Mastering Stick Welding: Techniques and Tips
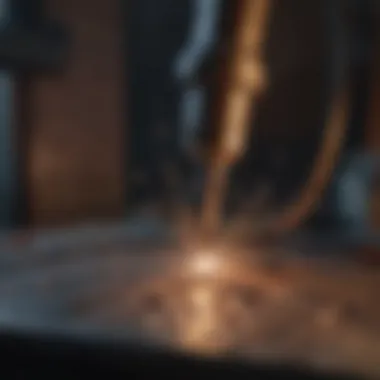
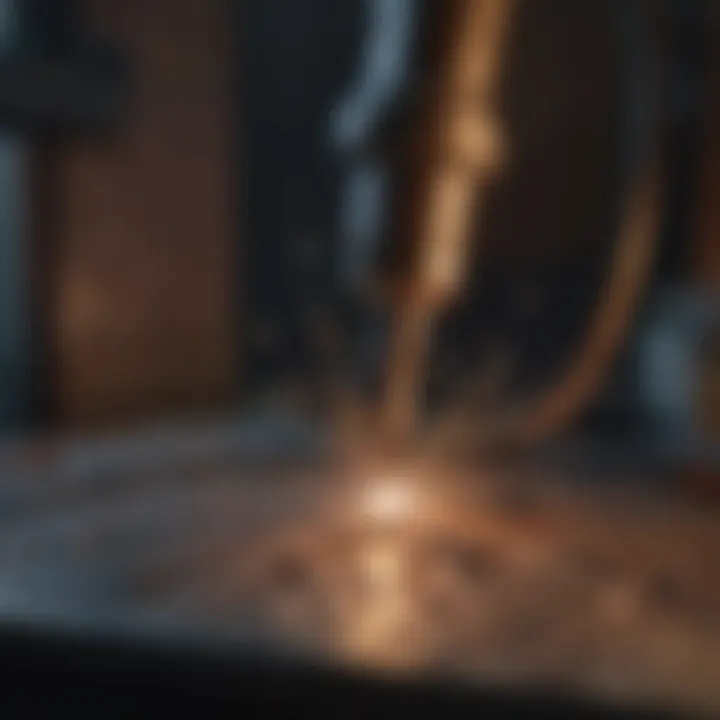
Intro
Stick welding is a fundamental skill in the field of welding, commonly used by professionals and hobbyists alike. Whether in industrial settings or at home, mastering stick welding brings efficiency and effectiveness to both steel and iron projects. Learning how to perform this type of welding not only enhances your craftsmanship but also opens doors to various applications, particularly for agriculture farmers involved in repair and maintenance work on machinery or structures.
In this guide, we will delve into the essential concepts, techniques, and safety practices that are crucial for anyone looking to learn stick welding. Understanding these elements is vital for secure and competent welding. From acquiring basic definitions and grasping historical context to exploring recent trends and practical applications, this article aims to serve as a thorough resource for both novices and experienced welders.
As we proceed, we will emphasize key terminology related to stick welding, ensuring readers have a firm grasp of the language, which is essential for effective communication and troubleshooting. Furthermore, recent technological advancements will be explored to highlight the evolving landscape of welding methods.
Equipped with the knowledge from this article, learners should feel confident in applying their skills and adapting them to different contexts. Let's begin by examining the fundamental concepts and terminology that form the backbone of stick welding.
Prelude to Stick Welding
Stick welding, also known as shielded metal arc welding (SMAW), is a fundamental technique in the field of welding. This method plays a crucial role in both industrial and domestic applications. Understanding this welded process allows agricultural farmers and enthusiasts to create strong, lasting bonds between metals, which is essential for equipment repairs and construction projects. In this section, we will define stick welding and provide insight into its historical context, which will help clarify its significance in modern practices.
Definition and Overview
Stick welding involves the use of a consumable electrode coated in flux. When an electric current passes through the electrode, it creates an arc that melts the electrode and base metal. The flux coating disintegrates, generating a shielding gas that protects the weld pool from contaminants such as oxygen. This method is versatile and can be used on various metals, including steel, cast iron, and certain alloys.
