Comprehensive Guide to Plywood Manufacturing
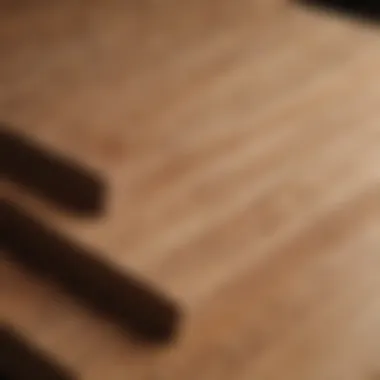
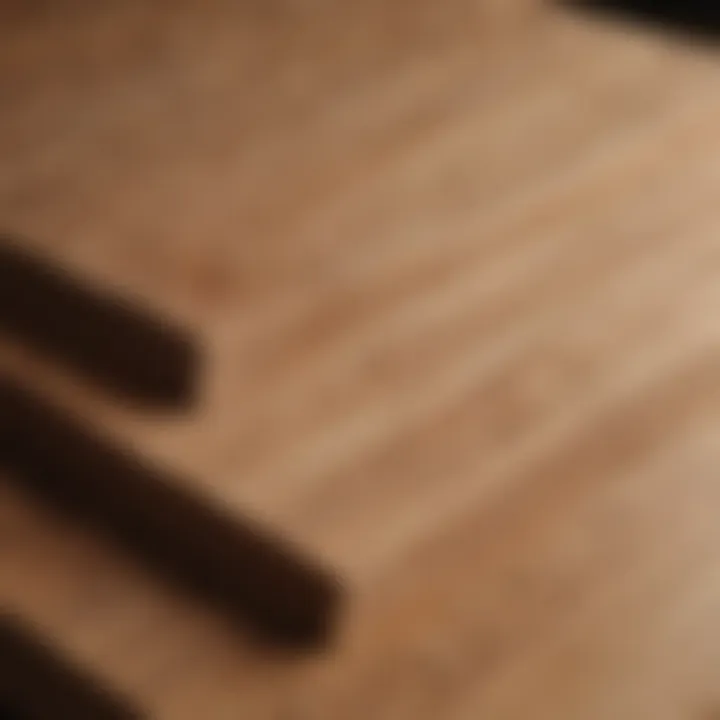
Intro
Plywood is an essential material widely used in construction, furniture making, and various applications in agriculture. Its unique construction and properties make it a versatile option for numerous projects. This article will provide a comprehensive overview of the intricate processes involved in plywood manufacturing. By examining materials, methods, quality standards, and future trends, we aim to provide valuable insights for agricultural professionals and enthusiasts.
Key Concepts and Terminology
Basic Definitions
To understand plywood manufacturing, it's crucial to define some key terms. Plywood is typically made by layering thin sheets of wood, known as veneers, which are glued together. Each layer is typically oriented in different directions to enhance strength and stability. The thickness of plywood can vary, influencing its applications.
Historical Context
The origins of plywood date back to ancient civilizations. Early forms of laminated wood can be seen in Egypt around 3000 BC. However, modern plywood, as we know it today, started becoming prevalent in the early 20th century. Advancements in adhesives and manufacturing techniques allowed plywood to gain popularity for its durability and cost-effectiveness across diverse industries.
Recent Innovations and Trends
Technological Advancements
In recent years, the plywood manufacturing process has seen significant innovations. CNC machines, which enhance precision and efficiency, have become staples in many plants. Furthermore, advancements in adhesive technology have allowed for stronger bonds and better moisture resistance, crucial for outdoor applications.
Sustainable Practices
The plywood industry is increasingly focusing on sustainability. Many manufacturers are now sourcing wood from certified forests, ensuring responsible forest management. Recycled materials are also being utilized to create plywood, reducing waste and the carbon footprint of production.
Practical Applications and Techniques
Step-by-step Guides
The manufacturing of plywood involves several key stages:
- Log Selection: The process begins with selecting suitable logs, which are debarked and cut into manageable lengths.
- Veneer Production: Logs are sliced into thin sheets, usually resulting in multiple layers of veneer from each log.
- Drying: These veneers are then dried to the appropriate moisture content to prepare for gluing.
