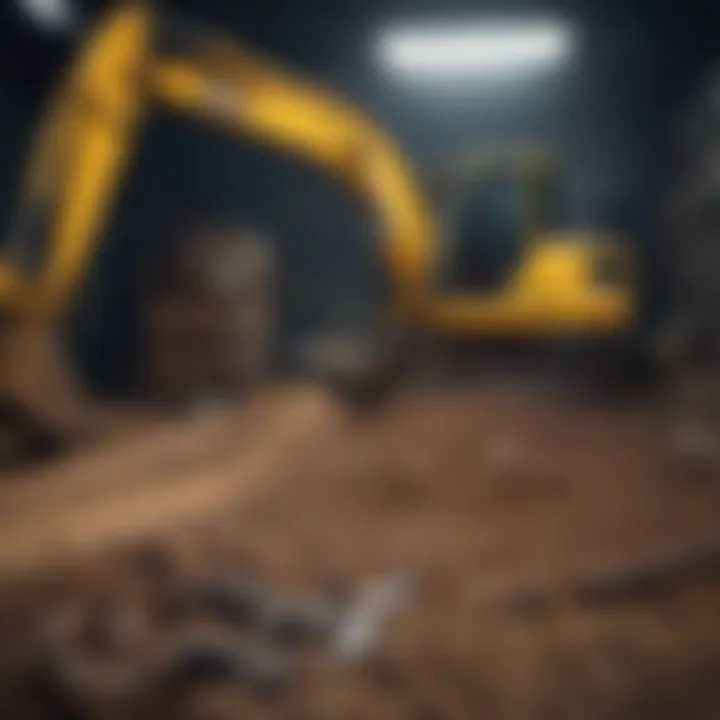
- Fluid Levels: Check hydraulic oil, coolant, and fuel levels to ensure they are within the recommended specifications.
- Leaks: Look for any signs of fluid leaks, especially around hose connections and fittings.
- Belts and Cables: Inspect belts for wear and adjust tension as needed. Also, check cables for signs of fraying or damage.
- Operational Function: Test various machine functions, such as hydraulic movements and electrical components, to confirm they operate smoothly.
Performing these inspections on a regular basis can help catch issues early, minimizing the risk of unexpected failures.
Routine Oil Changes
Routine oil changes are another pillar of effective preventive maintenance. The oil lubricates the engine and hydraulic systems, reducing friction and wear. Over time, oil can degrade, leading to decreased performance and potential damage. Consider these points:
- Frequency of Changes: Follow the manufacturerโs recommendations for oil change intervals. Regularly check the oil condition to determine if more frequent changes are needed.
- Type of Oil: Use the appropriate oil grade as specified in the excavator's manual. Incorrect oil can affect engine performance and efficiency.
- Disposal: Ensure proper disposal of used oil in accordance with local regulations. This maintains environmental standards and supports sustainable practices.
Changing oil consistently helps in maintaining engine health and performance, leading to longer equipment life.
Monitoring Performance Metrics
Monitoring performance metrics can provide valuable insights into the health and efficiency of a mini excavator. Operators should keep track of:
- Fuel Consumption: An increase in fuel consumption may indicate underlying issues, such as inefficiencies or engine problems.
- Hydraulic Pressure: Regularly monitor hydraulic pressure readings to ensure they remain within optimal ranges. Deviations can signify potential mechanical issues.
- Operating Temperatures: Keeping an eye on operating temperatures can help identify when cooling systems may need attention or if the engine is under undue stress.
By systematically evaluating performance metrics, operators can preemptively address potential crises, thus avoiding costly repairs and improving overall machine reliability.
"Regular maintenance not only keeps machinery operating efficiently but also secures a longer lifespan for equipment involved in critical agricultural work."
Implementing these preventive maintenance practices is essential for farmers seeking to maximize the efficiency and lifespan of their mini excavators. With diligent attention to maintenance, operators can ensure that their excavators perform at their best when they need them most.
Understanding Repair Costs
Understanding the costs associated with mini excavator repairs is essential for farmers and agricultural enthusiasts. A clear grasp of these costs can lead to more informed decisions regarding maintenance and repair strategies. Knowing what to expect financially allows individuals to budget accordingly and avoid unexpected expenses that can disrupt agricultural operations.
Factors Influencing Costs
Several factors can influence the cost of mini excavator repairs. Understanding these can help in anticipating expenses. Here are some key elements to consider:
- Type of Repair: Basic services like oil changes will cost less than major repairs on hydraulic systems or engines.
- Labor Rates: Different repair shops have varying labor rates. Areas with high demand may see elevated costs.
- Parts Availability: If certain parts are hard to find, it may increase the cost. Original parts tend to be more expensive than aftermarket alternatives.