One of the key benefits of stick welding is its adaptability. It can be performed in various positions, making it suitable for a wide range of applications. Moreover, stick welding does not require expensive equipment or complicated setups, which makes it accessible for both professionals and hobbyists. Farmers, for instance, may find stick welding particularly useful for maintaining agricultural machinery, making it a valuable skill in the farming community.
Historical Context
Stick welding originated in the early 20th century and rapidly gained traction during World War II. As the demand for reliable and durable welding processes increased, this technique became preferred for its simplicity and effectiveness. Initially, stick welding was primarily used for large-scale projects in shipbuilding and construction. However, over the years, it has evolved into a popular choice in various sectors, including agriculture, automotive, and manufacturing.
Today, advancements in technology have further enhanced stick welding's utility. The development of improved electrode designs and welding machines has led to greater efficiency and precision. Understanding the historical context of stick welding helps appreciate its ongoing relevance and adaptability, particularly in agriculture where maintenance and repairs are critical. This makes a solid foundation for learning about the technique itself as we delve deeper into the principles and practices of stick welding.
Principles of Stick Welding
Understanding the principles of stick welding is crucial for anyone interested in mastering this technique. Knowledge of these principles allows welders to produce strong, reliable joints, while also optimizing the welding process itself. It contributes not only to the quality of the weld but also to the efficiency of the operation. This section elucidates the core components of stick welding, including how the welding arc works, the types of electrodes used, and the metal transfer mechanisms involved in creating a weld.
The Welding Arc
The welding arc is the core of stick welding. It is generated when the electrode touches the base metal and then is withdrawn slightly, creating a gap. This gap forms a high temperature environment due to the high electric current passing through the air, resulting in molten metal. The temperature of the arc can exceed 3,000 degrees Celsius, which is sufficient to melt most metals commonly in use.
The arc stability and its characteristics vary based on several factors like the type of electrode and the welding machine settings. As such, understanding how to control the arc can lead to better results. A stable arc produces a consistent weld bead, while an unstable one could cause irregularities, including porosity or undercutting. It is vital for stick welders to learn how to maintain this arc appropriately.
Electrode Types and Their Functions
Electrodes play a pivotal role in stick welding. They not only provide the filler material but also affect the quality of the weld. Different electrodes are designed for different applications and metals. Common electrodes include E6010 and E7018, each having unique characteristics suitable for specific conditions.
- E6010: Great for deep penetration and is often used for root passes in pipe welding.
- E7018: Known for its smooth and easy operation, it provides good mechanical properties in the weld and is often used in structural steel applications.
Additionally, selecting the right type of electrode for the job can minimize issues like slag inclusion or weak welds. It is recommended to balance the electrode choice with the position and thickness of the material being welded. Understanding electrode specifications is crucial to achieving the desired properties in the final weld.
Metal Transfer Mechanisms
Metal transfer is the process by which molten metal from the electrode is deposited into the weld pool. In stick welding, this transfer primarily occurs in three methods: globular, spray, and short circuit. Each method is influenced by the current used and the arc length:
- Globular Transfer: Characterized by the formation of large metal droplets. It occurs at lower currents and is not very efficient due to increased spatter.
- Spray Transfer: Features a fine mist of metal droplets being transferred. This method requires higher current and is generally used in thicker materials.
- Short Circuit Transfer: This occurs when the electrode contacts the base metal, creating a temporary short circuit. It is ideal for thin materials and produces less spatter.
Understanding these mechanisms helps in controlling the process effectively. It shapes the final weld's characteristics and quality, impacting both strength and appearance. Learning to manipulate these transfer methods can greatly enhance the quality of the finished weld.
Equipment Required for Stick Welding
Understanding the equipment required for stick welding is essential for anyone looking to practice this skill effectively. The right tools ensure not only efficiency but also safety and precision in the welding process. A comprehensive overview of necessary equipment gives insights into the correct setup for both novices and experienced welders. Good equipment can mean the difference between a strong, durable weld and a failed application, highlighting the critical nature of these components.
Welding Machine Overview
A welding machine is the heart of the stick welding process. Selecting the appropriate one is paramount. Stick welding typically employs either a transformer-based or inverter-based machine.
- Transformer-Based Machines: These machines are robust and reliable, often suited for heavy-duty applications. They can handle high amperage and are appropriate for outdoor use.