- Gluing: Adhesives are applied to the layers, ensuring effective bonding.
- Pressing: The layered veneers are placed in hot presses to cure the glue, forming a solid panel.
- Finishing: The final stage includes sanding and cutting the plywood to required specifications.
Case Studies
An example of innovative plywood use can be seen in agricultural applications. Companies are now using plywood for durable storage solutions, ensuring protection from weather elements. These solutions not only maintain the integrity of stored goods but also showcase the materialβs versatility.
The plywood industry is critical not just for construction but also for agricultural advancements. Proper understanding of its manufacture can lead to better quality applications, ensuring longevity and sustainability.
In summary, understanding the manufacture of plywood involves knowing its essential definitions, historical journey, recent innovations, and practical applications. With a focus on sustainable practices and technological advancements, the plywood industry continues to evolve, offering vast potential for both building and agricultural needs.
Foreword to Plywood
Plywood is pivotal in various industries due to its strength, versatility, and adaptability. The significance of this material is evident in everything from construction to furniture making. Understanding the nuances of plywood production is essential for those involved in agriculture, construction, and manufacturing. This guide will provide insights into the intricate processes that define plywood manufacturing, revealing both its historical context and contemporary relevance.
Definition and Importance
Plywood is a composite material made from thin layers of wooden veneer, bonded together to create sheets. This unique construction method gives plywood exceptional stability, strength, and resistance to warping. Its importance cannot be overstated, as it serves a multitude of applications:
- Structural Uses: Plywood is a preferred choice in building structures due to its superior load-bearing capabilities.
- Furniture Manufacturing: Many furniture pieces, especially affordable ones, utilize plywood for both aesthetic and practical reasons.
- Transport and Packaging: Plywood is often chosen for crates and shipping containers because of its durability.
The value of plywood lies in its ability to combine the natural beauty of wood with engineered resilience, making it indispensable in various sectors.
Historical Context
The origins of plywood can be traced back thousands of years. Ancient cultures in regions like Egypt and China used layered wood assemblies. However, the modern plywood we recognize today began to take shape in the late 19th century.
In 1865, the first patent for a plywood manufacturing process was registered in the United States. The early facilities produced plywood using simple methods, primarily targeting the furniture sector. As the 20th century progressed, advancements in adhesive technology and machinery transformed plywood production. The material gained popularity during both World Wars for military applications, further cementing its significance.
Today, plywood is a worldwide commodity, produced in various grades and types to meet diverse needs. Innovations in manufacturing continue to enhance quality and sustainability, ensuring that plywood remains a vital material well into the future.
Plywood Composition
Understanding the composition of plywood is crucial as it lays the ground for its durability, appearance, and overall performance. Plywood is made from multiple layers of wood veneer, bonded together through adhesives. This layer structure gives plywood its unique strength and versatility.
Types of Wood Used
Softwoods
Softwoods are commonly utilized in plywood production because of their lightweight and ease of use. They are harvested from conifer trees, which include species such as pine, fir, and spruce. One key characteristic of softwoods is their tendency to be less dense compared to hardwoods. This quality makes them suitable for applications that do not require heavy load bearing. Softwoods are advantageous due to their lower cost and availability. However, they might lack some of the aesthetic features found in hardwoods, which can be a downside for certain finishing applications.