- Service Shop Reputation: Established shops may charge more for their expertise and reliability.
- Equipment Condition: Older machines prone to frequent problems might lead to more significant overall costs.
"Understanding these factors helps in planning and can significantly reduce financial strain during repairs."
Estimating Repair Expenses
Estimating repair expenses is not always straightforward but is crucial for farmers. Here are effective methods to estimate costs:
- Get Quotes: Contact local services for estimates based on your specific needs. Comparing multiple quotes will give a clearer picture.
- Review Common Prices: Familiarize yourself with average costs for common repairs in the industry. Online forums and sites like Reddit can provide insights from other users.
- Consult with Mechanics: Experienced mechanics can advise on what to expect regarding costs based on past projects.
- Consider Maintenance History: A machine that has been well-maintained may need fewer repairs, translating to lower costs over time.
Being proactive in understanding repair costs allows farmers to safeguard their operations. It can help in minimizing unforeseen expenditures and maintaining optimal performance of mini excavators.
The Impact of Delayed Repairs
The significance of understanding the impact of delayed repairs cannot be overstated when it comes to the operational efficacy of mini excavators, especially in agriculture. Time is often of the essence in farming operations where productivity directly relates to equipment reliability. Ignoring minor issues can lead to compounded problems, potentially hindering performance and escalating costs long-term. Farmers must recognize that timely repairs conserve the functionality and integrity of machinery, ensuring it operates at peak efficiency while minimizing unexpected downtime.
Effects on Performance and Efficiency
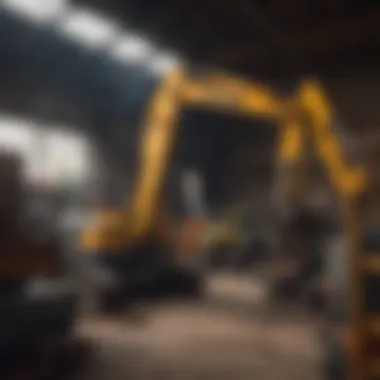
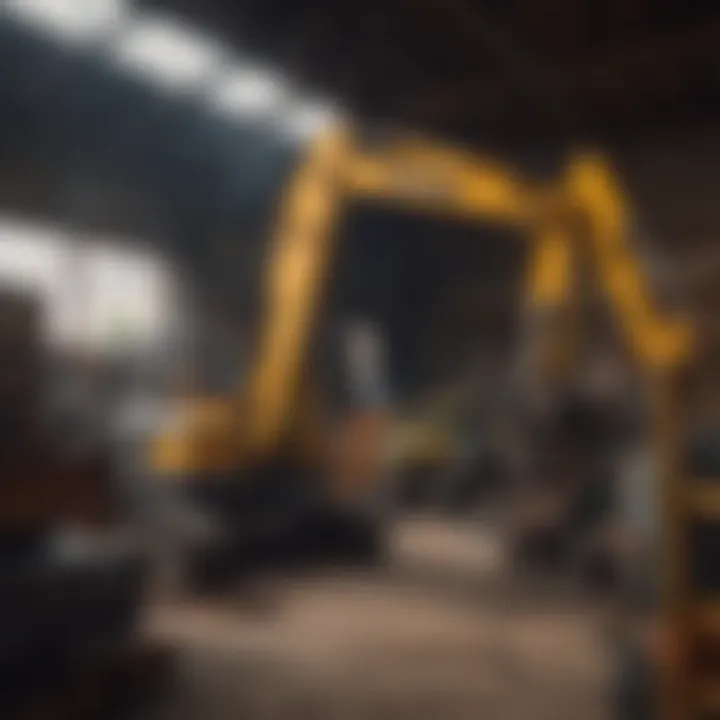
Delayed repairs can severely diminish the performance of mini excavators. When issues are not addressed promptly, the equipment may operate below its intended capacity. For instance, hydraulic problems can result in sluggish response times, affecting overall digging power and speed. This inefficiency translates into longer project times, which incurs additional labor costs. Moreover, when machinery operates ineffectively, it can contribute to increased fuel consumption, further straining the operational budget.
Preventing small issues from becoming larger, complex faults is crucial. Addressing concerns such as leaking fluids or worn components immediately can lead to a smoother and more efficient operation. Keeping equipment at optimal performance not only enhances the efficacy of specific jobs but also extends the lifespan of the machinery, leading to better return on investment.
Long-term Damage Risks
The risks associated with delaying repairs extend beyond immediate inefficiencies. Over time, ignoring small repairs may lead to significant damage that could have been averted. For example, a small hydraulic leak, if not addressed, can result in catastrophic hydraulic system failure. Such failures necessitate expensive replacements and could leave the machine out of service for extended periods.