- Inverter-Based Machines: These are lighter, portable, and often more efficient. They adjust quickly to changes in welding environments, making them ideal for varied settings.
When choosing a welding machine, ensure it matches the specifications required for the electrodes and the thickness of the material to be welded. Further, an adjustable amperage setting is vital; it allows for fine-tuning based on specific tasks.
Selecting the Right Electrode
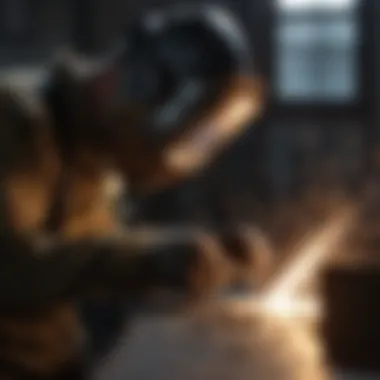
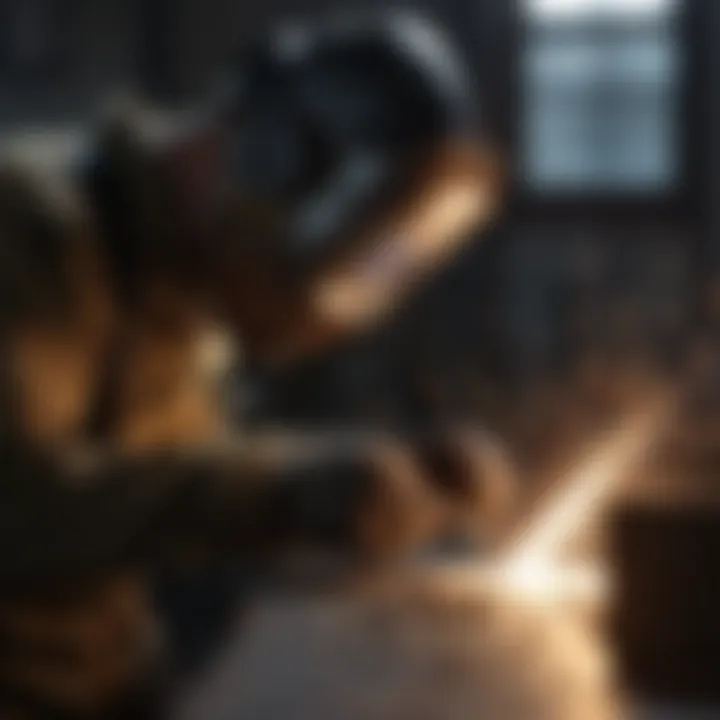
Electrodes play a critical role in the stick welding process. They provide the filler material necessary for a successful weld. Understanding electrode classifications can direct users to make the right choice:
- E6011: Known for its versatility, it can weld in any position and works on dirty or rusty metals.
- E6013: This type is suited for thin materials and offers a smoother finish.
- E7018: Best for high-strength welding, particularly in structural applications.
Selecting the right electrode depends on the materials being used and the specific requirements of the job at hand. Users should consider factors such as the required strength, penetration depth, and the type of current being utilized (AC or DC).
Protective Gear Essentials
Safety should always be the primary concern in any welding activity. Appropriate protective gear is crucial in preventing injuries or long-term health consequences. Essential gear includes:
- Welding Helmet: This protects the eyes and face from ultraviolet and infrared radiation. A helmet with a proper shade lens will help in protecting against bright arcs.
- Protective Clothing: Wear flame-resistant clothing, such as a welding jacket, to minimize the risk of burns. Cotton or leather materials are generally advisable.
- Gloves: Heavy-duty welding gloves are necessary to protect hands from heat and sparks.
In addition to personal protective equipment, ensure the work area is well ventilated. This minimizes exposure to harmful fumes generated during the welding process. Regularly inspect safety equipment to ensure they are still effective and comply with safety standards.
Remember: Proper equipment and protective gear are paramount for a successful and safe welding experience.