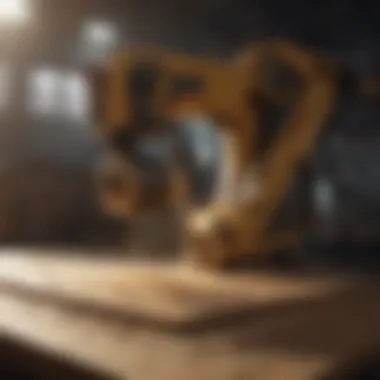
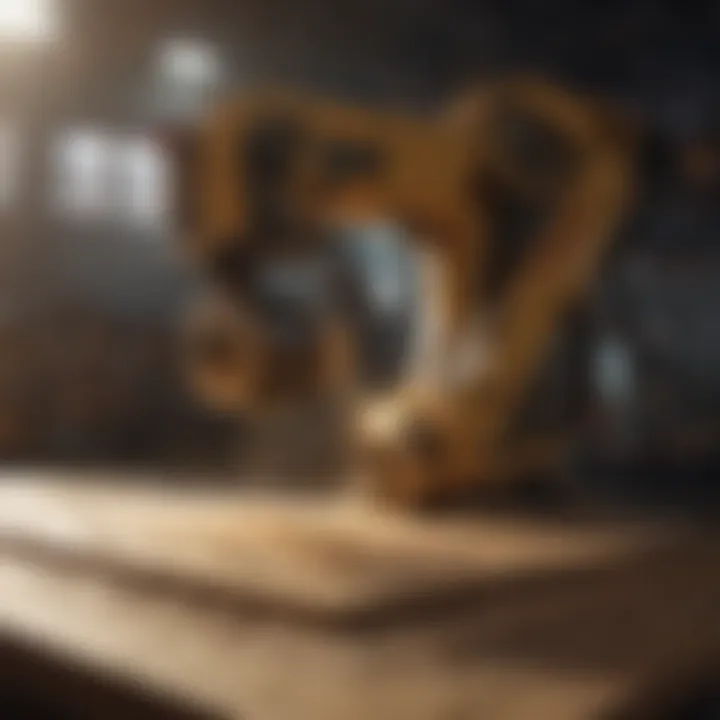
Hardwoods
Hardwoods come from deciduous trees and often bring higher durability and density to plywood products. Species like oak, birch, and maple are common in this category. The main advantage of hardwoods is their strength and rich appearance, which can enhance the visual aspect of the plywood. These woods tend to resist wear and tear better than softwoods, making them suitable for applications needing longevity. However, they are generally more expensive and their processing can require more energy and resources.
Engineered Woods
Engineered woods, like MDF and particleboard, offer unique benefits in plywood construction. They consist of wood fibers, strands, or veneers that are bonded together with adhesives. A significant characteristic of engineered woods is their uniformity and resilience against warping. They provide a cost-effective option in situations where high-end hardwood or softwood may not be necessary. Despite their advantages, they can sometimes be less appealing visually and may not perform as well as natural woods in specific environments.
Adhesives and Chemicals
Types of Adhesives
The types of adhesives used in plywood are fundamental to its durability and performance. Commonly utilized adhesives include urea-formaldehyde, phenol-formaldehyde, and polyvinyl acetate. Each adhesive has distinct properties that make it suitable for various applications. For instance, phenol-formaldehyde is known for its moisture resistance, making it ideal for exterior plywood. The choice of adhesive impacts the final product's strength and durability.
Environmental Considerations
Environmental concerns have gained much attention in recent years, and this influences plywood composition significantly. Using low-emission adhesives and sustainable wood sources is increasingly viewed as a necessity. These environmental considerations are important not only for regulatory compliance but also for market appeal. Many consumers are now more inclined to choose products that are sustainably made. Moreover, companies focusing on eco-friendly practices may face fewer regulatory hurdles and achieve a competitive edge in the plywood industry.
Manufacturing Process Overview
The manufacturing process of plywood is a complex interplay of various stages that transform raw timber into a versatile construction material. Understanding this process is integral to appreciating the quality and durability of plywood. Each step influences the final characteristics of the product, from strength and stability to aesthetic appeal. This section will explore the detailed journey of plywood from log to finished product, emphasizing the significance of each phase.
Harvesting and Log Preparation
The first step in plywood production is harvesting the logs. This involves selecting suitable trees, often based on species and health. Softwoods like pine and hardwoods like birch are commonly preferred for their properties. After cutting down the trees, logs are transported to the mill. Here, log preparation occurs where logs undergo debarking and are cut into manageable lengths. The aim is to prepare high-quality raw materials for the next stages of manufacturing, ensuring minimal waste and maximizing efficiency.
Rotary Cutting and Slicing
Rotary cutting is a crucial technique in plywood manufacturing. Logs are mounted on a lathe and rotated against a sharp blade. This process peels off thin sheets of veneer, maximizing the use of the log. Alternatively, slicing can also be used, where logs are cut lengthwise, producing thicker veneers. This method allows for enhanced grain patterns. Both techniques create the veneer sheets needed for plywood laying.