In the long run, the cumulative effects of postponed repairs can lead to permanent damage to the machinery. Structural failures, engine damage, and transmission issues are just a few of the potential pitfalls. Farmers should consider the long-term implications of neglecting repairs. Planning for regular assessments and performing timely maintenance not only safeguards equipment but also conserves resources. Delayed repairs ultimately result in not just higher costs, but also a detrimental impact on productivity and operational continuity.
After-Service Considerations
After addressing repairs on a mini excavator, it is crucial to consider the post-service aspects. The right after-service strategies can significantly influence the equipment's future functionality. This section discusses key elements and advantages of post-repair follow-ups and ongoing maintenance strategies. Both components focus on prolonging the life of mini excavators and ensuring they continue to operate efficiently.
Post-Repair Follow-ups
Following repairs, implementing a structured follow-up process is essential. These follow-ups can verify that the repairs were effective and are performing as expected. Here are some important aspects to consider:
- Scheduled Check-ins: Arrange follow-up dates with the repair service to ensure the equipment is operating without issues. This structured approach aids in identifying any possible lingering problems.
- Performance Monitoring: Keep track of how the mini excavator behaves after repairs. Noting any changes in performance helps in deciding if the repairs have succeeded.
- Documentation: Maintain records of the repairs and any observations noted during the follow-ups. Documentation is valuable for future reference, enabling both the operator and the repair technicians to review repair history fast.
Implementing a follow-up system enhances transparency and communication between the equipment owner and the service providers, fostering trust and reliability.
Ongoing Maintenance Strategies
Engaging in regular maintenance is vital for keeping mini excavators in peak condition. Ongoing maintenance strategies go beyond post-repair actions and embed a culture of care and inspection. Key strategies include:
- Fluid Checks and Changes: Regularly inspect oil and other vital fluids for cleanliness and appropriate levels. Regular fluid changes prevent mechanical components from experiencing unnecessary wear.
- Component Inspection: Routinely examine parts such as tracks, undercarriage, and the hydraulic system for wear or signs of degradation. Catching small issues early can prevent larger, more expensive repairs later.
- Operator Training: Ensure operators are well-trained in using the equipment efficiently. Understanding weight limits and control mechanisms can minimize wear and extend the machine's lifespan.
- Log Maintenance Activities: Keep a log of all maintenance tasks accomplished. This assists not only in tracking when the next maintenance is due but also provides insights into patterns or recurring issues that may arise.
Taking proactive steps strengthens the reliability and efficiency of mini excavators while minimizing the risk of significant breakdowns that disrupt agricultural operations. Combined, these after-service considerations are essential for achieving long-term effectiveness in machinery usage.
The End and Future Perspectives
The conclusion of this guide aims to underscore the significance of understanding mini excavator repair services in the agricultural context. As discussed, effective maintenance and timely repairs are critical to maximize the functionality and durability of this essential equipment. Farmers must recognize that neglecting repairs can lead not only to inefficiencies but also to costly damages that could have been prevented.
By prioritizing ongoing maintenance strategies, operators can avoid sudden breakdowns and extend the lifespan of their equipment. This translates directly into sustained productivity and economic benefits over time. Additionally, staying informed about the latest repair techniques and technologies can improve decision-making regarding repairs and upgrades.
Sustaining Equipment Longevity
To ensure that mini excavators perform at their best, sustaining equipment longevity involves implementing a proactive maintenance approach. Regular checks should focus on key components such as hydraulic systems, tracks, and engine performance.
Essential practices for sustaining the longevity of mini excavators include:
- Scheduled Maintenance: Adhering to the manufacturerโs maintenance schedule is crucial. This often includes routine inspections and servicing.
- Immediate Repairs: Addressing small issues promptly can prevent them from escalating into more significant problems.
- Proper Lubrication: Ensuring that all moving parts are adequately lubricated reduces wear and tear on the components.
- Environmental Considerations: Keeping the equipment protected from harsh weather can also enhance its lifespan.
Efforts in these areas can lead to a smoother operation of mini excavators, ultimately saving time and money in the long run.
Emphasizing Continuous Learning
In a rapidly evolving industry, continuous learning becomes vital for those involved with mini excavators. It is important for operators, managers, and repair technicians to keep up-to-date with advancements in technology and repair techniques.
Key aspects of continuous learning include:
- Training Programs: Engaging in workshops and training programs can enhance skills related to mini excavator operation and maintenance.
- Online Resources: Utilizing platforms like Reddit and Facebook to gather insights from communities and experts is beneficial.
- Professional Certification: Pursuing certifications from recognized organizations adds credibility and expertise in handling repairs and maintenance.
Continuous learning not only enhances personal skill sets but also contributes positively to overall operational efficiency. Being informed of existing and upcoming technology makes it easier to adapt and implement better practices in mini excavator use and repair.