Safety Considerations
Understanding safety considerations in stick welding is crucial for anyone involved in this trade. Welding involves high temperatures, electric currents, and potential exposure to hazardous fumes. Neglecting safety measures not only puts oneself at risk but can also endanger others nearby. By prioritizing safety, welders can create a more efficient and secure working environment. Furthermore, adhering to safety guidelines can prevent accidents that lead to injuries or equipment damage, ultimately resulting in cost savings and a more productive workflow.
Personal Safety Gear
Welders must equip themselves with appropriate personal safety gear. This gear is essential in shielding the body from harmful incidents. The most critical components include:
- Welding Helmet: Protects the eyes and face from sparks and harmful rays. It is advisable to choose a helmet with an auto-darkening feature for convenience.
- Flame-Resistant Clothing: Wear long-sleeve shirts and pants made of flame-resistant materials. This clothing helps prevent burns from sparks or molten metal.
- Gloves: Select gloves that provide protection while maintaining dexterity. Leather gloves are a common choice, as they resist heat and abrasion.
- Steel-Toed Boots: Protect the feet from heavy objects and offer additional safety against sharp materials on the ground.
- Respiratory Protection: Depending on the workspace, a respirator may be necessary to protect against harmful fumes and gases produced during welding.
Employing the right personal safety gear allows welders to perform their tasks with greater confidence and reduces the likelihood of accidents.
Work Area Precautions
Establishing safety measures in the work area is as important as wearing protective gear. A well-organized workspace can significantly lower risks associated with stick welding. Key precautions include:
- Cleaning the Work Area: Remove flammable materials and clutter from the vicinity. An organized space reduces the risk of fire hazards and accidental trips.
- Ventilation: Ensure adequate ventilation to disperse toxic fumes. Open windows or use exhaust fans to maintain air quality.
- Emergency Equipment: Keep a fire extinguisher nearby and inspect it regularly. Familiarize yourself with its use in case of an emergency.
- Proper Storage of Materials: Store electrodes and other welding supplies in a secure area, away from moisture and heat, to prevent deterioration.
- Clear Signage: Place warning signs around the welding area to inform others of potential hazards.
By implementing these precautions, you can create a safe and conducive environment for stick welding operations.
Emergency Procedures
Finally, knowing proper emergency procedures can be vital in case of mishaps. Immediate action can mitigate damage and ensure safety. Essential procedures include:
- Immediate Response to Injuries: In case of an injury, assess the situation and administer first aid if trained. Seek medical attention if the injury seems severe.
- Fire Response: If a fire occurs, use the nearest fire extinguisher. If it spreads and becomes uncontrollable, evacuate the area and call emergency services.
- Electric Shock Protocols: If someone receives an electric shock, do not touch them until the source of the electricity is turned off. Call for medical help immediately.
- Reporting Incidents: Document any accidents or near misses to learn and improve safety protocols. Additionally, introduce corrective measures to prevent recurrence.
By having a clear plan for emergencies, welders can act swiftly, which is essential for safety on the job.
Remember: Safety is everyoneβs responsibility. Prioritize it in every welding project.
Techniques for Effective Stick Welding
Mastering stick welding requires a thorough understanding of various techniques. These techniques significantly influence the quality and integrity of welds. Knowing how to correctly position yourself, control movement, and adjust settings like amperage and voltage is essential for achieving strong and reliable welds. This section will delve into each one.
Welding Positions Explained
Welding positions play a crucial role in the outcome of any welding project. The four primary positions are flat, horizontal, vertical, and overhead. Each position requires different techniques and approaches:
- Flat Position (1G): This is the most comfortable position for welders. It allows for gravity to assist with the weld pool. Beginners should start here to build confidence and skill.
- Horizontal Position (2G): This position can be more challenging, as gravity works against you. Controlling the weld pool becomes critical. Practive with smaller passes to ensure sound joint formation.
- Vertical Position (3G): Here, the welder works either uphill or downhill. Uphill welding requires a steady hand to keep the weld pool from falling. Downhill is typically faster but can create weaker welds.
- Overhead Position (4G): This position demands a high degree of skill. Gravity complicates control of the weld pool, which can easily drip or sag. Developing proficiency in this position is key for advanced welders.
By practicing in each of these positions, welders can become versatile and adept, able to tackle various welding challenges.