Drying Techniques
The veneer sheets must be dried to remove excess moisture. This step is vital for preventing future warping and mold. Drying techniques vary, and two primary methods are often utilized: conventional drying and kiln drying.
Conventional Drying
Conventional drying involves air-drying the veneer sheets in a controlled environment, where natural airflow helps in moisture reduction. Its main characteristic is simplicity, allowing producers to utilize less energy compared to more advanced methods. However, this method can take significant time and is weather-dependent. For those seeking an economical yet effective solution, conventional drying serves as a substantial choice despite its slower operation.
Kiln Drying
Kiln drying employs heated chambers to accelerate the moisture removal process of the veneer sheets. This method stands out for its efficiency; it significantly reduces the drying time compared to conventional drying. Kiln drying allows for precise control of temperature and humidity, leading to uniform moisture levels in the veneers. It also helps in minimizing the risk of defects, such as warping or cracking. However, the initial energy requirements may be higher, making it a more costly option in some cases.
Glue Application
After drying, glue is applied to the veneers. The choice of adhesive is critical as it affects the performance and durability of the plywood. Different types of adhesives serve varying needs, with some tailored for specific applications such as exterior use. The glue must cover the surfaces evenly to ensure strong bonding. Proper application techniques are essential to maintain the integrity of the plywood.
Pressing and Curing
Once adhesive application is complete, the veneers are assembled into layers and placed in a hydraulic press. Pressing not only applies uniform pressure across the panels but also activates the adhesive, starting the curing process. This step solidifies the bonding and shapes the plywood into its final form. Factors like pressure and time are monitored closely to ensure optimal results.
Trimming and Quality Check
The final step in plywood manufacturing involves trimming the edges and performing a thorough quality inspection. Panels are cut down to specified dimensions, and defects are identified and rectified. Quality checks ensure that each sheet meets industry standards, examining aspects like thickness, flatness, and overall finish. Such meticulous attention to detail guarantees that the plywood will perform reliably in various applications.
Types of Plywood
Understanding the various types of plywood is crucial in the context of this article, as each type serves different purposes and comes with distinct characteristics. These characteristics influence not only the functionality but also the performance and durability of plywood in various applications. Evaluating specific elements, benefits, and considerations surrounding each type can guide consumers in making the most informed choices.
Exterior Plywood
Exterior plywood is designed to withstand harsh weather conditions. This type means it has a high resistance to moisture and extreme temperatures. It often employs special waterproof adhesives and is made from resilient wood species that can endure outdoor elements. Typically, the surface is treated or finished with protective coatings to enhance durability against rain, snow, and sun exposure.
This type of plywood is ideal for construction projects such as sheds, outdoor furniture, and deck platforms. When selecting exterior plywood, itβs important to consider the intended application. For example, structural plywood used in building facades must meet specific standards to ensure safety and longevity.
Interior Plywood
Interior plywood is primarily used for indoor applications. It is not exposed to severe weather conditions, allowing for a variety of wood types that may not resist moisture as well as exterior grades. Common uses include cabinetry, furniture, and paneling.
The choice of interior plywood often revolves around aesthetic preferences and structural requirements. The veneers can be chosen for their finish, with options like oak or birch providing a fine appearance for visible installations. Importantly, interior plywood must comply with indoor air quality standards, which can include measures against the emissions from adhesives used in manufacturing.