Control and Movement Techniques
Effective control and movement during stick welding are paramount for consistent and high-quality results. Proper technique includes steady hand movements and the correct angle of the electrode. Here are some key points to consider:
- Electrode Angle: Keep the electrode at an angle of about 15 to 30 degrees relative to the workpiece. This angle enables smooth arc stability and effective penetration.
- Travel Speed: Maintain a consistent welding speed. Too fast can lead to insufficient penetration, while too slow can cause excess material. Regular practice will help you find the right rhythm.
- Arc Length: The arc length should be kept shortβideally about the diameter of the electrode rod. This promotes better control of the weld pool and may reduce spatter.
By mastering these techniques, a welder can ensure strong penetration and improved bead appearance, leading to stronger welds.
Setting Amperage and Voltage
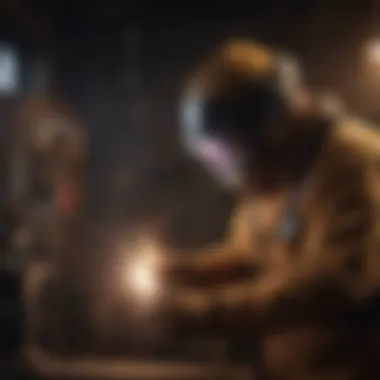
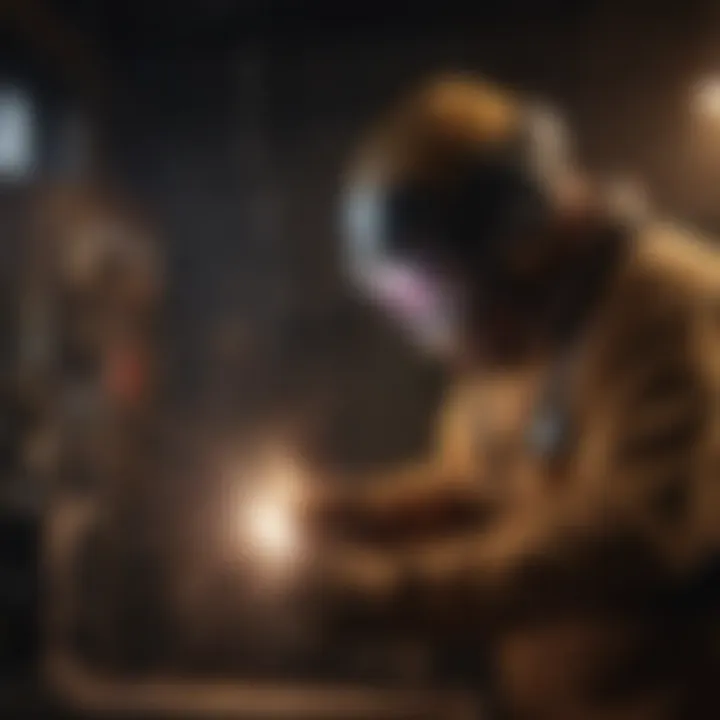
Correctly setting the amperage and voltage is vital for any successful welding project. Each electrode type and thickness of material require different settings. Here are essential factors to consider:
- Amperage Settings: Amperage needs vary based on electrode diameter, base metal thickness, and joint configuration. A general rule of thumb is to use 30 to 40 amps per millimeter of electrode diameter.
- Voltage Settings: Voltage should be adjusted according to the type of weld being performed. Higher voltage typically leads to wider beads, while lower voltage results in tighter, concentrated welds.
Always refer to the manufacturer's guidelines for specific recommendations on your equipment. Proper setting of these parameters can greatly enhance the quality of the weld and minimize defects.
Remember, practice is essential. Experiment with different settings on scrap metal before working on important projects.
Practicing Stick Welding Skills
Practicing stick welding skills is a vital component of becoming proficient in this form of welding. Mastery requires not only theoretical knowledge but also practical applications. Through consistent practice, a welder develops the muscle memory necessary for precision and accuracy. The ability to adjust techniques in real-time can significantly affect the quality of the weld.
Effective practice offers several benefits. Firstly, it enhances hand-eye coordination, which is crucial for maintaining a steady hand and controlling the welding arc. Additionally, frequent practice helps in developing a better understanding of how different settings on the welding machine influence the weld pool and metal fusing. This knowledge is essential for producing strong, defect-free welds.