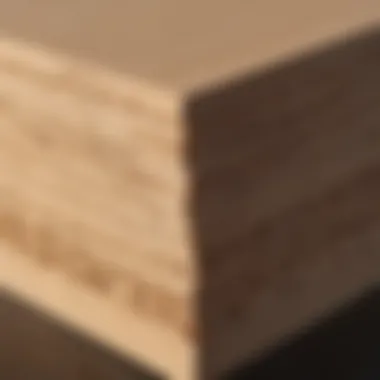
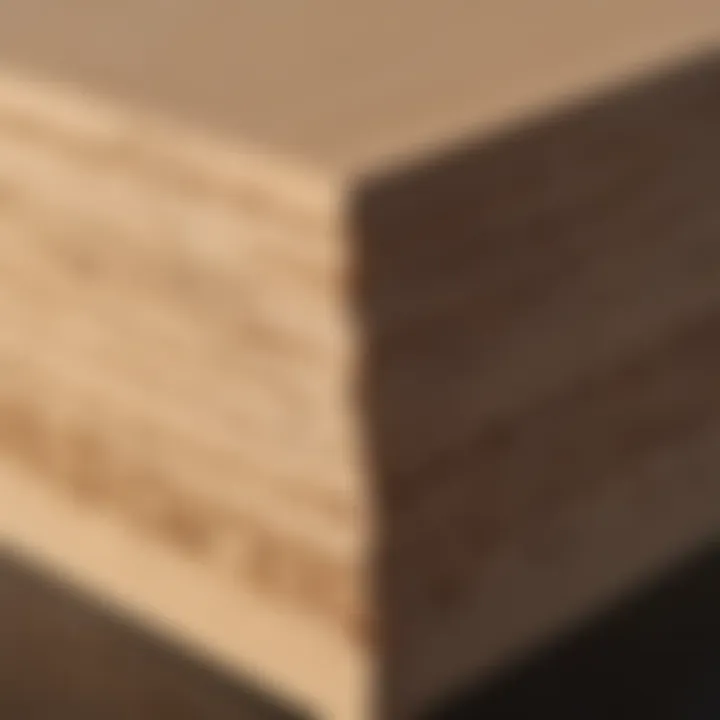
Marine Plywood
Marine plywood stands as the premium choice for applications requiring maximum durability in moist environments, particularly marine settings. Unlike regular plywood, marine plywood is made using highly waterproof adhesive and is manufactured to a higher standard concerning the quality of veneer. This type of plywood is typically void-free, reducing the risk of delamination and ensuring increased strength over time.
This kind of plywood finds its use in boat building, docks, and other settings where water exposure is a continuous challenge. Due consideration must be given to the specifications to ensure that the plywood adheres to marine-grade standards, which vary by region and application. As environmental concerns collect momentum, selecting sustainably sourced marine plywood can also align with eco-friendly practices in the industry.
"Choosing the right type of plywood is essential not just for structural integrity but also for the longevity and appearance of the final product."
By understanding the differences between the various types of plywood, consumers and manufacturers can better navigate their options and make choices that align with their project's specific needs.
Quality Control in Plywood Production
Quality control plays a critical role in the plywood manufacturing process. It ensures that the final product meets specific standards and is fit for consumer use. The importance of quality control spans various aspects of production, from the initial choice of materials to the final inspection of the sheets before they leave the factory.
Implementing a rigorous quality control system provides several benefits. It reduces waste by identifying defects early in the production line. This not only saves on materials but also on labor costs associated with rework. Furthermore, consistent product quality enhances customer satisfaction and fosters trust in the brand.
Standards and Regulations
Adhering to industry standards and regulations is an essential component of plywood quality control. Various organizations develop these standards to ensure safety, performance, and environmental responsibility. Industry standards may include guidelines regarding the thickness, bonding strength, and moisture content of plywood sheets.
In many countries, adherence to these standards is not just recommended; it is mandatory for manufacturers. For example, the American Plywood Association (APA) has established performance standards that manufacturers must comply with in order to label their product as compliant.
Testing Methods
The testing methods used in quality control are divided into two main categories: physiological tests and chemical tests. Each method serves to evaluate different properties of plywood, ensuring that products meet performance expectations.
Physical Tests
Physical tests are crucial for assessing the structural integrity of plywood. These tests measure the strength, flexibility, and durability of the material under various conditions. The most common physical tests include the following:
- Bending Strength Test: Determines how much weight plywood can bear before breaking.
- Humidity Resistance Test: Evaluates the plywoodβs ability to withstand changes in moisture levels.
The key characteristic of physical tests is their focus on performance in practical applications. These tests are valuable because they simulate actual use conditions, making them a beneficial choice for determining plywood reliability. Their unique feature lies in their ability to provide empirical data, leading to informed decisions about material usage and expected lifespan. However, physical tests can be time-consuming and may require specialized equipment.
Chemical Tests
Chemical tests assess the composition of the plywood, particularly regarding adhesives and preservatives used in production. These tests evaluate the off-gassing properties of chemicals within the plywood, ensuring they meet health and safety guidelines.
Common chemical tests include:
- Formaldehyde Emission Test: Measures the level of formaldehyde released from plywood, ensuring it falls within acceptable limits.
- Retention of Preservatives Test: Checks the effectiveness of chemicals used to prevent rotting or insect damage.
The main characteristic of chemical tests is their focus on safety and environmental impact. They are essential for compliance with regulations that protect both consumers and the environment. The unique feature of chemical tests is their ability to identify potentially harmful substances, which ensures that products are non-toxic and safe for use. Nonetheless, these tests can be complex and involve rigorous laboratory procedures.
Quality control in plywood production is not merely a regulatory requirement; it is a commitment to excellence that shapes industry standards.
Technological Innovations
Technological innovations play a significant role in the manufacture of plywood. They enable manufacturers to improve efficiency, reduce waste, and enhance product quality. An increased focus on technology has brought forward equipment and processes that streamline various aspects of production. Automation and sustainable practices are two key components driving these innovations in the plywood industry.
Automation in Manufacturing
Automation in manufacturing has transformed how plywood is produced. It reduces the manual labor required at various stages of the production process. Machinery can perform cutting, gluing, and pressing at a faster and more consistent rate than human labor. This leads to faster production times and a decrease in errors that can occur during manual handling.
Moreover, automation enhances precision and reduces material waste. Equipment like computerized numerical control (CNC) machines allow for highly accurate cuts and optimizes the use of raw materials by maximizing yield. Quality control measures can also be automated, ensuring that every sheet meets the required standards. In summary, automation directly contributes to increased efficiency, reliability, and product quality in plywood manufacturing.
Sustainable Practices
Sustainable practices are increasingly being incorporated into the plywood manufacturing process. This reflects a growing awareness of the environmental impact of production. There are two significant elements of sustainable practices worth considering: recycled materials and eco-friendly adhesives.
Recycled Materials
Recycled materials are gaining traction in plywood manufacturing. The use of wood scraps, offcuts, and other by-products reduces waste and decreases the demand for new timber. One of the key characteristics of recycled materials is their lower environmental impact compared to virgin materials. This makes them a popular choice among more environmentally conscious consumers.
A unique feature of recycled materials is their versatility. They can often be repurposed into various plywood products, contributing to the circular economy. While incorporating recycled materials can lead to quality challenges, advancements in processing technology have mitigated these risks. Therefore, the benefits of using recycled materials often outweigh the potential downsides.
Eco-Friendly Adhesives
Eco-friendly adhesives represent a shift towards more sustainable bonding solutions in plywood manufacturing. These adhesives contain fewer harmful chemicals compared to traditional options, which can emit volatile organic compounds (VOCs). Their main advantage is the reduced health risks for workers and consumers, making them increasingly attractive.
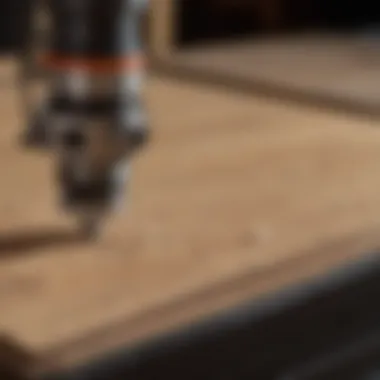
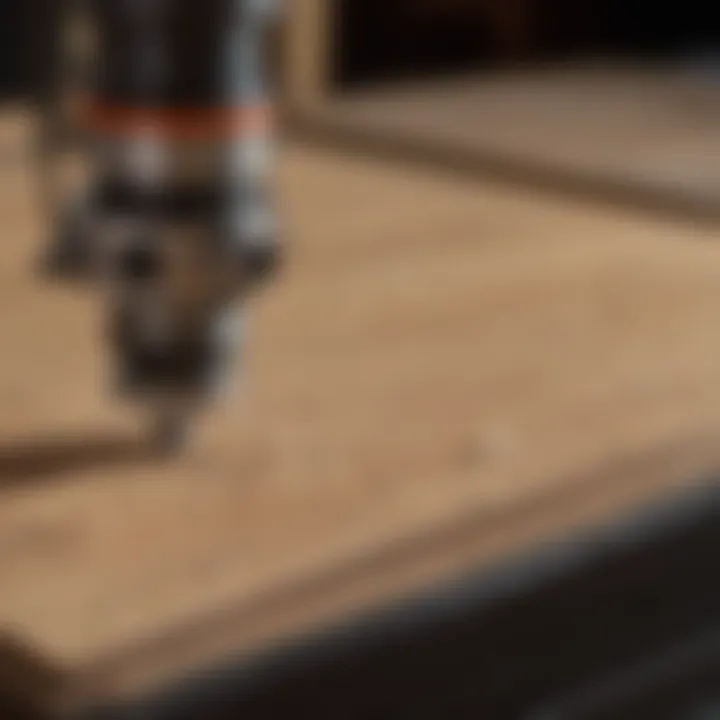
These adhesives are typically derived from sustainable sources, such as plant-based materials. A distinguishing feature is their ability to maintain strong bonds while being less harmful to the environment. However, some eco-friendly adhesives may have limitations in terms of heat resistance or water resistance compared to conventional adhesives. Despite this, their benefits make them an important aspect of modern plywood production practices.