If you are new to stick welding, starting with the basics is necessary before progressing to more complex techniques.
Starting with Simple Joints
When beginning the practice of stick welding, it is advisable to start with simple joints. Simple joints, such as butt, lap, and corner joints, provide a solid foundation for understanding the welding process. Practicing these joints allows a welder to gain familiarity with the welding equipment and the behavior of the electrode.
To make the most of the practice:
- Choose the appropriate electrode for the metal type.
- Ensure a clean work surface to prevent contamination.
- Adjust the amperage to suit the thickness of the material.
By starting with these basic joints, the welder can focus on mastering the fundamental skills without the complexity of more intricate designs.
Progressing to Complex Welds
Once the welder is comfortable with simple joints, they can move on to more complex welds. This progression is crucial for enhancing skill and preparing for real-world applications. Complex welds often involve multiple passes and different joint configurations like T-joints or fillet welds. These require an understanding of welding sequence and heat management.
Itβs also important to experiment with various angles and positions. This helps the welder become adaptable to different working environments. Practicing complex welds can sometimes reveal personal weaknesses, which can then be addressed through further training and dedication.
Feedback and Improvement
Regular feedback during practice plays an essential role in improvement. Whether it is from a mentor, peer, or self-assessment, constructive feedback helps identify areas for development. After each practice session, reviewing welds visually and through tests can offer insights that are valuable for growth.
- Document progress: Taking notes on each session can reveal patterns in errors or improvements over time.
- Seek professional guidance: Having a mentor can provide critical real-time feedback that may not be evident otherwise.
- Utilize video resources: Watching expert welders in action can inspire better techniques and approaches.
By focusing on these elements, a welder not only refines their skills but also builds confidence. Consistent practice in various settings will translate into improved capability, making stick welding an effective tool for both beginners and seasoned professionals.
Troubleshooting Common Issues
Trooubleshooting common issues in stick welding is critical for achieving successful and high-quality welds. Understanding how to identify problems and solutions helps welders to enhance their effectiveness and complete projects more efficiently. In this section, we will discuss key areas of concern that may arise during stick welding and strategies to rectify these issues.
Identifying Defective Welds
Recognizing defective welds is essential for any welder. Defects can arise from various factors, including incorrect machine settings, improper technique, or material contamination. Common signs of a defective weld include:
- Porosity: Small holes within the weld, usually caused by trapped gases.
- Undercutting: A groove left at the edge of the weld, which reduces the strength.
- Incomplete Fusion: Areas where the weld did not bond properly to the base material.
To identify these defects, inspect the weld visually and use a hammer to tap on the weld. A hollow sound may indicate porosity. Regular testing methods like x-ray or ultrasonic testing can also be useful in maintaining weld integrity.
Electrical Issues and Solutions
Electrical issues often pose challenges during stick welding. Problems may arise from improper settings, equipment malfunction or connections. Common electrical challenges include:
- Inconsistent Amperage: Check connections, and confirm that the settings on the welding machine match the electrode specifications.
- Arc Sticking: This happens if the electrode makes too much contact with the workpiece. To avoid this, adjust the angle and distance from the workpiece.
- Overheating: High duty cycles can cause machine shutdowns. Always allow adequate time for cooldowns to prevent damage.
Solutions will vary depending on the specific issue, but thorough equipment checks before welding can mitigate many common problems. Regular maintenance of your welding machine is crucial for optimal performance.
Addressing Material Contamination
Material contamination can lead to defects and weaken welds. Common sources of contamination include:
- Rust or Dirt: Always clean surfaces before welding to ensure good fusion.
- Oil or Grease: Degreasers or solvents should be used to remove unwanted residues.
- Moisture: Ensure that electrodes are stored in dry conditions to avoid moisture pick-up.
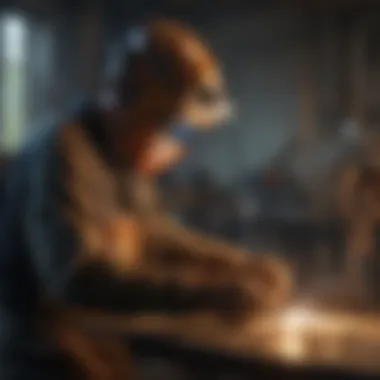
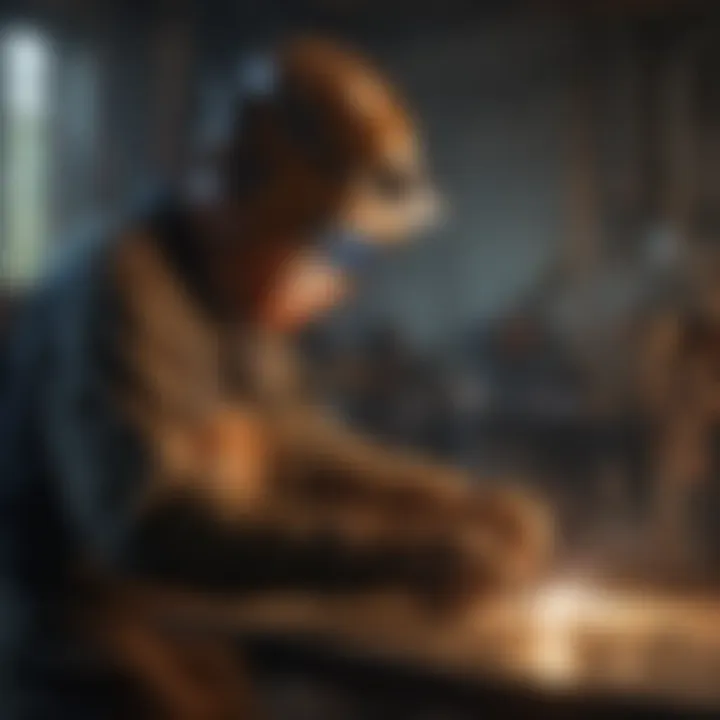
To address contamination, perform a surface inspection before welding. Use a wire brush or grinder for cleaning and follow it up with a solvent to ensure all contaminants are removed.
"Prevention is key in welding. Identifying and addressing issues early can save time and resources in the long run."
By mastering these troubleshooting skills, stick welders can significantly reduce defects and enhance the quality of their work. This knowledge empowers welders to approach their tasks with confidence, ready to tackle common challenges that may arise.
Applications of Stick Welding
Stick welding, also known as Shielded Metal Arc Welding (SMAW), is a versatile method widely used across various industries and applications. Understanding the applications of stick welding is essential for both enthusiasts and professionals. Stick welding's adaptability makes it suitable for different materials and environments, which is particularly relevant in todayβs diverse welding landscape.
The benefits of stick welding include its effectiveness in outdoor conditions, its cost efficiency, and the availability of various electrodes that can accommodate different metals.
Industrial Uses
Stick welding finds significant application in industrial settings. Many manufacturing facilities use it for fabrication and repair of heavy machinery. The robustness of stick welding allows welders to join thick metals, which is essential for constructing and maintaining equipment such as excavators, loaders, and dozers.
Moreover, stick welding is necessary in the infrastructure sector. It is often used in constructing bridges, buildings, and pipelines. The ability to weld in various positions adds to its favorability in projects that require different orientations, from vertical to overhead joins.
Another key industrial application is in shipbuilding. The marine industry heavily relies on stick welding for repairing and constructing vessels. The durability and penetration characteristics of stick welds are invaluable in these contexts, ensuring a strong bond capable of withstanding harsh marine environments.
Household and Repair Applications
Stick welding is also used in household and repair applications. For individuals working on DIY projects, the simplicity of stick welding makes it accessible. It is particularly effective for minor repairs of farm equipment and tools, which is crucial for agricultural farmers who need reliable equipment to maintain productivity.
In addition, stick welding caters to furniture and metal art projects. Enthusiasts utilize it for creating custom pieces or restoring older metal items. The low investment in equipment and materials makes it an attractive option for hobbyists.
Furthermore, stick welding can be employed for automotive repairs. Enthusiasts and professionals alike use this method for fabricating and welding components in cars. The ability to create strong welds on different metal thicknesses is vital in this field.
Stick welding's versatility plays a key role in both industrial and home settings, allowing for a range of applications from repairs to heavy construction.