"Innovations in automation and sustainability are reshaping the plywood industry, offering new solutions for environmental responsibility and efficiency."
Overall, technological innovations, particularly in automation and sustainable practices, represent crucial advancements in plywood manufacturing. They enhance productivity and promote environmentally conscious approaches that are favorable for the industry and the planet.
Challenges Facing the Plywood Industry
The plywood industry encounters several significant challenges that impact its operations and growth. Addressing these challenges is crucial for sustaining production levels and maintaining the quality of plywood products. It is essential to understand the challenges since they affect how raw materials are sourced, processed, and delivered to the end-user. The industry needs to adapt and innovate to overcome these obstacles, ensuring long-term viability.
Supply Chain Issues
The plywood supply chain is complex and involves numerous players. Lumber mills, suppliers of adhesives, and transportation providers must work seamlessly together to deliver finished products to consumers. Disruptions in this chain can lead to delays and increased costs.
One major issue is the shortage of high-quality timber due to deforestation and overharvesting. Plywood manufacturers often face difficulties in sourcing sustainable wood species. This impacts overall production, as raw materials become scarce or too expensive. In addition, logistic challenges, such as fluctuating fuel prices and transportation bottlenecks, can hinder the timely movement of goods.
- Increasing Costs: Rising prices in transport can lead to higher operating costs for companies.
- Sourcing Challenges: Difficulty in finding reliable suppliers can lead to inconsistencies in product quality.
Companies also need to anticipate demand shifts. Adapting to market trends quickly can be challenging when relying on various suppliers. Thus, a robust and flexible supply chain is indispensable to navigate these complexities effectively.
Environmental Regulations
The plywood industry also faces stringent environmental regulations that aim to protect forests and ecosystem health. As awareness about climate change grows, regulatory bodies enforce stricter guidelines on wood harvesting practices. Companies must ensure compliance with these regulations to avoid penalties and maintain their reputations.
These regulations often demand more from manufacturers in terms of sustainable practices. They must show that they are sourcing timber responsibly and minimizing waste in production. This incorporates using eco-friendly adhesives and chemicals in the process. Notably, the requirement to obtain certifications, such as the Forest Stewardship Council (FSC) certification, can be cumbersome for smaller businesses but is essential for legitimacy in the market.
- Compliance Costs: Meeting environmental standards often entails a significant monetary investment.
- Consumer Demand: There is a growing preference among consumers for sustainable products, which adds pressure on manufacturers to enhance their environmental practices.
"Sustainability is not just an option; itβs a necessity for survival in todayβs plywood market."
Failure to adapt to these regulatory requirements can lead to litigation or loss of market access. Thus, the industry must innovate and invest in sustainable practices to remain competitive while aligning with regulatory expectations.
Future Trends in Plywood Manufacturing
As the plywood manufacturing sector evolves, it becomes essential to understand the future trends shaping its trajectory. These trends are significant not only for manufacturers but also for consumers and stakeholders in the industry. Greener practices, technological advancements, and changing market dynamics are interconnected factors driving changes in plywood production. Understanding these elements helps industry players to adapt and innovate more effectively.
Market Demand and Growth
The demand for plywood continues to experience fluctuation, influenced by various sectors such as construction, furniture making, and interior decorations. As urbanization increases globally, more structures are built, leading to a greater need for durable and aesthetic materials. As a result, plywood becomes a staple choice due to its strength-to-weight ratio and versatility.
Market research indicates positive growth for plywood, with projections showing an increased demand for both residential and commercial applications. There is also a noticeable shift towards environmentally friendly plywood options, which are made of sustainably sourced materials. Organic certifications and eco-labeling are major selling points, making this segment more appealing to environmentally conscious consumers.
One notable trend is the adaptation to regional preferences. For instance, in Northern Europe, designers are moving towards lighter wood tones, while in North America, darker finishes may be favored for interior use. This reflects not just aesthetic preferences but also a cultural inclination toward design styles that differ by region.
"Plywood is not merely a building material; it is a canvas for creativity and innovation."
Emerging Technologies
The rise of new technologies is significantly transforming plywood manufacturing. Automation plays a crucial role in enhancing production efficiency and reducing labor costs. Automated machinery is capable of more precise cuts and improved glue application, ensuring better quality panels.
Furthermore, advances in software technology have led to better inventory management and logistics. This allows manufacturers to respond quicker to market demands and optimize supply chains. For example, using data analytics, companies can predict the types and quantities of plywood needed based on historical sales data.
Sustainable technologies are also gaining traction in plywood manufacturing. Innovations include bio-based adhesives that reduce reliance on formaldehyde and other harmful chemicals. Companies now explore recycled materials to manufacture plywood, significantly reducing waste and promoting circular economy principles.
Overall, the convergence of demand for sustainable products and the incorporation of advanced technologies can lead to a resilient plywood industry. Companies that embrace these trends will likely hold a competitive edge in the marketplace.
The End
The conclusion section is crucial in summarizing the entire article on plywood manufacturing. It brings together various elements discussed throughout the document, highlighting key insights and reinforcing the relevance of plywood in multiple industries. By reiterating the processes, materials, and standards involved, the conclusion serves as a final reminder of the complexities and significance of plywood.
In the world of construction, furniture making, and design, plywood is indispensable. Its versatility makes it suitable for various applications. The durability of different types of plywood also ensures that it meets industry standards for safety and performance. Recognizing these elements emphasizes the need for continuous innovation and adherence to quality control standards in the plywood manufacturing sector.
Aside from its immediate benefits, understanding the implications of plywood manufacturing extends into broader environmental considerations. As sustainability becomes more critical, the industry must adapt to better practices. The use of eco-friendly adhesives and renewable resources must remain a priority.
"Plywood's application range underscores its importance in modern construction while inviting ongoing improvements in manufacturing practices."
Summary of Key Points
- Plywood Composition: Plywood is made from various types of woods including softwoods, hardwoods, and engineered woods, bonded with adhesives.
- Manufacturing Process: The process involves harvesting, preparing logs, rotary cutting, drying, applying glue, pressing, and quality checks.
- Types of Plywood: Different grades such as exterior, interior, and marine plywood serve specific needs based on environmental conditions.
- Quality Control: Strict standards and testing methods ensure that plywood meets both safety and performance benchmarks.
- Technological Innovations: Automation and sustainable practices are transforming the manufacturing landscape, driving efficiency and ecological responsibility.
Implications for the Future
The future of plywood manufacturing hinges on several interlinked factors. Increasing demand for eco-friendly construction materials is likely to drive a substantial shift in production methodologies. The industry is seeing a surge in interest regarding sustainable resources. The use of recycled materials and the development of bio-based adhesives present significant opportunities for growth.
Moreover, technological advances will likely continue to reshape how plywood is produced. Innovations such as automated cutting and pressing systems can improve accuracy and reduce waste. Looking ahead, companies must prioritize research and development. This focus will help address challenges from climate change and resource scarcity.
In summary, the implications of these trends suggest a vibrant future for the plywood industry, one that balances efficacy with environmental stewardship.