In summary, the applications of stick welding are vast and varied. Its industrial uses showcase its importance in the manufacturing sector, while its household applications demonstrate accessibility for everyday users. As more individuals engage with various welding projects, understanding these applications becomes invaluable.
Future Trends in Stick Welding
Stick welding is an indispensable skill in various industrial and domestic applications. As the world becomes more advanced, the methods and technologies behind stick welding must also evolve. This section explores emerging trends and innovations that are shaping the future of stick welding. Understanding these trends is crucial for welders who seek to stay relevant in an increasingly competitive marketplace.
Technological Advancements
Technological progress is reshaping stick welding techniques and equipment. Recent advancements enhance both efficiency and safety in the welding process. New welding machines, such as inverter welders, now offer lightweight designs and improved control. These machines can automatically adjust settings and maintain stable arcs, which simplifies the welding process significantly.
In addition, digital technology plays a vital role. Many modern machines now include computerized interfaces. This allows for real-time monitoring of performance metrics, which helps welders to make informed decisions quickly. Furthermore, augmented reality and virtual reality applications are being utilized for training. This technology provides simulated welding environments where novices can practice their skills without the risks associated with working in a live environment.
As automation becomes prevalent in manufacturing, stick welding is also expected to embrace adaptation. Robotic welders can perform tasks with precision and speed. However, a skilled human welder is still essential for quality control and troubleshooting. Thus, the relationship between manual skills and automation continues to develop.
Sustainability Considerations
The welding industry is increasingly focused on sustainability due to environmental concerns. This trend is driving changes in materials and processes used in stick welding. Several companies are looking for eco-friendly electrodes and filler materials that reduce harmful emissions. For instance, manufacturers are now creating electrodes that produce less smoke and pollutants during the welding process.
Moreover, energy consumption is becoming a significant consideration. Innovative designs in equipment aim to reduce energy use without sacrificing performance. Techniques like regenerative braking and variable frequency drives facilitate energy efficiency, and this aligns with broader sustainability goals.
Lastly, recycling practices are being integrated into the welding process. Welders are encouraged to recycle scrap metal and use sustainable practices in their work. This not only reduces waste but can also decrease costs for businesses.
"Adopting sustainable practices not only fulfills corporate social responsibility but also offers economic benefits."
Overall, the future of stick welding will likely be marked by a balance between technological advances and sustainability efforts. Adapting to these trends will ensure welders are equipped with the best tools and practices for a changing world.
Epilogue
The conclusion of this article captures the essence of the skills and knowledge necessary for mastery in stick welding. Understanding the various elements discussed throughout the guide is critical for anyone looking to embark on this craft. Stick welding, while seeming straightforward, requires attention to detail, proper equipment, and safety practices to achieve precision and efficiency.
Summary of Key Learning Points
Throughout the article, several key points were highlighted. First, we covered the fundamental principles behind stick welding, such as the welding arc and the types of electrodes. This foundational knowledge is crucial, as it informs the choices made during the welding process. Second, the equipment necessary for effective stick welding was discussed, including machines and protective gear. Knowing what tools to use makes a significant difference in the quality of the welds produced. Additionally, safety considerations were emphasized, revealing how important it is to protect oneself and maintain a safe work environment.
"Understanding the essential components of stick welding is the first step in achieving proficiency in this valuable skill."
Finally, troubleshooting techniques were examined, helping welders identify and rectify common issues that may arise during the welding process thus ensuring a smoother workflow. Each section contributed to a broader understanding of how to effectively carry out stick welding tasks.
Encouragement for Ongoing Practice
Skill in stick welding is not attained overnight; it develops through continual practice and experience. It is recommended that readers engage with the material discussed, using each project as a learning opportunity. As one explores more complex welds and applications, the confidence in your techniques will increase. Participation in welding workshops or community groups can also provide the chance to learn from experienced welders.
Staying informed about advancements and methods in stick welding will further enhance skills. Regularly revisiting the fundamentals ensures that the techniques used remain sound. Remember, every welder, regardless of their level, should seek opportunities to engage with this craft. Ongoing education and practice are the keys to becoming proficient in stick welding. There is always room to improve, and each day presents a new chance to refine your skills.